filmov
tv
CNC Mill for under $100
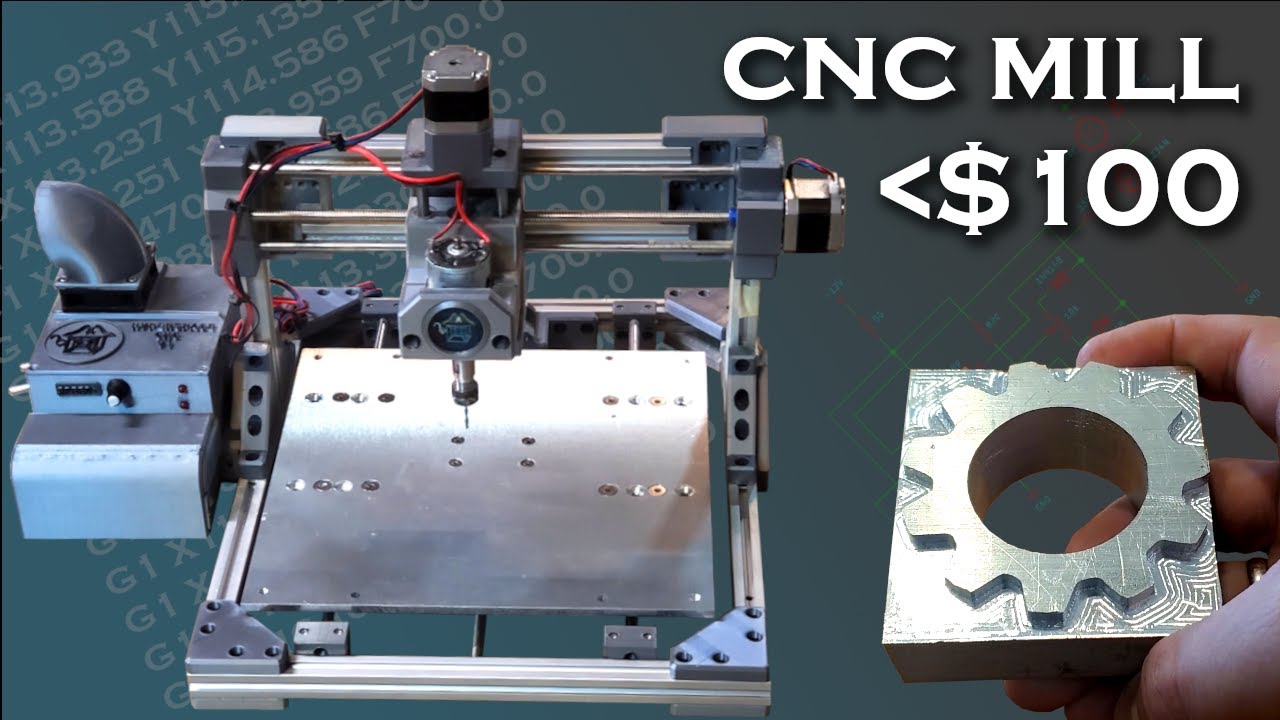
Показать описание
In this video I'm going to show how I built a basic CNC mill. Most of the hardware was sourced from spare / leftover parts I had laying around from other projects and ended up costing me under $100. It has a working area of approximately 250mm x 250mm x 70mm and is capable of milling aluminum (though somewhat rough).
The axes are moved with small NEMA17 stepper motors running at 24V, driven by A4988 drivers. The brain of the machine is an Arduino Uno running GRBL firmware, and G-code is sent to it via. USB from a laptop running Universal Gcode Sender - so everything is open source.
I have a little bit of experience operating a CNC mill, but this is the first one i've built / owned. The biggest learning experience from this build was that everything needs to be tightened up and made as rigid as possible to get good results. Between leadscrew backlash and rails flexing, the spindle could easily be moved +/- 1mm or more, which causes tons of vibration, chattering, rough cutting, and loss of precision. In a future video I'll be upgrading the spindle and beefing up the structure to use 16mm rails instead of 8mm for better rigidity.
I don't recommend trying to build this design yourself, because I created the printed brackets based on parts i had on hand, not what was "optimal". However, if you really want to, the STL's can be found here:
Music Used:
Kevin MacLeod - George Street Shuffle
Serge Pavkin - Atmospheric Ambient
Kevin MacLeod - Groove Groove
Eric Skiff - Underclocked
Serge Pavkin - Fractal
The axes are moved with small NEMA17 stepper motors running at 24V, driven by A4988 drivers. The brain of the machine is an Arduino Uno running GRBL firmware, and G-code is sent to it via. USB from a laptop running Universal Gcode Sender - so everything is open source.
I have a little bit of experience operating a CNC mill, but this is the first one i've built / owned. The biggest learning experience from this build was that everything needs to be tightened up and made as rigid as possible to get good results. Between leadscrew backlash and rails flexing, the spindle could easily be moved +/- 1mm or more, which causes tons of vibration, chattering, rough cutting, and loss of precision. In a future video I'll be upgrading the spindle and beefing up the structure to use 16mm rails instead of 8mm for better rigidity.
I don't recommend trying to build this design yourself, because I created the printed brackets based on parts i had on hand, not what was "optimal". However, if you really want to, the STL's can be found here:
Music Used:
Kevin MacLeod - George Street Shuffle
Serge Pavkin - Atmospheric Ambient
Kevin MacLeod - Groove Groove
Eric Skiff - Underclocked
Serge Pavkin - Fractal
Комментарии