filmov
tv
Magnetic Air Engine
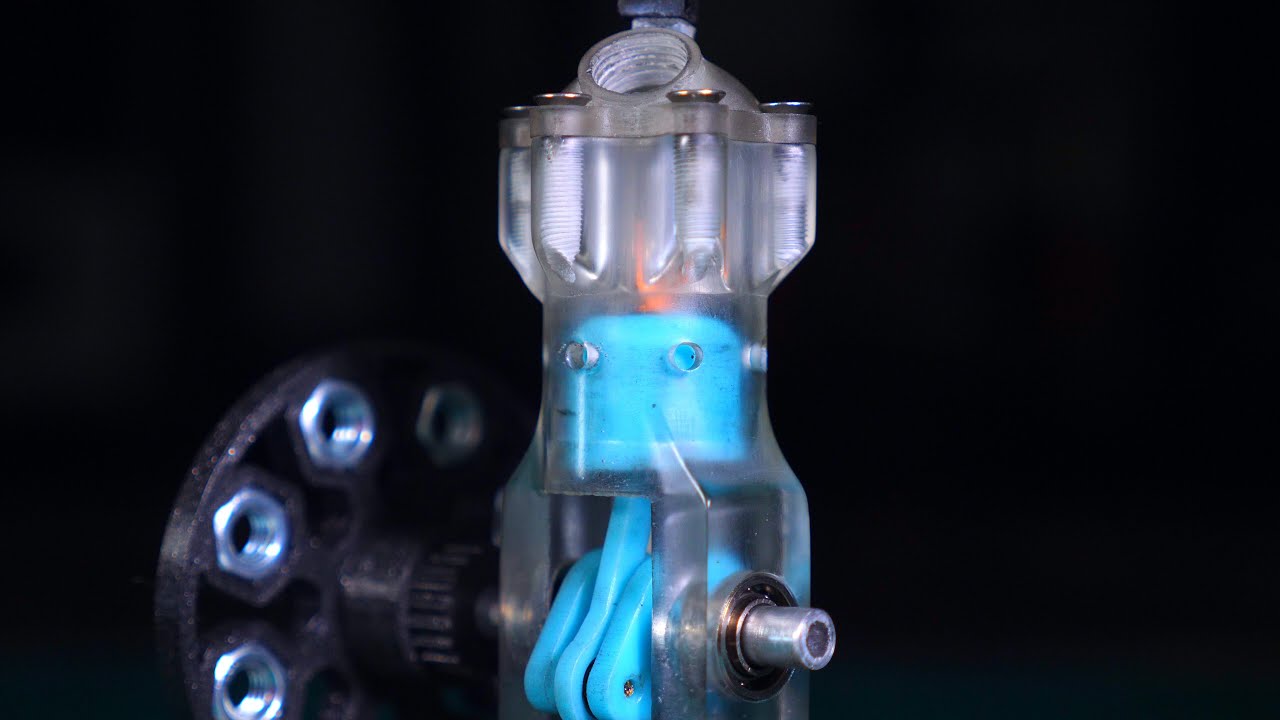
Показать описание
3D Printers
#engine #magnetic #3dprinting
Magnetic Air Engine
GM CEO: 'This New Engine Will CHANGE The World!'
Can I 3D Print a Magnetic Air Engine?
Could I Make a MAGNETIC Engine that Runs on Air?
selfrunning magnet motor powering loads and is accelerating #shorts
Making V6 Engine Using Magnets
Magnet Power Generator, Autopower Engine gadgets/Viral invention #shorts #gadgets
Optimising an Air Engine
Suzuki V Strom 650 Air Filter Upgrade
How I Powered My Magnetic Air Engine! #shorts
Amazing Magnetic Stirling Engine - Ultra Low-Temperature #shorts #stirling #engine
V6 Engine using neodymium Magnets
4,500RPM Air Engine
Magnetic Air Engine #shorts
Amazing Magnetic Engine Design No need to fuel or battery to run can run magnetic field charge
We use magnets as pistons - what will happen?
Gearless Magnetic Transmission - You Can't Break These Gears
Making a LEVITATING Lego Generator Powered by Air
Secret new helicopter test flight. Bio magnetic power engine
Water Air Engine
Magnetic 4 Piston Engine By Om and Yashil
Which is the best Stirling engine
free Energy magnetic project fan working #shorts #viral #update #amazing #
3 Amazing Experiments with Magnets | Magnetic Games
Комментарии