filmov
tv
What is Rotary Broaching?
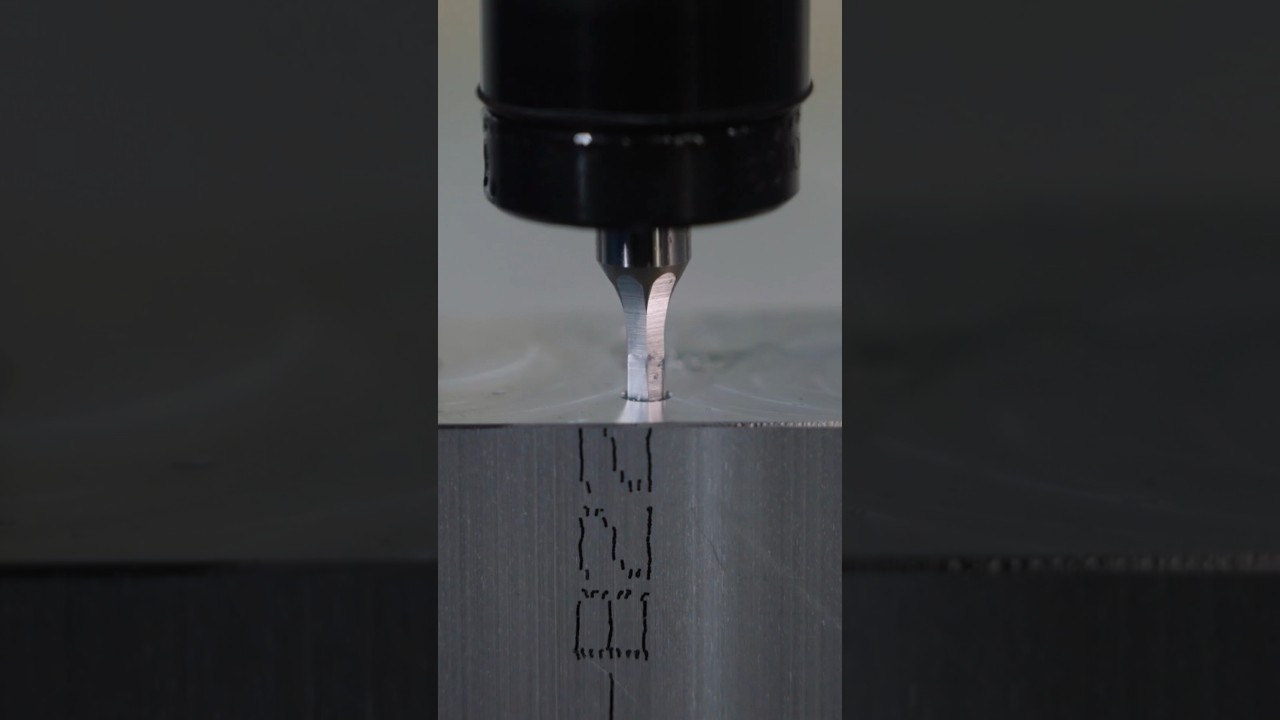
Показать описание
How does rotary broaching work?
What is Rotary Broaching?
Rotary Broaching Illustration in a Lathe - By Polygon Solutions
How Does Rotary Broaching Work? by Polygon Solutions
What is Rotary Broaching? | Slater Tools
Rotary Broaching #machining
Rotary Broaching The Night Away
Rotary Broaching Illustration in a Mill - By Polygon Solutions
Rotary Broach: Captain's Log, Supplemental
Rotary Broaching on a Lathe with Poliangolar Broaching System
Rotary Broaching
KC-CX Rotary Broaching Tool Holder On CNC Lathe
Broaching on Lathes and Mills: Rotary Broaching | Slater Tools
Rotary Broaching Innovation at IMTS 2014
Rotary broaching process also known as wobble broaching process
Detailed Rotary Broach #TMC2020
Making A Rotary Broach - Cutting Hex Sided Holes (DIY)
BROACHING: Innovative Way To Cut Complex Metal Shapes
Cutting Complex Metal Shapes with Broaching
Adonai Rotary Broach - BCM27 with hex insert - product
History of Rotary Broaching at IMTS 2014
rotary broaching with a boring head
Rotary Broaching a 36 Tooth Spline into a Custom Socket
Rotary Broaching a Hex Key Recess on a Mini Lathe
Комментарии