filmov
tv
Solder Seal Wire Connectors - Are They Any Good? - Was I Wrong?
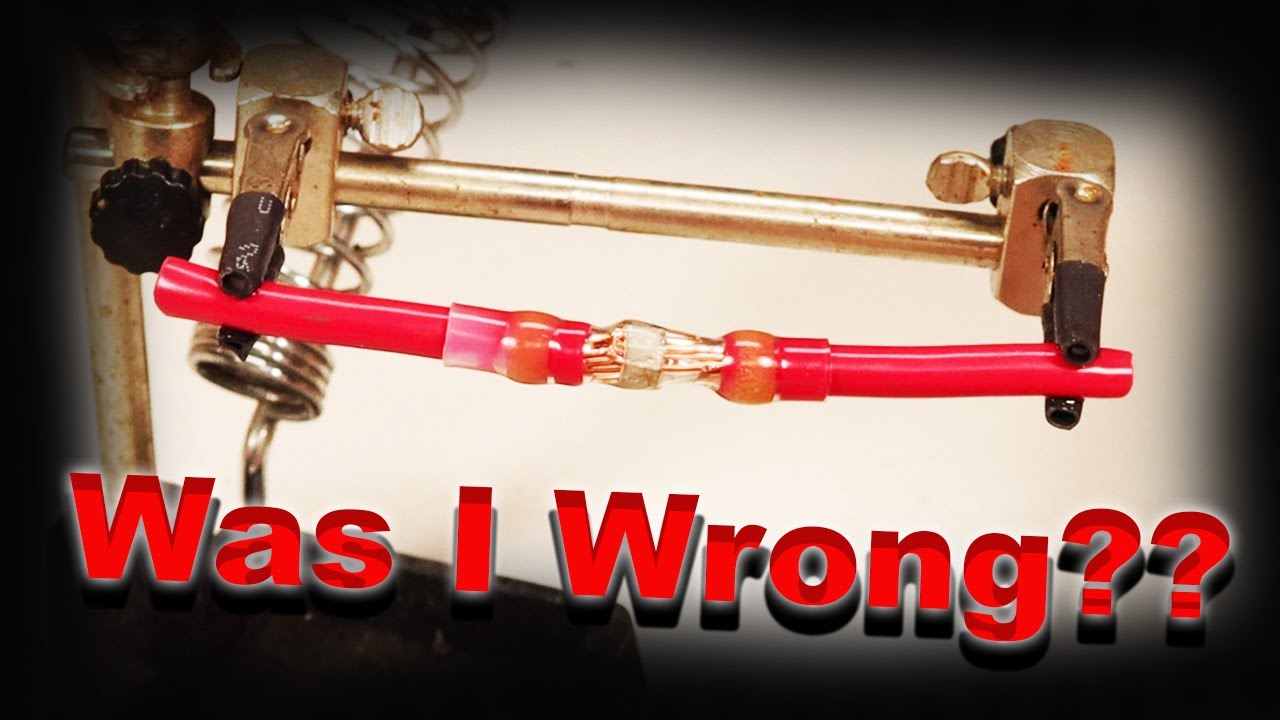
Показать описание
Last year we put out a video reviewing the solder seal connectors we picked up from Facebook marketplace and got a lot of heat from YouTube for what we said. We figured we give them another shot, so here it goes.
Want to learn how to solder? Check out her soldering videos here:
This video was sponsored by Skillshare
As an Amazon Associate, I earn from qualifying purchases. Clicking on the links above helps support the channel and helps us provide you with more quality content. We thank you for your support.
Want to learn how to solder? Check out her soldering videos here:
This video was sponsored by Skillshare
As an Amazon Associate, I earn from qualifying purchases. Clicking on the links above helps support the channel and helps us provide you with more quality content. We thank you for your support.
Amazon's #1 Best Selling Solder Seal Connector Any Good? Find Out!
How to Use Solder Seal Heat Shrink Butt Connectors
How to use solder seal wire connectors?
Solder Seal Wire Connectors Review - Are They Any Good? - Shop Talk
Solder Seal Wire Connectors - Are They Any Good? - Was I Wrong?
Heat shrink solder butt connector test.
How To Use Solder Seal Wire Connectors
Solder seal wire connector / Test & review
10 DIY Halloween Lighting Upgrades!
Solder Seal Heat Shrink Waterproof Wire Connectors - Review
SOLDER & SEAL THE BEST WIRE CONNECTORS I HAVE FOUND
Kuject 120PCS Solder Seal Wire Connectors WT001 Review
Heat Shrink Solder Seal Wire Connector
Heat Shrink Self-Solder Butt Splice Connectors
Solderstick Waterproof Easy Solder Wire Connector
Heat Shrink Solder Butt Connectors TEST - Wire Connectors
The 5 Best Solder Seal Wire Connectors in 2023
Does Solder Seal Work? - Splice, Solder, and Heat Shrink Wires ALL-IN-ONE?
Wirefy Solder Seal Wire Connectors
Which Wire Connector is BEST?
How To Use Solder Seal Wire Connectors
The 5 Best Solder Seal Wire Connectors Of 2023
Are Solder Seal Connectors BETTER than Butt Splices? (the truth)
Do these Marine (Solder Seal) Connectors WORK? Tested on my BMW...
Комментарии