filmov
tv
Basic Guitar Soldering. Sharpen My Axe
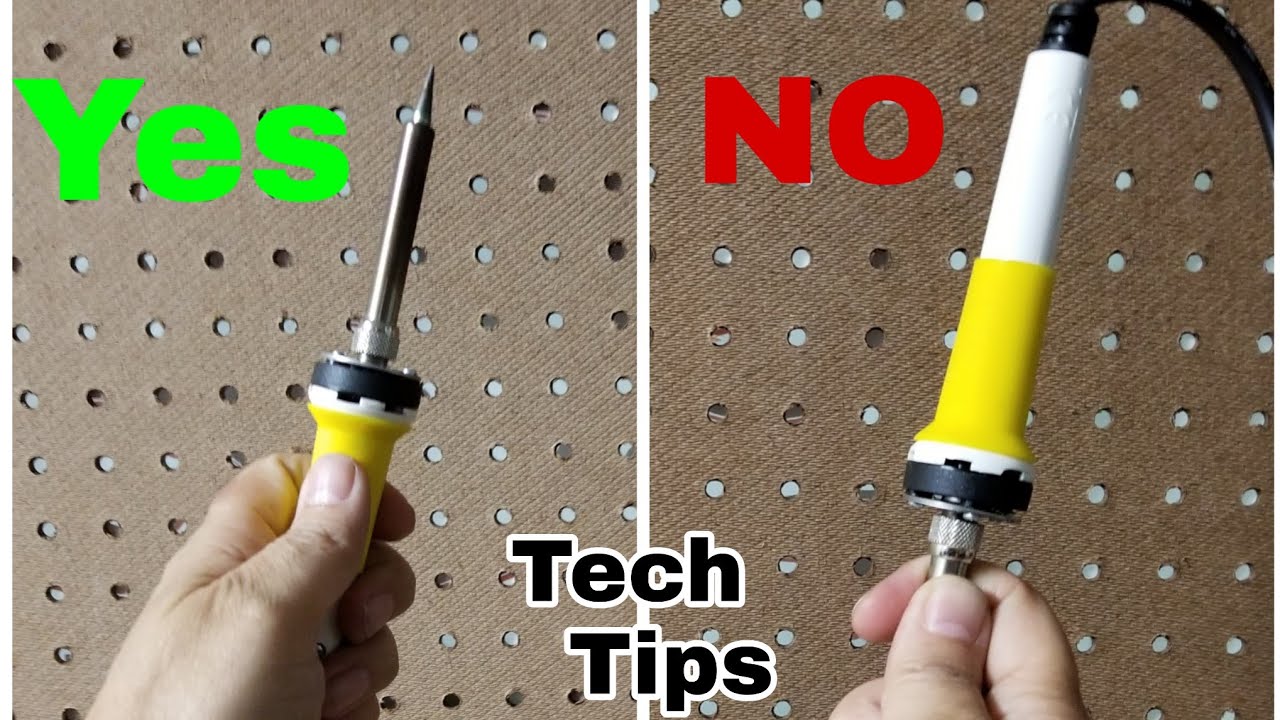
Показать описание
#knowyourgear #sharpenmyaxe #mcknightrepair
Support this channel by checking out our Know Your Gear merch
Soldering tools to check out
The Snark tuner I'm using in this video
Radius Gauge with slots
Fret Rocker
Precision Notched Straightedge
The Music Nomad gauge I use
Digital Caliper
Digital Multimeter
Clip On Tuner in this video
My Favorite set up tools
Helping Hands
Here are some other products from a dealer I trust and buy from online
You can become a Patreon and support more videos like this
Know Your Gear Facebook
Instagram
Want to have your product on an episode ? Contact me here
By clicking some of the links above you are supporting the channel with the purchases you make. Thank you
Support this channel by checking out our Know Your Gear merch
Soldering tools to check out
The Snark tuner I'm using in this video
Radius Gauge with slots
Fret Rocker
Precision Notched Straightedge
The Music Nomad gauge I use
Digital Caliper
Digital Multimeter
Clip On Tuner in this video
My Favorite set up tools
Helping Hands
Here are some other products from a dealer I trust and buy from online
You can become a Patreon and support more videos like this
Know Your Gear Facebook
Want to have your product on an episode ? Contact me here
By clicking some of the links above you are supporting the channel with the purchases you make. Thank you
Basic Guitar Soldering. Sharpen My Axe
How to Solder Guitar Electronics | Guitar Tech Tips | Ep. 20 | Thomann
How the guitar output jack works. Sharpen My Axe
Guitar wiring: how to get a good clean solder joint!
How to Solder Guitar Parts and Wiring - Tips, Tricks & Methods
How To Solder: Basic Electric Guitar Wiring 101 (by request)
How To Solder Parts in a Guitar Some Basic Tips
How To Solder Guitar Pots, Caps, And Wire
Installing Stainless Steel Frets In A $75 Guitar. Sharpen My Axe
Full Guitar Soldering Series on our Channel 👍
How To Solder Guitars (5/6) - Soldering to a Jack Socket
How To Solder Guitars (1/6) Soldering Technique and the RIGHT Equipment
Building A Super Strat Out Of A $75 Guitar. Sharpen My Axe
How To Solder Guitars (6/6) - Soldering to a Trem Claw
How to Solder a PureTone Output Jack #shorts
The Ultimate Squier Upgrade Experiment. Sharpen Your Axe
How to solder | Repair a guitar cable with basic tools
How To Solder Guitar Parts
How To Solder Guitars (3/6) - Soldering a Stratocaster Switch
The Solder Monster’s long arms reach into your guitar cavity
Fret Leveling - The Easy Way // How To
How To Solder Guitar Parts - Dylan Talks Tone #207
Mods anyone can do to their Fender Strat. Sharpen My Axe
How To Solder Guitars (2/6) - Capacitors and Pots
Комментарии