filmov
tv
Comparison of 4 different CNC endmill router bits
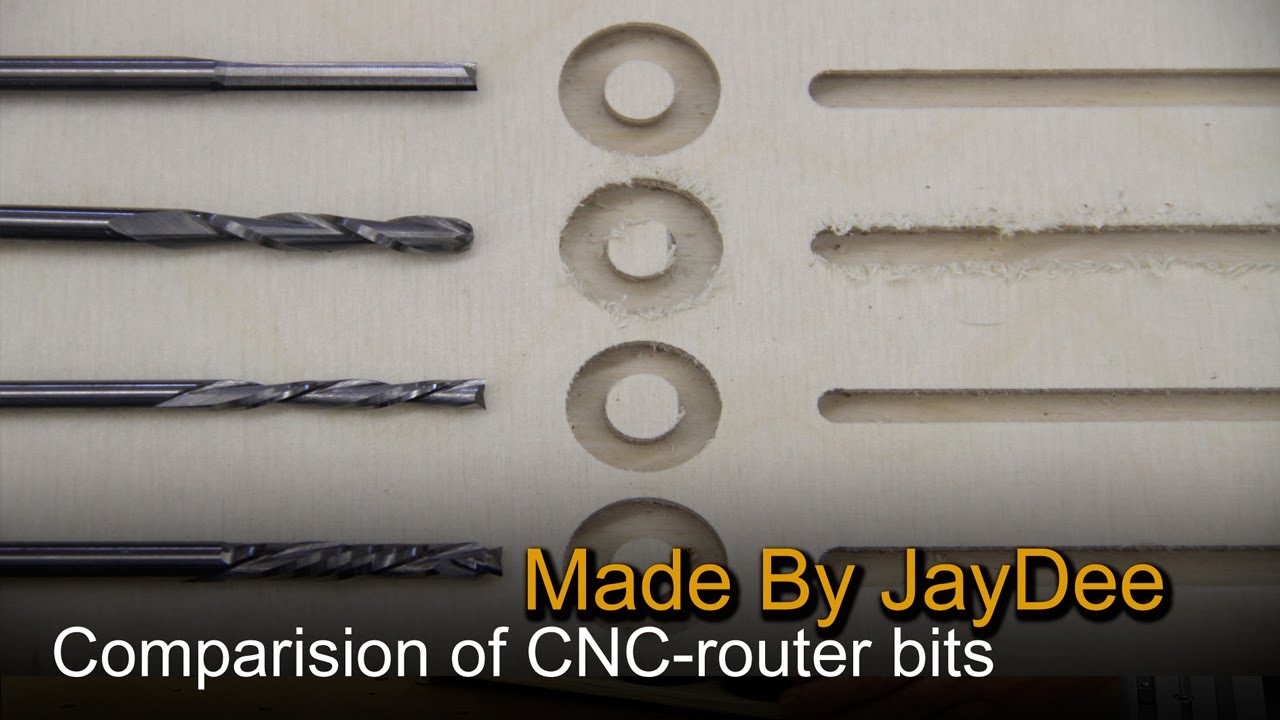
Показать описание
The chip out of some CNC router bits was annoying, so i ordered some different types and made this test.
The candidates:
1.) straight cut router bit
2.) up cut router bit
3.) down cut router bit
4.) up/down cut router bit
Like standard router bits for handheld machines, the straight cut type seems to work great on my CNC.
All four router bits are from aliexpress-Seller "CNC Cheap Store":
straight cut:
down cut:
up-/down cut:
upcut:
The candidates:
1.) straight cut router bit
2.) up cut router bit
3.) down cut router bit
4.) up/down cut router bit
Like standard router bits for handheld machines, the straight cut type seems to work great on my CNC.
All four router bits are from aliexpress-Seller "CNC Cheap Store":
straight cut:
down cut:
up-/down cut:
upcut:
Comparison of 4 different CNC endmill router bits
CNC Bits For Beginners / Upcut Vs. DownCut Vs. Compression Vs. Ball Nose End Mills!
Mekanika EVO vs PRO | CNC Milling Machines Comparison
CNC milling: how 3 axis, 4 axis, 5 axis working?
The Ultimate Desktop CNC Router Comparison - Which Should You Buy?
CNC machines - The Types of CNC Machines Explained (3 and 5 axis)
Watch BEFORE You Buy a CNC Router in 2024
Best CNC Router Machine for Beginners in 2024 | Top 5 | Cut/Engraving
CNC Q & A Podcast | Episode 4
5 axis cnc woodworking machine cnc router
The Hidden Costs of CNC's!
Watch This Before You Buy A CNC Router In 2023
3 Axis, 4 Axis & 5 Axis CNC Milling: Best Router?
10 Differences Between CNC Spindles & Routers (I Use Both)
Game Changing CNC Machine for Small Woodworking Shops
CNC vs Laser. Which Should You Get First?
The Ultimate CNC Router Review Buyers Guide, Best CNC Routers
The First Samurai - The pinnacle of Desktop CNC Machines - Official launch
CNC Machining - 3, 4 & 5th Axis? Explained
Which is the Best CNC for You? Avid CNC or Phantom CNC?
CNC Mill Tool Holding for R8 Spindles - Comparing All Options
So You Want to Buy a CNC Mill, Part 4 Rough Cost Compare
Comparing CNC machines for luthiery work | Making the TCI 5050 CNC
Did you know this about CNC machines? - 3, 4 & 5 axis CNC machines EXPLAINED | Engineering 101 -...
Комментарии