filmov
tv
What Can You Do With a $200 CNC
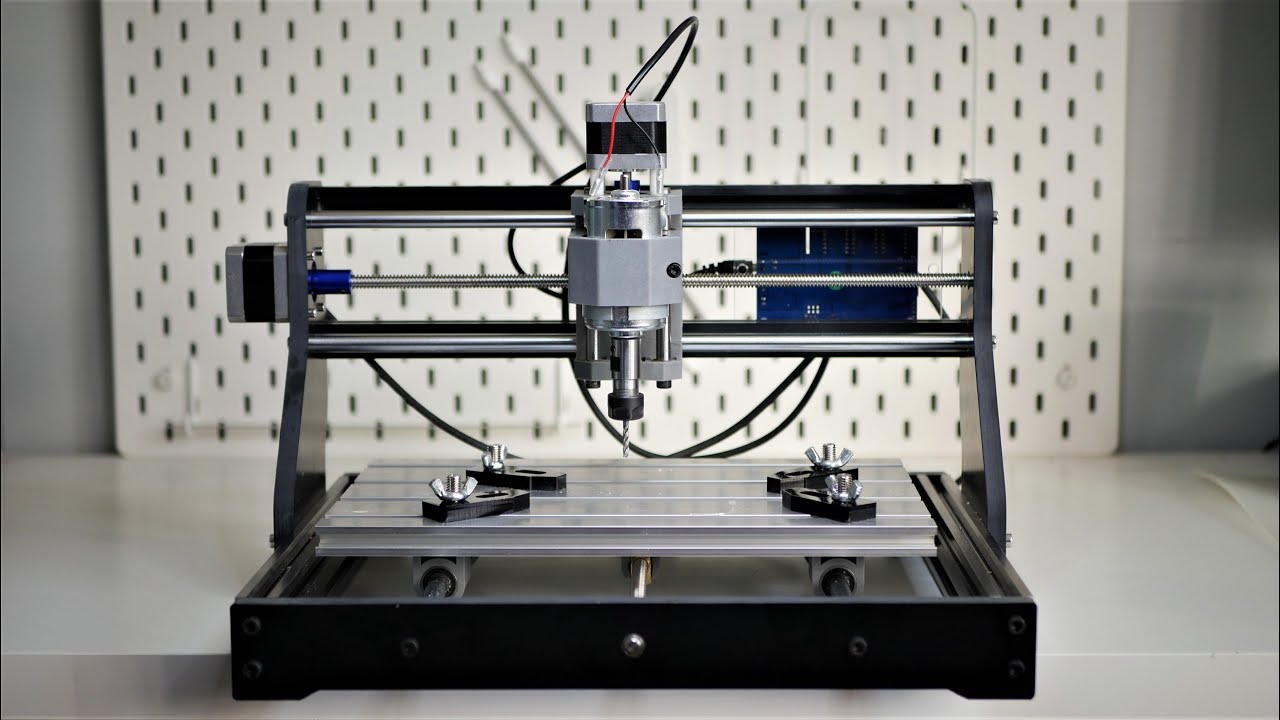
Показать описание
3018 CNC is probably the most inexpensive machine you can buy. Surprisingly with proper settings and materials, you can achieve really nice results! Sure, it's not the fastest CNC machine but definitely a great inexpensive learning tool for beginners.
Feedrate and depth of cut per pass:
Wood engraving: 500mm/min, 1mm
Wooden tray: 500mm/min, 1mm
Plywood: 400mm/min, 1mm
Acrylic engraving: 600mm/min, 1mm
Acrylic contour: 1000mm/min, 0.5mm
PCB: 300mm/min, 0.12mm and 0.6 for the contour
What Can You Do Song
Weird things you can do with your body #lifehacks #shorts
What can you do? (US version)
Steven Universe | What Can I Do For You? | Cartoon Network
What can you do? - Simple Skits
Steven Universe Official Soundtrack | What Can I Do (For You) | Cartoon Network
What Can You Do Without a Brain?
Lesson 5: What Can You Do?
The IMPOSSIBLE Push Up Challenge! 😱😬(Can You Do It?) #fitnesschallenge #fitness #gym
'What Can You Do With A Paleta?' Read Aloud by Ms. Torres
What Can You Do with Python? - The 3 Main Applications
What can you do with geography?
10 Things You Can Do With SLIME - Merrell Twins
What Can You Do With Blender 3D
I can Song | Things I can do
What YOU can do with 1 ROBUX...
Jack Savoretti - What More Can I Do? (Official Video)
What Can You Do That No One Else Can? Learn How To Answer This Interview Question
Rose and Greg Sing Together - “What Can I Do' | Steven Universe | Cartoon Network
What can you do with a neuroscience degree?
Copycat (Can You Do This?) | Kids Songs & Nursery Rhymes | The Mik Maks
What Can You Do Song -- 'I Can' Song
20 FUN Activities Kids Can Do With Slime l Improving Development and Play Skills l Sensory Autism
What Can I Do
Комментарии