filmov
tv
Drill through anything (conductive) with Electrical Discharge Machining
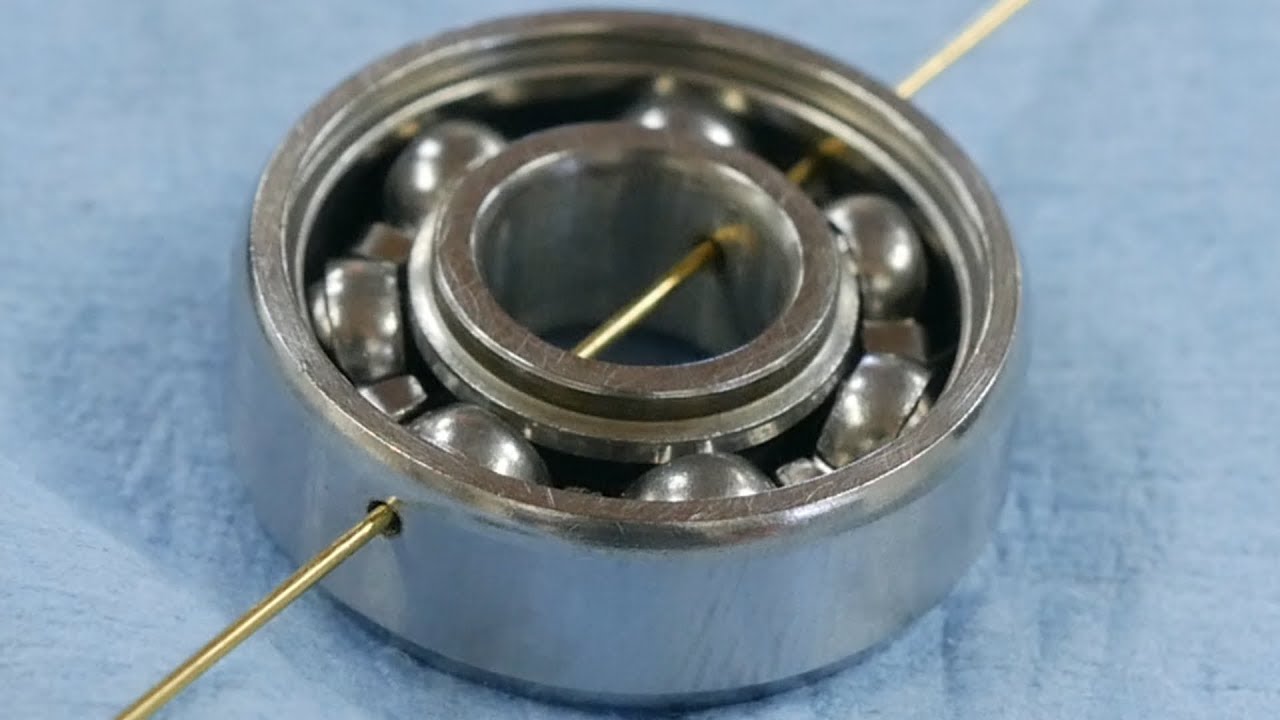
Показать описание
I show how to build an EDM drilling machine, describe how it works, and where to buy parts.
Drill through anything (conductive) with Electrical Discharge Machining
Incredible Drill Anything Conductive (EDM) Short
Incredible Drill Anything Conductive EDM
How to drill through the centre of a bolt | drill bolt guide
What's Inside the Worlds' Fastest Heat Conductor?
Horizontal Directional Drilling / Boring (HDD): How the Drill Bit is Steered
The super glue idea that not many people know about
Super Glue and Baking soda! Pour Glue on Baking soda and Amaze With Results
What REALLY HAPPENS WHEN YOU SPILL WATER in an OUTLET?
Cryogenic treatment of drill bits: tested 2X lifetime and microstructure analysis
10 STUPID ERRORS To AVOID in Soldering and TIPS
Electrician Quick Tip #4 - Fish Tape Trick
Amazing precision of a DIY Wire EDM machine
Repurposing Cordless Drills
No, we didn't use Magic to Crush this Can...
'Zero Tolerance Machining' with the Wire EDM, Making a Puzzle Cube - Part 2 | US Digital
Aluminum Welding Rods: What You NEED to Know
How We Made A Wire EDM Machine At Home
Open end round head copper riveting effect show can be conductive
Stainless steel conductive thread
How to Make • Surface Speaker
Open end round head copper spigot riveting effect show, can conductive spigot
Do you know the conductive blind rivets?#kseet #rivet #hardwaretools
Copper rivets riveting magnets, PCB panels, conductive rivets #szent #riveter #blindrivet#kseetrivet
Комментарии