filmov
tv
#1 Mistake Made When Flux Core Welding (one simple Trick)
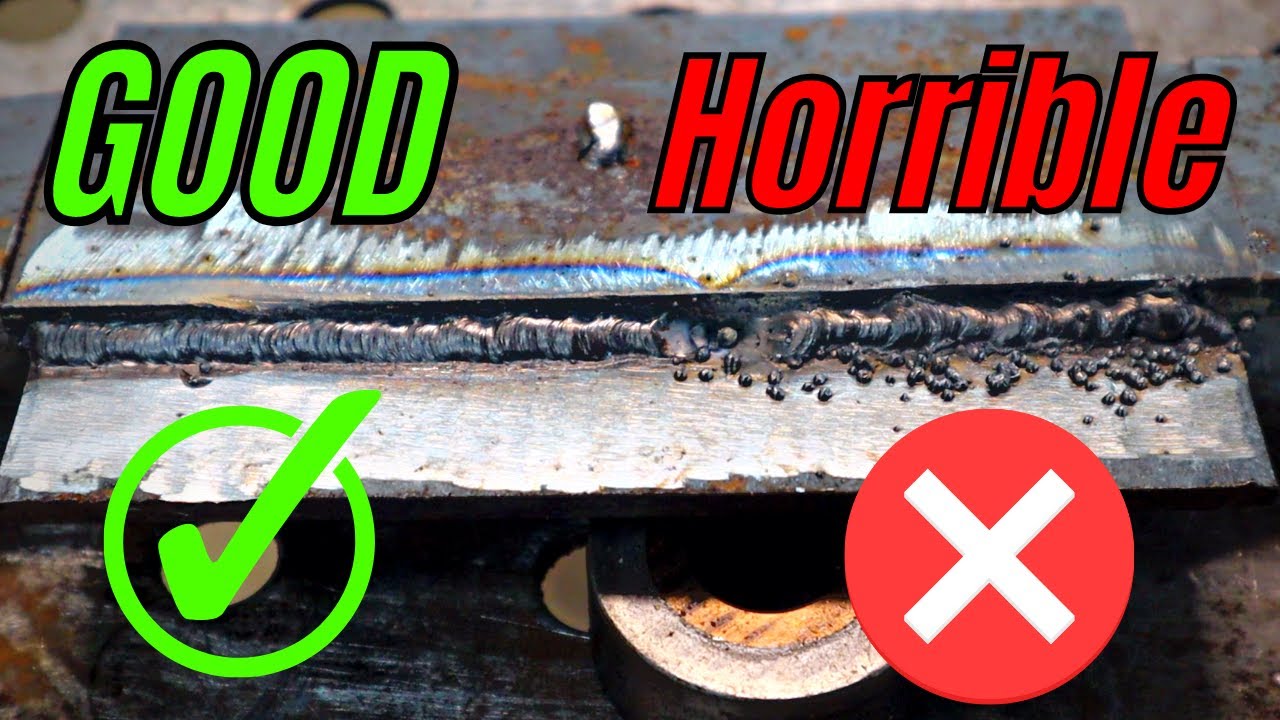
Показать описание
Is your flux core welder laying down some horrible welds? Before you give up on it check this trick out first! So many people including pro welders make the mistake of running the wrong polarity when using a gas-less flux core wire. For most general welding when using Stick (SMAW) and MIG processes you would use reverse polarity which mean (+) lead and (-) ground. This is also referred to electrode hot. The two processes that require straight polarity meaning electrode (-) and ground (+) are TIG and flux core (FCAW). Since MIG and Flux core are very similar it is very common that they are mistaken to both use the same polarity. So go out there and make sure you have your flux core machine set up properly before bashing it!
#1 Mistake Made When Flux Core Welding (one simple Trick)
TOP 5 Mistakes When Flux Core Welding With LRN2DIY
#1 Mistake Made When Flux Core Welding(one simple Trick) | Flux Core Welding Defects 100% Trips
#1 Tip and Trick to Improve Flux Core Welding
Flux Core Welding: #1 Beginner Mistake and How to Fix It
Learn Perfect Flux Core Welds In 10 Mins | Gasless Flux Core Welding For Beginners Tips And Tricks |
#1 Way to Get Better Flux Core Welds
Gasless Flux Core for Beginners #1 BIG Thing
Laravel | Desarrollando un CRM (Parte 1)
Without Flux There Would be No Good Solder Connection!
SOLDERING MISTAKE #1 (Flux quantity)
Gasless Flux Core - Beginner Mistake STICKOUT
What's the purpose of FLUX when soldering? | GOT2LEARN
Flux Core WELDING Basics: #1 Beginner Mistakes W/ HF Titanium
Tech Tips: Self-Shielded Flux Cored Arc Welding (FCAW-S) Troubleshooting
Don't use too much flux when soldering copper pipe, here's why! (Full vid in description b...
Gasless Flux Core #1 BIG Thing POLARITY
3 Flux Core Welding Myths DEBUNKED
3 Common Soldering Mistakes (part 1) FLUX #shorts #plumbing #plumber #soldering #fluxo
Flux core penetration and the importance of settings
Flux Core welding part 4: Can it weld thick steel?
Improve Your Flux Core Welding with this #1 Tip
Mistakes Apprentice Plumbers ALWAYS Make When Soldering
How to weld with flux core wire
Комментарии