filmov
tv
EEVblog 1443 - They Don't Teach This in School! (Coherence)
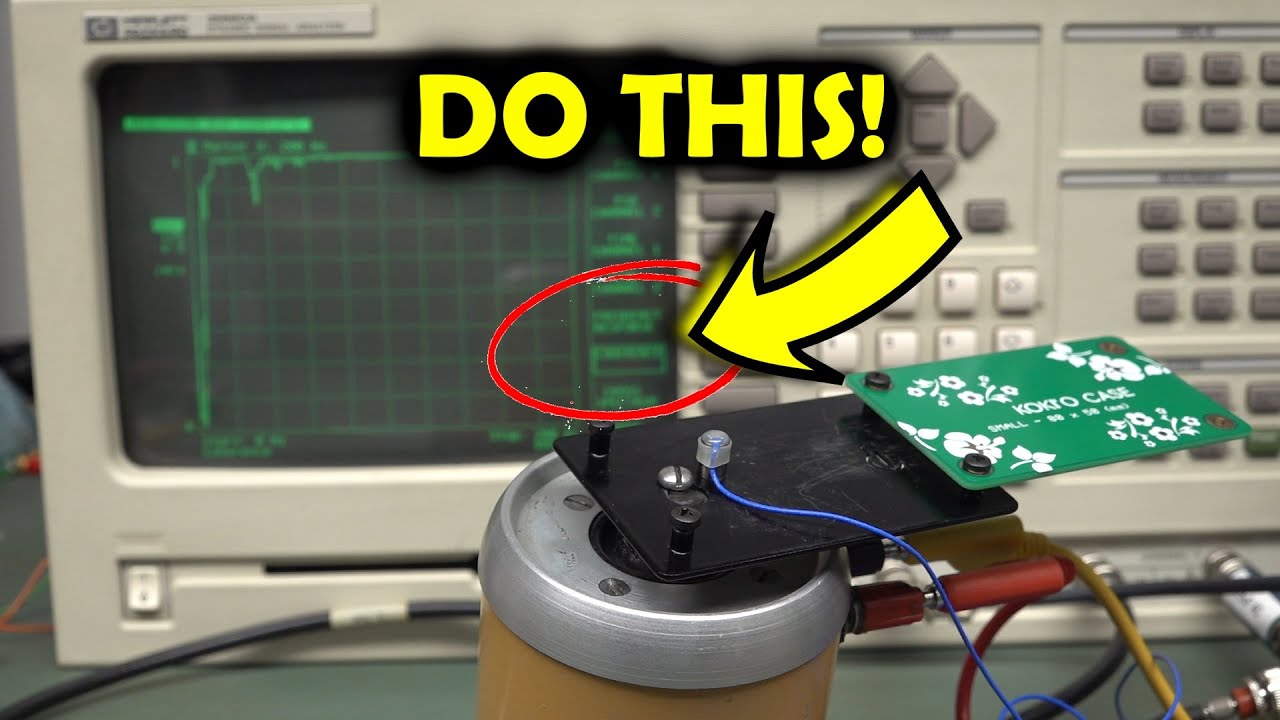
Показать описание
A follow-up video to the Electrodynamic Shaker, showing you the critical importance of Coherence measurement. Something you'll only get taught in the school of hard knocks!
Using the Ling Electrodynamic shaker, a measurement accelerometer, and a Dynamic Signal Analyser to set up a vibration test system.
00:00 - Electrodynamic Shaker
01:20 - The most inportant thing in vibration measurement
03:56 - What is a Dymanic Signal Analyser?
06:28 - It's all about the system response
08:12 - Your expensive calibrated setup is worthless!
08:44 - What is Coherence?
12:17 - If you've got a really crappy shaker
13:10 - Let's set up a vibration test jig
13:54 - How to power and accelerometer
16:44 - What happens if you leave it flapping around in the breeze?
20:14 - Traps for young players
22:39 - Let's sweep this sucker
26:50 - Tighten your nuts!
28:22 - Show me your coherence plot or GTFO!
Buy anything through that link and Dave gets a commission at no cost to you.
Donate With Bitcoin & Other Crypto Currencies!
#ElectronicsCreators #Vibration #Measurement
Using the Ling Electrodynamic shaker, a measurement accelerometer, and a Dynamic Signal Analyser to set up a vibration test system.
00:00 - Electrodynamic Shaker
01:20 - The most inportant thing in vibration measurement
03:56 - What is a Dymanic Signal Analyser?
06:28 - It's all about the system response
08:12 - Your expensive calibrated setup is worthless!
08:44 - What is Coherence?
12:17 - If you've got a really crappy shaker
13:10 - Let's set up a vibration test jig
13:54 - How to power and accelerometer
16:44 - What happens if you leave it flapping around in the breeze?
20:14 - Traps for young players
22:39 - Let's sweep this sucker
26:50 - Tighten your nuts!
28:22 - Show me your coherence plot or GTFO!
Buy anything through that link and Dave gets a commission at no cost to you.
Donate With Bitcoin & Other Crypto Currencies!
#ElectronicsCreators #Vibration #Measurement
Комментарии