filmov
tv
Understanding the Tesla Model S Power Electronic Components
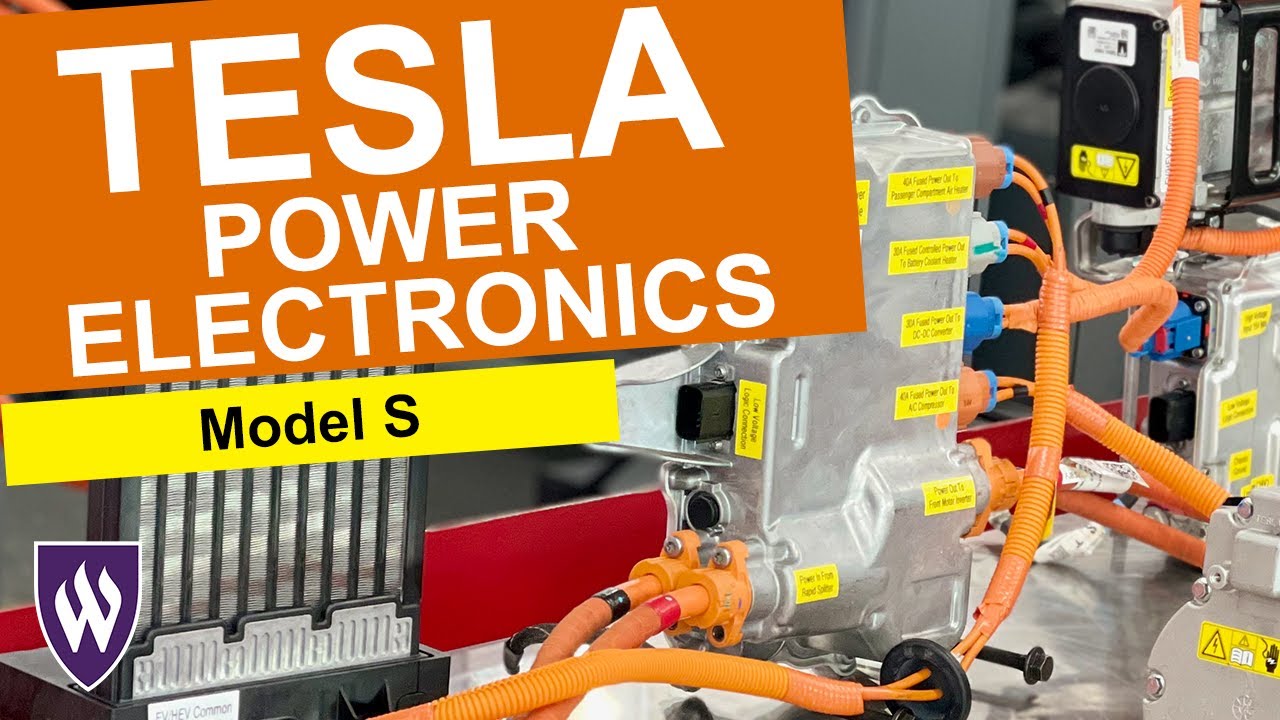
Показать описание
Join me on a journey through 74 feet (22.56 meters) of high voltage cable through 10 different power electronics components of a 2015 and later Tesla Model S AWD.
TIMELINE:
0:00 Start
0:10 Introduction
0:50 Model S cables and common components
1:16 MUST SEE Orange cable core and shielding
2:38 Common component 1 - The Charge Receptacle
4:00 The charging receptacle cable size (50 sq mm) compared to the Tesla Model 3 cable size (95 sq mm)
6:12 Common component 2 - The On-Board Charger Module (48A 11.52 kW)
7:48 Single Phase or three-phase power input ports
10:10 The Interlock circuit
11:50 See the internal parts and connections of the on-board charger
12:28 MUST SEE The AC power input path through the on-board charger
12:55 AC voltage needs to be boosted to ~400V
13:39 The DC power output path through the on-board charger
14:10 The DC power input path through the on-board charger
14:32 The DC contactors used when supercharging the battery
15:47 A Safety Warning that should have been at the start of the video
16:54 The DC output from the on-board charger
17:26 Common component 3 - The Rapid Splitter (Front Junction Box)
17:50 The connection to the high voltage battery through the rapid splitter
18:22 The function and internal connections of the Rapid splitter
22:20 The position of the Rapid Splitter in the vehicle under the rear seat
22:50 Common component 4 - The rear motor inverter
24:54 Summary of the high voltage components in the rear of the vehicle
25:48 MUST SEE Pyrofuse Pack battery cable tag and pyrotechnic fuse
26:22 The standard 1300 amp fuse
26:40 The 2000 amp pyrotechnic fuse and its internal components
30:30 Why the battery fuse is needed
31:45 The high voltage components and cables at the rear of the vehicle
32:28 Common component 5 - The High Power Distribution Module (HPDM) (Front junction block)
33:20 See the four internal fuses and circuit board inside the HPDM
34:22 Another Interlock switch
34:48 The battery coolant heater control circuit
35:48 The high voltage connections from the Rapid Splitter to the HPDM
36:49 Common component 6 - The front motor inverter
38:17 The NVH Mat covering the front Drive Unit and motor
39:55 Common component 7 - The electric air-conditioning compressor (40A Fuse)
41:23 Common component 8 - The 2500 Watt DC to DC converter (30 A Fuse)
42:05 DC to DC converter output of 178 amps at 14 volts
43:03 the DC to DC converter charges the 12V battery
44:16 Common component 9 - The high voltage battery coolant heater (30 A Fuse controlled)
46:18 Common component 10 - The Positive Temperature Coefficient (PTC) Cabin Air Heater (40A Fuse)
48:18 The high voltage components and cables at the front of the vehicle
49:29 Almost all Electric Vehicles (EV) have the same common components shown in this video
50:39 Additional EV training is available for you.
51:12 Wrap up and summary
ABOUT US
ADDITIONAL TRAINING FOR YOU
DONATE TO OUR DEPARTMENT
TIMELINE:
0:00 Start
0:10 Introduction
0:50 Model S cables and common components
1:16 MUST SEE Orange cable core and shielding
2:38 Common component 1 - The Charge Receptacle
4:00 The charging receptacle cable size (50 sq mm) compared to the Tesla Model 3 cable size (95 sq mm)
6:12 Common component 2 - The On-Board Charger Module (48A 11.52 kW)
7:48 Single Phase or three-phase power input ports
10:10 The Interlock circuit
11:50 See the internal parts and connections of the on-board charger
12:28 MUST SEE The AC power input path through the on-board charger
12:55 AC voltage needs to be boosted to ~400V
13:39 The DC power output path through the on-board charger
14:10 The DC power input path through the on-board charger
14:32 The DC contactors used when supercharging the battery
15:47 A Safety Warning that should have been at the start of the video
16:54 The DC output from the on-board charger
17:26 Common component 3 - The Rapid Splitter (Front Junction Box)
17:50 The connection to the high voltage battery through the rapid splitter
18:22 The function and internal connections of the Rapid splitter
22:20 The position of the Rapid Splitter in the vehicle under the rear seat
22:50 Common component 4 - The rear motor inverter
24:54 Summary of the high voltage components in the rear of the vehicle
25:48 MUST SEE Pyrofuse Pack battery cable tag and pyrotechnic fuse
26:22 The standard 1300 amp fuse
26:40 The 2000 amp pyrotechnic fuse and its internal components
30:30 Why the battery fuse is needed
31:45 The high voltage components and cables at the rear of the vehicle
32:28 Common component 5 - The High Power Distribution Module (HPDM) (Front junction block)
33:20 See the four internal fuses and circuit board inside the HPDM
34:22 Another Interlock switch
34:48 The battery coolant heater control circuit
35:48 The high voltage connections from the Rapid Splitter to the HPDM
36:49 Common component 6 - The front motor inverter
38:17 The NVH Mat covering the front Drive Unit and motor
39:55 Common component 7 - The electric air-conditioning compressor (40A Fuse)
41:23 Common component 8 - The 2500 Watt DC to DC converter (30 A Fuse)
42:05 DC to DC converter output of 178 amps at 14 volts
43:03 the DC to DC converter charges the 12V battery
44:16 Common component 9 - The high voltage battery coolant heater (30 A Fuse controlled)
46:18 Common component 10 - The Positive Temperature Coefficient (PTC) Cabin Air Heater (40A Fuse)
48:18 The high voltage components and cables at the front of the vehicle
49:29 Almost all Electric Vehicles (EV) have the same common components shown in this video
50:39 Additional EV training is available for you.
51:12 Wrap up and summary
ABOUT US
ADDITIONAL TRAINING FOR YOU
DONATE TO OUR DEPARTMENT
Комментарии