filmov
tv
How To CNC Cut Metal For Under $400 using the 1310 CNC Router
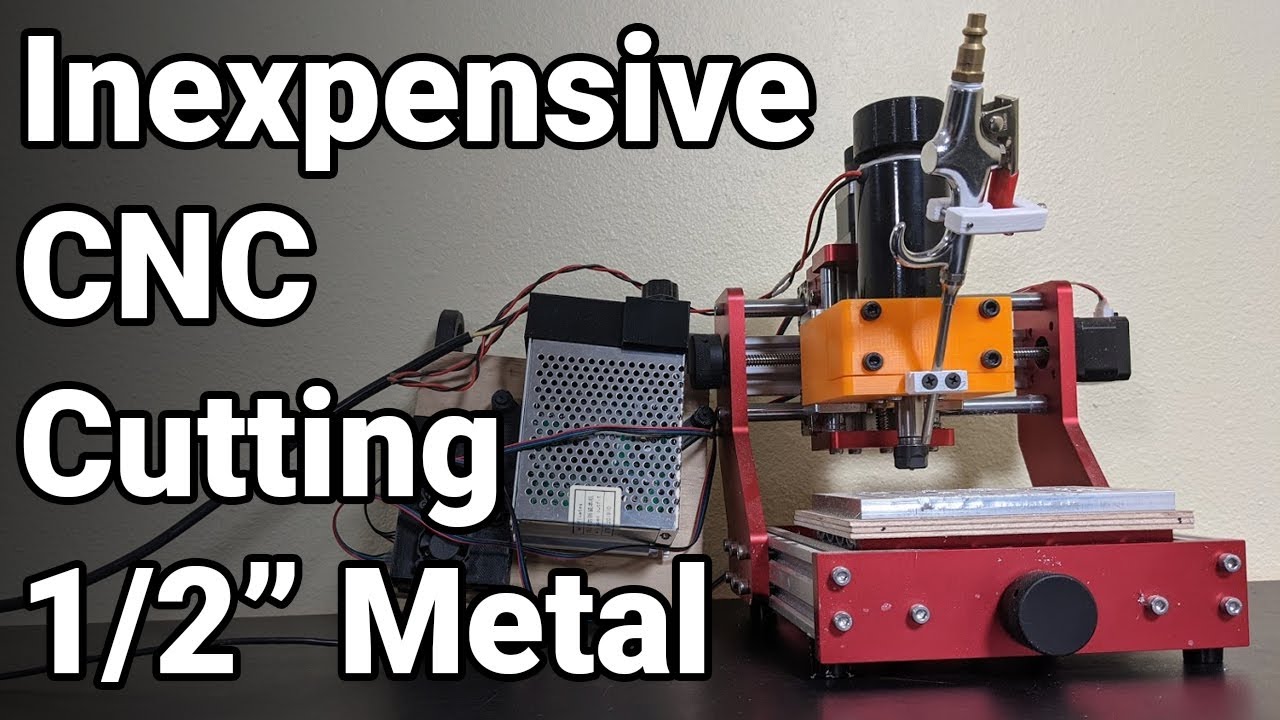
Показать описание
The dream is to be able to CNC cut metal parts in your garage for the least money possible. Well, I think I've got a solution for y'all: The 1310 CNC. It'a all metal construciton thick linear motion rods and Lead Screws on all 3 axis makes this the most robust inexpensive CNC machine coming out of China for under $300, but it's got an achilles heel: The spindle motor. So let's replace that and cut some 1/2" Aluminum.
Timestamps:
0:00 Intro
3:41 - Assembly Timelapse
4:48 - Stock Built Walkthrough & Critique
11:31 - Electronics
12:50 - Universal G-code Sender (UGS)
15:41 - CNC Coordinates Explained
19:07 - Firmware Modification
20:09 - Software workflow
29:07 - First Cuts in Metal
31:03 - New Motor
32:35 - 3D Printed Upgrade
34:20 - Getting the RPM correct by ear
35:32 - Adjusting Stepper Motor Torque
38:00 - New Motor Fan
39:13 - First Successful Aluminum Metal Parts Cut
43:15 - The Chatter is Breaking Bits
44:47 - Issues with Bits and Bit Selection
48:48 - Air cooling the cut
49:39 - Relocating the electronics
50:34 - Conclusion/Lessons Learned
Timestamps:
0:00 Intro
3:41 - Assembly Timelapse
4:48 - Stock Built Walkthrough & Critique
11:31 - Electronics
12:50 - Universal G-code Sender (UGS)
15:41 - CNC Coordinates Explained
19:07 - Firmware Modification
20:09 - Software workflow
29:07 - First Cuts in Metal
31:03 - New Motor
32:35 - 3D Printed Upgrade
34:20 - Getting the RPM correct by ear
35:32 - Adjusting Stepper Motor Torque
38:00 - New Motor Fan
39:13 - First Successful Aluminum Metal Parts Cut
43:15 - The Chatter is Breaking Bits
44:47 - Issues with Bits and Bit Selection
48:48 - Air cooling the cut
49:39 - Relocating the electronics
50:34 - Conclusion/Lessons Learned
Комментарии