filmov
tv
Knife made from COPPER WIRE - Its SHARP!! - Aluminum bronze with forged edge
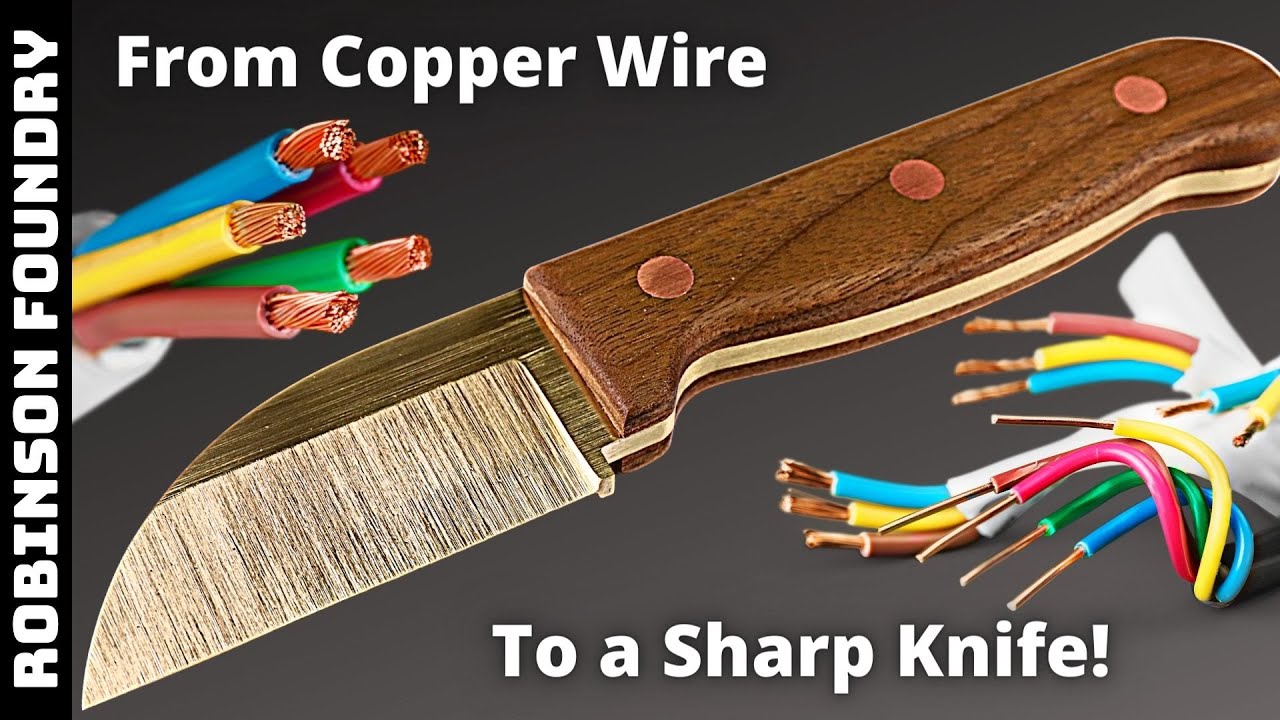
Показать описание
In this video I'll be making an aluminum bronze knife to use around my shop. I made this knife from copper wire and pure aluminum. 90% copper mixed with 10% aluminum makes a very hard alloy called aluminum bronze. I made the knife by creating a sand casting and then cutting the shape of the knife out of it. I then cast pure copper pins and used them to attach walnut handle scales.
Casting equipment
3d printing FDM
3d printing Resin
Belt Grinder
Belt Grinder Accessories
Welding
Metal finishing tools
General
Some of my favorite tools of the year
Camera Equipment
All of the links above are affiliate links. This means that, at zero cost to you, I will earn an affiliate commission if you click through the link and finalize a purchase.
Casting equipment
3d printing FDM
3d printing Resin
Belt Grinder
Belt Grinder Accessories
Welding
Metal finishing tools
General
Some of my favorite tools of the year
Camera Equipment
All of the links above are affiliate links. This means that, at zero cost to you, I will earn an affiliate commission if you click through the link and finalize a purchase.
I Make A Knife From Copper And Cable
Knife made from COPPER WIRE - Its SHARP!! - Aluminum bronze with forged edge
Damascus steel technology using copper piano strings.
This is truly the best wire stripper in 2023
Casting Copper Knife out of Scrap
FORGING A COPPER DAMASCUS KNIFE . Part 2
Forging a Copper Damascus Bowie Knife
Melting Copper Wire into Axe - Bronze Casting
An Incredibly Sharp And Strong Knife That I Made And An Ordinary Iron Cable
Making A Knife From Copper And Cable
Making a Cable and Copper Chef Knife
i made a copper knife #trending #shorts #casting #knife
Forging a Copper Damascus Katana
❗How to STRIP Copper WIRE | A Selection of 55 of The Best Wire Strippers.😲😲😲
This video will make your Life easier. Copper from thin Wires, quickly and easily in just 8 Minutes.
Forging a Solid Copper Damascus Cu Mai Knife
Casting Cimmerian Arrow out of Bronze
Making a Knife w/ COPPER Wire Sponge Epoxy Handle
Scrap copper to dagger knife
This is the best knife for stripping copper wires.
I regret not having learned this secret at age 50! I would die without knowing
Stripping Copper Wires without Knives and special Devices | Easy and Fast
This is all you need to strip any wires. Top 4 Homemade Knives.
DIY $1 Homemade Wire Stripper - Copper Cord, ROMEX, & Aluminum Cable Cheap Stripping Device Tool
Комментарии