filmov
tv
Understanding the Tesla Model S Front Motor
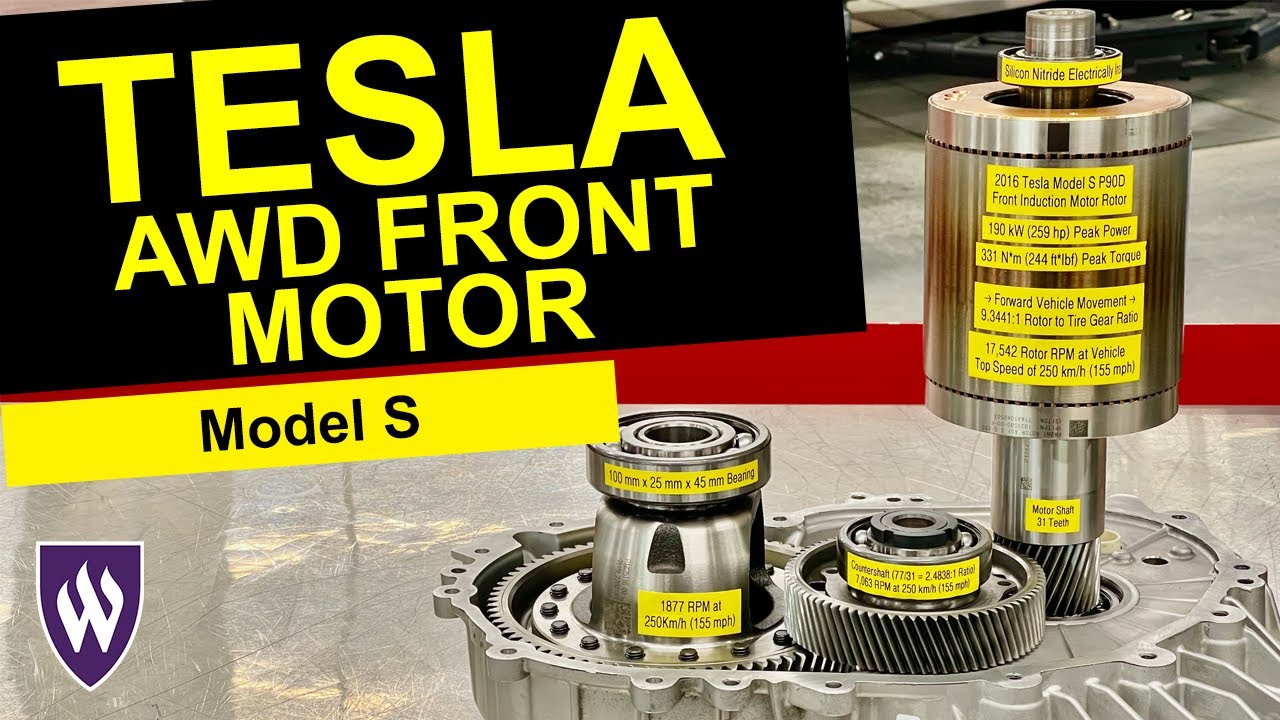
Показать описание
Join me for another deep dive to see the details of the 17,500 RPM front motor and drive unit from a 2014-2018 Tesla Model S AWD. See all four motor rotors from the Tesla Model S and Model 3. The video is divided into four sections showing: 1. The motor and gears. 2. The high-performance bearings. 3. The lubrication system. and 4. The electrical system.
TIMELINE:
0:00 Start
0:11 Model S, X, and 3 electric motor combinations
1:30 RWD Model S and X motors
1:37 AWD Model S and X motors
1:54 Performance AWD Model S and X motors
2:28 RWD and AWD Model 3 motors
3:10 MUST SEE Close up photos of all four motors
3:44 Video Section 1 - Gears and Rotor
3:56 Gear housing components
4:49 Comparison of differential with a rear performance motor
5:53 MUST SEE Why are the bearings and gears so big?
7:36 The front differential case speed at 250 km/h (155 mph) = 1877 RPM
7:54 MUST SEE Different tire sizes and different gear ratios
9:00 Installation of the front differential case with a 79 tooth ring gear (Prime Number)
9:22 The Counter Shaft with 21 (Factors 3, 7) pinion gear teeth. 79/21 = 3.7619:1 Gear ratio from countershaft to the differential case
10:41 The countershaft speed at 250 km/h (155 mph) = 7063 RPM
11:08 The motor rotor shaft and drive gear with 31 teeth (Prime Number)
11:35 MUST SEE Comparison of the front rotor to the rear performance rotor
12:56 Maximum torque at a vehicle speed comparison
15:36 Motor rotor speed sensor and reluctor wheel
16:49 MUST SEE SKF Ceramic Bearing (Silicon Nitride) on the rotor
17:43 The rotor is in a wet environment and cooled by the transmission fluid
18:33 MUST SEE Rotor shaft grounding rings with conductive filaments from (AEGIS?)
19:37 Shaft grounding protects bearings from damage from electrical current
20:10 The Rotor Shaft with 31 gear teeth drives the 77 (Factors 7, 11) tooth counter gear. 77/31 = 2.4839:1 Gear ratio.
20:52 See all three gears in the reduction gearbox with an overall gear reduction of (79/21) x (77/31) = 9.3441:1
21:26 The differential and the axle half shaft and jackshaft to reduce torque steer
22:23 Video Section 2 - Specialized Bearings
22:58 How Tesla run bearings at higher speeds than their limiting speeds with lubrication
23:07 Video Section 3 - Specialized Lubrication for bearings
23:34 The 20 tooth oil pump gear is overdriven by the differential ring gear 20/79 = 0.2531:1 gear ratio (3.95 times faster than the ring gear)
24:18 The transmission fluid drain and fill plugs
24:39 The fluid refill procedure
25:45 MUST SEE The proper fluids for the front-drive unit (Mobile SHC 629 and Dexron VI)
28:00 The path of the pressurized transmission fluid to six destinations
28:09 1. Lubrication and cooling to the motor gear and conductive bearing
29:08 2. Through the fluid-to-coolant heat exchanger to remove or add heat
31:04 3. Cool fluid is sprayed on the stator frame and right side windings for cooling through a sparge pipe
32:24 4. Cool fluid is sprayed on the non-conductive bearing and the right side of the rotor
32:58 5. Cool fluid is dripped on the stator frame and left side windings
32:47 6. Cool fluid is sprayed on the left side of the rotor
33:48 Transmission fluid fill capacities
34:42 Video Section 4 - Electrical Components
34:50 MUST SEE The three-phase, four-pole, 48 slot stator
35:55 The milli-ohm resistance of the stator windings with a Hioki RM3548 Resistance Meter
36:48 High-Performance induction motors versus high-efficiency Internal Permanent Magnet Synchronous Reluctance Motors (IPM-SynRM)
39:30 The inverter and its connection to the stator
41:42 The stator temperature sensor
42:40 How the stator frame is mounted with the stator housing
45:18 Thank you for your donations
ABOUT US
Weber State University (WSU) Davis Campus - Automotive Technology Department - Advanced Vehicles Lab. A technical description and operational demonstration of the Tesla Model S Front Drive Unit (FDU).
ADDITIONAL TRAINING FOR YOU
DONATE TO OUR DEPARTMENT
TIMELINE:
0:00 Start
0:11 Model S, X, and 3 electric motor combinations
1:30 RWD Model S and X motors
1:37 AWD Model S and X motors
1:54 Performance AWD Model S and X motors
2:28 RWD and AWD Model 3 motors
3:10 MUST SEE Close up photos of all four motors
3:44 Video Section 1 - Gears and Rotor
3:56 Gear housing components
4:49 Comparison of differential with a rear performance motor
5:53 MUST SEE Why are the bearings and gears so big?
7:36 The front differential case speed at 250 km/h (155 mph) = 1877 RPM
7:54 MUST SEE Different tire sizes and different gear ratios
9:00 Installation of the front differential case with a 79 tooth ring gear (Prime Number)
9:22 The Counter Shaft with 21 (Factors 3, 7) pinion gear teeth. 79/21 = 3.7619:1 Gear ratio from countershaft to the differential case
10:41 The countershaft speed at 250 km/h (155 mph) = 7063 RPM
11:08 The motor rotor shaft and drive gear with 31 teeth (Prime Number)
11:35 MUST SEE Comparison of the front rotor to the rear performance rotor
12:56 Maximum torque at a vehicle speed comparison
15:36 Motor rotor speed sensor and reluctor wheel
16:49 MUST SEE SKF Ceramic Bearing (Silicon Nitride) on the rotor
17:43 The rotor is in a wet environment and cooled by the transmission fluid
18:33 MUST SEE Rotor shaft grounding rings with conductive filaments from (AEGIS?)
19:37 Shaft grounding protects bearings from damage from electrical current
20:10 The Rotor Shaft with 31 gear teeth drives the 77 (Factors 7, 11) tooth counter gear. 77/31 = 2.4839:1 Gear ratio.
20:52 See all three gears in the reduction gearbox with an overall gear reduction of (79/21) x (77/31) = 9.3441:1
21:26 The differential and the axle half shaft and jackshaft to reduce torque steer
22:23 Video Section 2 - Specialized Bearings
22:58 How Tesla run bearings at higher speeds than their limiting speeds with lubrication
23:07 Video Section 3 - Specialized Lubrication for bearings
23:34 The 20 tooth oil pump gear is overdriven by the differential ring gear 20/79 = 0.2531:1 gear ratio (3.95 times faster than the ring gear)
24:18 The transmission fluid drain and fill plugs
24:39 The fluid refill procedure
25:45 MUST SEE The proper fluids for the front-drive unit (Mobile SHC 629 and Dexron VI)
28:00 The path of the pressurized transmission fluid to six destinations
28:09 1. Lubrication and cooling to the motor gear and conductive bearing
29:08 2. Through the fluid-to-coolant heat exchanger to remove or add heat
31:04 3. Cool fluid is sprayed on the stator frame and right side windings for cooling through a sparge pipe
32:24 4. Cool fluid is sprayed on the non-conductive bearing and the right side of the rotor
32:58 5. Cool fluid is dripped on the stator frame and left side windings
32:47 6. Cool fluid is sprayed on the left side of the rotor
33:48 Transmission fluid fill capacities
34:42 Video Section 4 - Electrical Components
34:50 MUST SEE The three-phase, four-pole, 48 slot stator
35:55 The milli-ohm resistance of the stator windings with a Hioki RM3548 Resistance Meter
36:48 High-Performance induction motors versus high-efficiency Internal Permanent Magnet Synchronous Reluctance Motors (IPM-SynRM)
39:30 The inverter and its connection to the stator
41:42 The stator temperature sensor
42:40 How the stator frame is mounted with the stator housing
45:18 Thank you for your donations
ABOUT US
Weber State University (WSU) Davis Campus - Automotive Technology Department - Advanced Vehicles Lab. A technical description and operational demonstration of the Tesla Model S Front Drive Unit (FDU).
ADDITIONAL TRAINING FOR YOU
DONATE TO OUR DEPARTMENT
Комментарии