filmov
tv
Cutoff Operations CAN be EASY
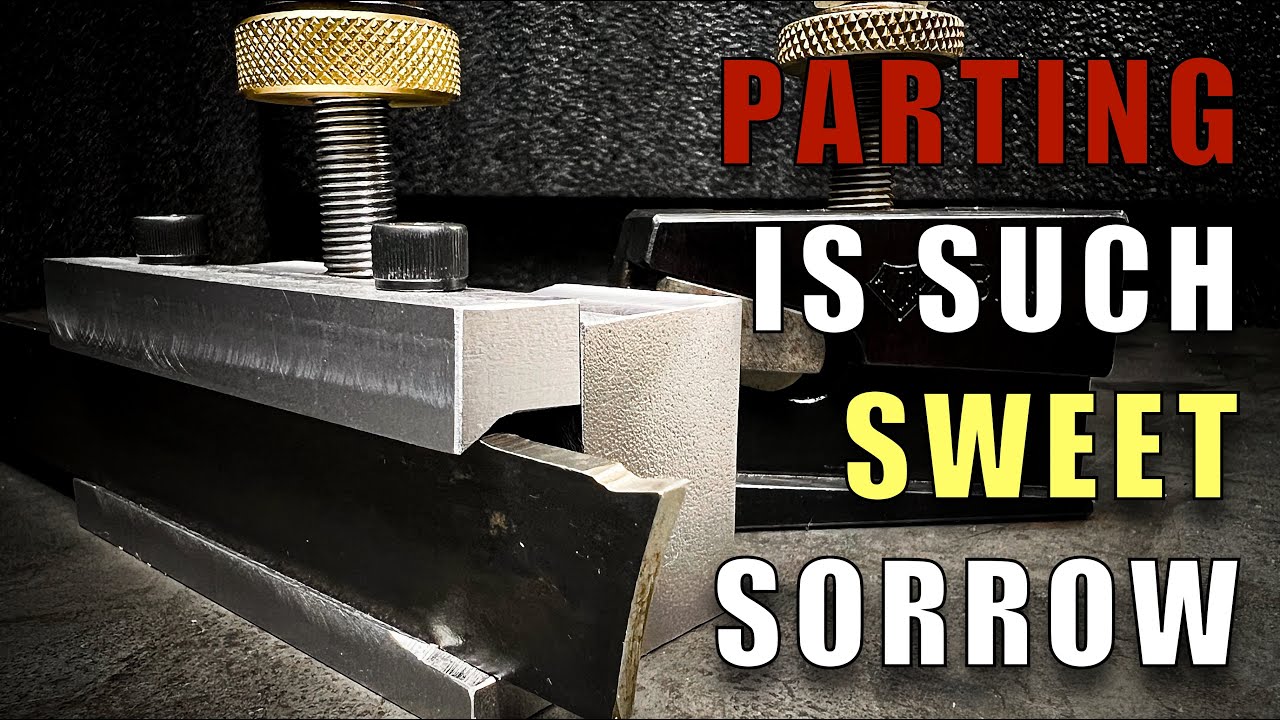
Показать описание
For this week's project we will be finishing up the DIY shop made parting tool holder for the aloris style BXA quick change tool post.
This is a more robust, versatile, and rigid cutoff tool holder that is meant to be an improved replacement for the typical parting tool holder that comes with most aloris style tool posts.
All of the work will be done on the milling machine and will include milling, drilling, and using the dovetail cutter.
I will also briefly demonstrate the use of sub datums on the DRO as a means to keep track of multiple different features, allowing you to revisit those features as many times as you need to perform a series of separate operations on the same feature.
As always, thank you for watching and if you have any questions, criticisms, ideas, etc. please leave a comment below!
My Lathe: MSC / Prince 9517350 - 13x40 Manual Metal Lathe
My Milling Machine: Bridgeport Variable Speed Series 1 "J Head"
My other Milling Machine: Brown & Sharpe No. 2 Plain "light type" Universal Milling Machine
CREDITS:
Cutoff Operations CAN be EASY
Active, saturation, & cutoff state of NPN transistor | Class 12 (India) | Physics | Khan Academy
Gotye - Somebody That I Used To Know (feat. Kimbra) [Official Music Video]
Verify: How easy is it to escape an ankle monitor?
The Simple Solution to Traffic
Basic Knife Skills
How does a spectrophotometer work?
How To Use An Angle Grinder - Ace Hardware
How To Remove a Stuck Nut or Bolt
The One Knife Needed To Butcher Meat Like A Pro | Game Changers
PhD-level AI shows we're forcing it to kill us all. OpenAI o1
How a Diesel Engine Works
Rain Bird Residential Valve Troubleshooting: Using the Bleed Screw to Fix a Sprinkler Leak
How To Fix a Lawn Mower That Quits, Dies or Stalls After 2 Minutes
Manually Turning a Valve On and Off - Rain Bird Residential Valve Troubleshooting
Is There a Way to Get Rid of Hemorrhoids for Good?
Order of operation - making a project easier by looking at how its made.
Line Handling Accident Prevention
Children First Aid: Nosebleed | First Aid | British Red Cross
Replacing the Solenoid: Rain Bird Residential Valve Troubleshooting
How To: SmartKey Features
How To Cut Down A Tree
How To Override The Push Button Start
[LG Dryers] How To Reset An LG Dryer
Комментарии