filmov
tv
What are PID Tuning Parameters?
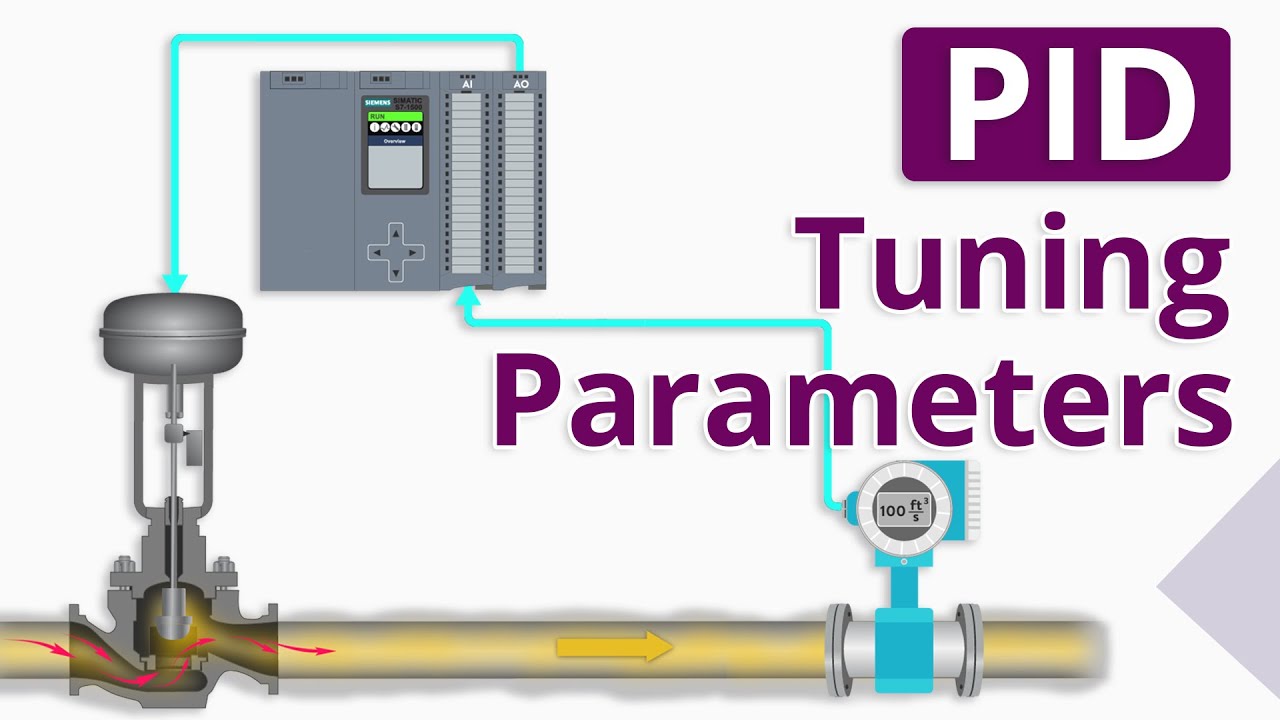
Показать описание
=============================
▶ Check out the full blog post over at
=============================
⌚Timestamps:
00:00 - PID Introduction
00:59 - PID Temperature Control
03:06 - Closed/Open-Loop Control
04:24 - Gas Flowrate PID Control
=============================
PID is an acronym for Proportional, Integral, and Derivative. A PID controller is a device that is used to control a process.
The controller can be a physical, stand-alone device or a control block found in a PLC function database.
The PID portion of the controller is a series of numbers that are used as adjustments in order to achieve your objective.
A very simple example of a PID controller would be the regulation of a heating and air conditioning system in a home.
Although there is a lot more to the controller than this example, this will give you a basic idea of the purpose of a device like this.
Consider that you have the temperature in your home set to 70 degrees Fahrenheit. This setting would be called the Setpoint or “SP” for short.
The current reading from the thermostat is 68 degrees Fahrenheit. This term is the Process Variable or “PV”. The heating or cooling unit is the Control Variable or “CV”. The Control Variable may also be referred to as the Manipulated Variable or “MV”.
There are different types of control action and for the temperature control in the house, the controller action is a direct-acting device meaning that the calculations are Setpoint minus Process Variable (SP-PV).
In our house example, we have a SetPoint of 70 and the Process Variable is 68 degrees Fahrenheit.
For this control when we subtract the Process Variable from the SetPoint we see that we have a value of 2. This result is called the Error or “E” in our process.
In the simplest terms, our house is too cool and the controller tells the heating unit to turn on. Remember, we are trying to get to 70 degrees. The unit will remain ON until the Error in our process becomes zero.
Now let’s say that someone opens a window in the house and it’s very cold outside. This disruption in the process is called Disturbance.
The factors in this process control may be:
- “How fast do we want the temperature to reach the setpoint”.
- “What could disturb our process”?
Clearly, there are many factors that can impact our processes and adjusting our controller’s parameters is how we deal with those factors.
In an industrial plant, since there are many factors that we need to consider, we need a robust controller that takes our parameters into account and does hundreds of calculations to determine where the process is and where it needs to go.
Say we need to control gas flow through a pipe. The Setpoint of gas flow is calculated based on a calculation of some factors. This Setpoint can change at any time based on the parameters used in the calculation.
We will control this flow based on a modulating valve. In this case, the more open the valve, the more gas allowed to flow. The requested position of the valve is our Control Variable.
Downstream of this modulating valve we have a flow meter that will measure the gas flowing through the pipe, this is our feedback or our Process Variable.
Let’s take a step back and talk about the parameters that we will be adjusting for our control.
First, the PID term, as stated earlier, stands for Proportional, Integral, and Derivative. These parameters can be used individually or collectively.
Meaning, you can have just a proportional controller, a proportional and integral, a proportional and derivative, or of course a proportional, integral, and derivative controller.
To sum it all up, we, as control engineers, need to control processes and in order to do that, we use devices available to us in order to facilitate that function.
The stand-alone and integrated PID controller is the most widely used device for that purpose.
=============================
Missed our most recent videos? Watch them here:
=============================
To stay up to date with our last videos and more lessons, make sure to subscribe to this YouTube channel:
=============================
=============================
#RealPars #PID #PIDTuning
Комментарии