filmov
tv
Solder seal wire connector / Test & review
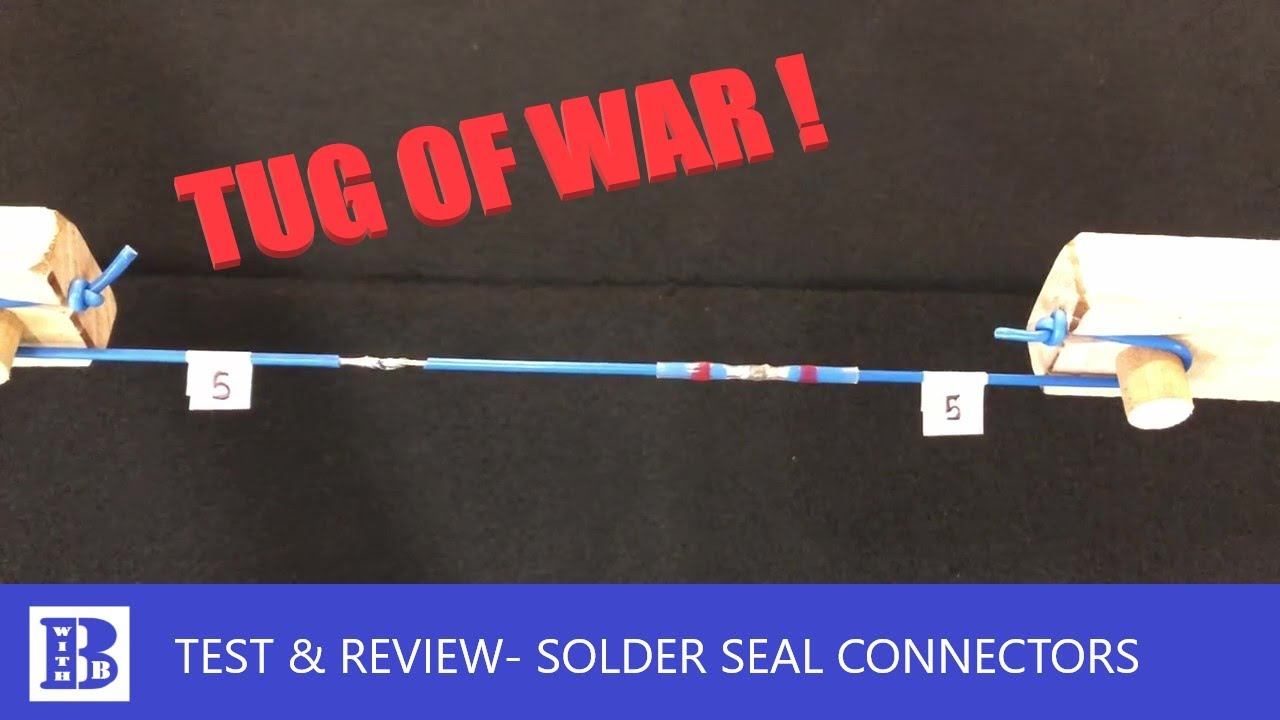
Показать описание
In this video I test & review solder seal wire connectors, also known as heat shrink wire connectors.
if you need to splice wires and don't have or want to use a solder gun then you want to watch this.
Although not new to the market, they are an often overlooked option for the Do it yourself type or even a pro when splicing wires.
They look like a great idea, but do they pass the test ?
As an Amazon Associate I earn from qualifying purchases,
using the links provides does not in any way increase the cost to you, however any income I get from them helps support my channel...thanks
if you need to splice wires and don't have or want to use a solder gun then you want to watch this.
Although not new to the market, they are an often overlooked option for the Do it yourself type or even a pro when splicing wires.
They look like a great idea, but do they pass the test ?
As an Amazon Associate I earn from qualifying purchases,
using the links provides does not in any way increase the cost to you, however any income I get from them helps support my channel...thanks
Amazon's #1 Best Selling Solder Seal Connector Any Good? Find Out!
How to Use Solder Seal Heat Shrink Butt Connectors
How to use solder seal wire connectors?
Heat shrink solder butt connector test.
Solder Seal Wire Connectors Review - Are They Any Good? - Shop Talk
Solder Seal Wire Connectors - Are They Any Good? - Was I Wrong?
How To Use Solder Seal Wire Connectors
Solder Seal Heat Shrink Waterproof Wire Connectors - Review
Solder seal wire connector / Test & review
Are Solder Seal Connectors BETTER than Butt Splices? (the truth)
Heat Shrink Self-Solder Butt Splice Connectors
Adam Savage's Quick Electronics Wiring Tips!
Heat Shrink Solder Seal Wire Connector
Solderstick Waterproof Easy Solder Wire Connector
SOLDER SEAL WIRE CONNECTORS
Never Solder Again - How to Connect Wires the EASY Way
Which Wire Connector is BEST?
How to SOLDER WIRES TOGETHER - PRO TIPS for WATERPROOF CONNECTIONS
Why you should NEVER solder wires on your car.
Using Solder Seal Heat Shrink Butt Connectors
SOLDER & SEAL THE BEST WIRE CONNECTORS I HAVE FOUND
How To Make A WATERPROOF Wire Solder Connection! EASY DIY Solderstick
Heat Shrink Solder Butt Connectors TEST - Wire Connectors
Self Soldering Butt Splice Heat Shrink Connectors
Комментарии