filmov
tv
Butt Connectors vs Solder | Crimping vs Soldering | Wire Connections | AnthonyJ350
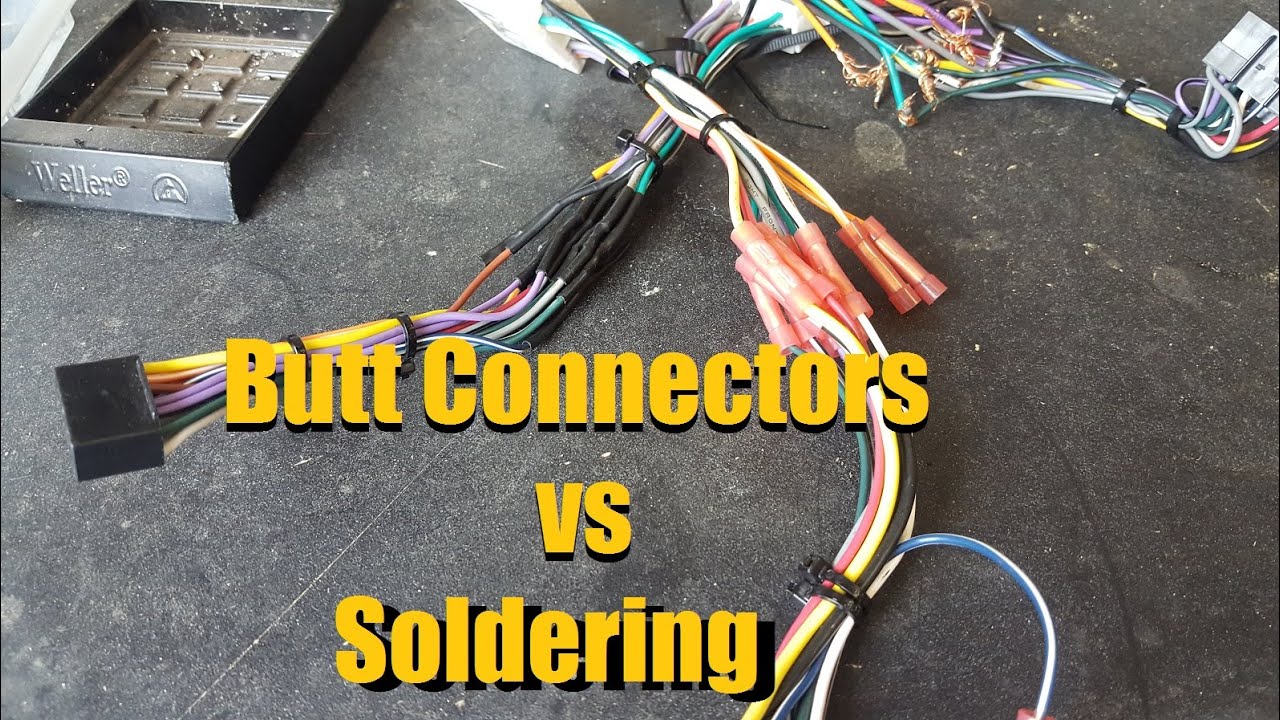
Показать описание
In this video I compare and contrast two styles of connections that are most commonly found in an install bay environment. Crimping with butt connectors and soldering.
If done properly, both are very solid connections. However I think soldering is still better because it's less prone to failure and corrosion.
About AnthonyJ350
I am a Mobile Electronics Certified Professional 12 Volt Installer (MECP Certified), Business Management Graduate (KPU), with a Professional Driver's License and a genuine automotive enthusiast who loves working on vehicles and I want to share my experiences with you. The goal is to help other people who can hopefully learn from my unique outlook towards vehicles, experiences and working practices.
Please feel free to ask questions or give feedback either in the comments or e-mail me.
New videos every week.
Go Fast Have Fun provides the content in this video, for information and entertainment purposes only.
The information in this Video presents guidelines to help vehicle enthusiasts modify or repair their vehicles and to demonstrate what car culture is all about. Go Fast Have Fun make no representations or warranties of any kind, express or implied, about the completeness, accuracy, reliability, suitability or availability with respect to the Video or the information, products, services, or related graphics contained on the Video for any purpose. Any reliance you place on such information is therefore strictly at your own risk. Nothing presented should be relied upon you for your modification or repair plans for your vehicle and is not in any way professional mechanical advice.
Go Fast Have Fun strongly recommends you consult with a professional automobile mechanic to ensure that any modification or repair plans for your vehicle are appropriate for your vehicle.
In no event will we be liable for any loss or damage including without limitation, indirect or consequential loss or damage, or any loss or damage whatsoever arising from loss of data or profits arising out of, or in connection with, the use of this Video and the information presented within it.
Go Fast have Fun
Canada
Butt Connectors vs Solder | Crimping vs Soldering | Wire Connections | AnthonyJ350
ANTHONYJ350
If done properly, both are very solid connections. However I think soldering is still better because it's less prone to failure and corrosion.
About AnthonyJ350
I am a Mobile Electronics Certified Professional 12 Volt Installer (MECP Certified), Business Management Graduate (KPU), with a Professional Driver's License and a genuine automotive enthusiast who loves working on vehicles and I want to share my experiences with you. The goal is to help other people who can hopefully learn from my unique outlook towards vehicles, experiences and working practices.
Please feel free to ask questions or give feedback either in the comments or e-mail me.
New videos every week.
Go Fast Have Fun provides the content in this video, for information and entertainment purposes only.
The information in this Video presents guidelines to help vehicle enthusiasts modify or repair their vehicles and to demonstrate what car culture is all about. Go Fast Have Fun make no representations or warranties of any kind, express or implied, about the completeness, accuracy, reliability, suitability or availability with respect to the Video or the information, products, services, or related graphics contained on the Video for any purpose. Any reliance you place on such information is therefore strictly at your own risk. Nothing presented should be relied upon you for your modification or repair plans for your vehicle and is not in any way professional mechanical advice.
Go Fast Have Fun strongly recommends you consult with a professional automobile mechanic to ensure that any modification or repair plans for your vehicle are appropriate for your vehicle.
In no event will we be liable for any loss or damage including without limitation, indirect or consequential loss or damage, or any loss or damage whatsoever arising from loss of data or profits arising out of, or in connection with, the use of this Video and the information presented within it.
Go Fast have Fun
Canada
Butt Connectors vs Solder | Crimping vs Soldering | Wire Connections | AnthonyJ350
ANTHONYJ350
Комментарии