filmov
tv
EEVblog 1442 - DON'T DO THIS! (PCB Vibration Testing)
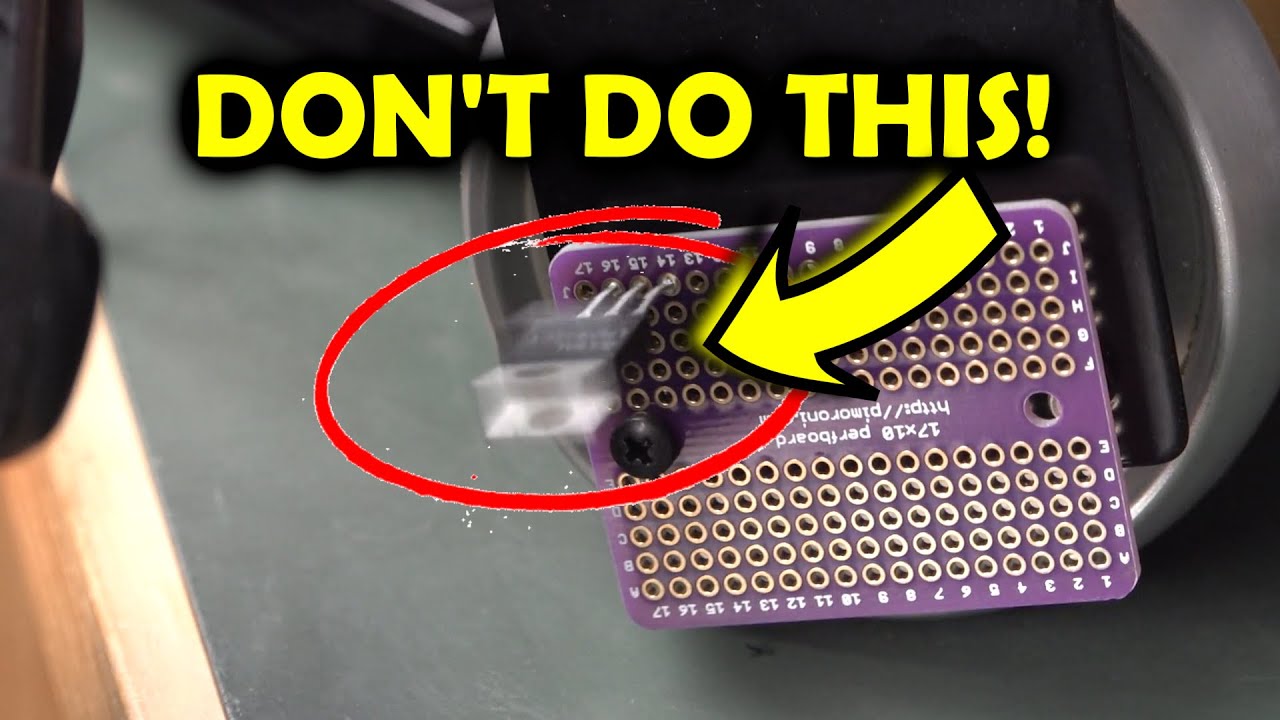
Показать описание
An innocent TO-220 regulator gets tortured using a mystery device from the bunker.
The art of environmental vibration PCB testing.
00:00 - What is this thing?
01:00 - I used to use these all the time
02:40 - Electrodynamic Shaker
03:56 - How PCB's are vibration tested
07:00 - Teardown
08:10 - Accelerometers
12:27 - The datasheet
12:57 - Does it work?
15:13 - Let's torture this poor TO-220
20:00 - Slow-mo looks cool!
20:45 - It's going to come-a-gutsa!
Buy anything through that link and Dave gets a commission at no cost to you.
Donate With Bitcoin & Other Crypto Currencies!
#ElectronicsCreators #Vibration #Testing
The art of environmental vibration PCB testing.
00:00 - What is this thing?
01:00 - I used to use these all the time
02:40 - Electrodynamic Shaker
03:56 - How PCB's are vibration tested
07:00 - Teardown
08:10 - Accelerometers
12:27 - The datasheet
12:57 - Does it work?
15:13 - Let's torture this poor TO-220
20:00 - Slow-mo looks cool!
20:45 - It's going to come-a-gutsa!
Buy anything through that link and Dave gets a commission at no cost to you.
Donate With Bitcoin & Other Crypto Currencies!
#ElectronicsCreators #Vibration #Testing
EEVblog 1442 - DON'T DO THIS! (PCB Vibration Testing)
EEVblog 1443 - They Don't Teach This in School! (Coherence)
EEVblog 1441 - Electric Buses are NOT a SCAM (Adam Something)
EEVblog 1439 - Analysing Veritasium's Electricity Misconceptions Video
EEVblog 1430 - Rent vs Buy - My $400,000 MISTAKE!
EEVblog 1465 - Your Multimeter Can Measure Inductors
Why Don't I Hire A Video Editor? (AGAIN)
eevBLAB 94 - Why Dont Companies DO THIS Anymore?
OLD VIDEO RELEASE: What's old is new again. The Lab. Rent vs Buy
EEVblog 1392 - No temp probe? No problem!
EEVblog 1447 - EXPENSIVE Fluke vs CHEAPER Brymen - Teardown
Always Have a Side Hustle
EEVblog 1481 - Dodgy Dangerous Heater REPAIR
eevBLAB 89 - Youtube is DEAD - Dislike Count REMOVED!
eevBLAB 91 - Why Are Fluke Meters So EXPENSIVE?
EEVblog 1446 - Analog Watt Hour Meters are AMAZING!
EEVblog 1479 - Is Your Calculator WRONG?
EEVblog #1325 - OPAMP Shootout - Datasheet Deep Dive
EEVblog 1486 - What you DIDN'T KNOW About Film Capacitor FAILURES!
EEVblog 1517 - Heat Pump Hot Water Install & Analysis
EEVblog 1448 - Convert a Fluke 77 IV to True RMS for 10 CENTS!*
Petition - Australian Standards Should be FREE
The EEVblog Lab VIBRATES!
Youtube LIED about Removing DISLIKES
Комментарии