filmov
tv
Are Solder Seal Connectors BETTER than Butt Splices? (the truth)
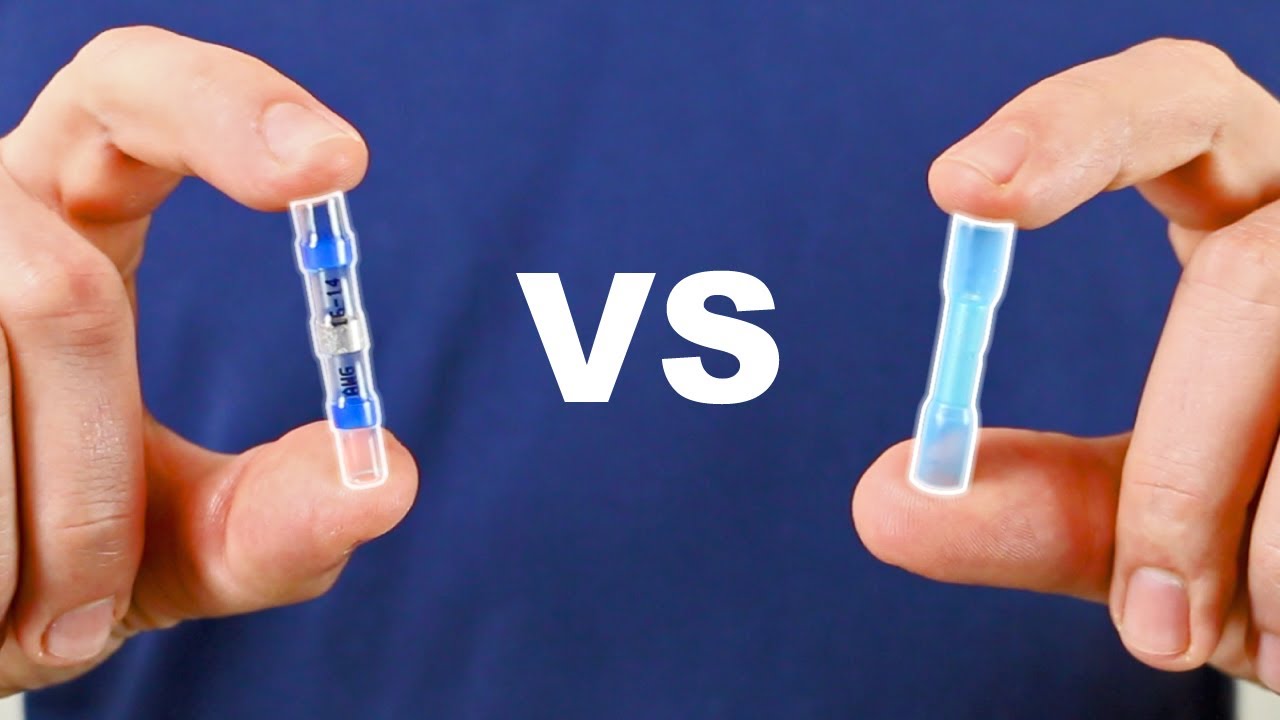
Показать описание
Amazon's #1 Best Selling Solder Seal Connector Any Good? Find Out!
Are Solder Seal Connectors BETTER than Butt Splices? (the truth)
Solder Seal Wire Connectors Review - Are They Any Good? - Shop Talk
Solder Seal Wire Connectors - Are They Any Good? - Was I Wrong?
How to Use Solder Seal Heat Shrink Butt Connectors
Heat shrink solder butt connector test.
How to use solder seal wire connectors?
The 5 Best Solder Seal Wire Connectors in 2023
The 5 Best Solder Seal Wire Connectors Of 2023
SOLDER & SEAL THE BEST WIRE CONNECTORS I HAVE FOUND
How to Use Solder Wire Connector Kit to Connect Wire 2021
Which Wire Connector is BEST?
Do these Marine (Solder Seal) Connectors WORK? Tested on my BMW...
Solder seal wire connector / Test & review
Better than butt splices - check out 'Solder Seal' splice from Haisstronica
Solderstick Waterproof Easy Solder Wire Connector
How To Use Solder Seal Wire Connectors
Solder Seal Heat Shrink Waterproof Wire Connectors - Review
Why you should NEVER solder wires on your car.
Solder Seal Connectors WORTH IT??
Amazon's Easy to use Solder Seal Connector Any Good? Find Out!
Wirefy Solder Seal Wire Connectors
Adam Savage's Quick Electronics Wiring Tips!
Solder Seal Wire Connectors Kit
Комментарии