filmov
tv
Make custom PCBs with the Sienci CNC and FlatCAM!
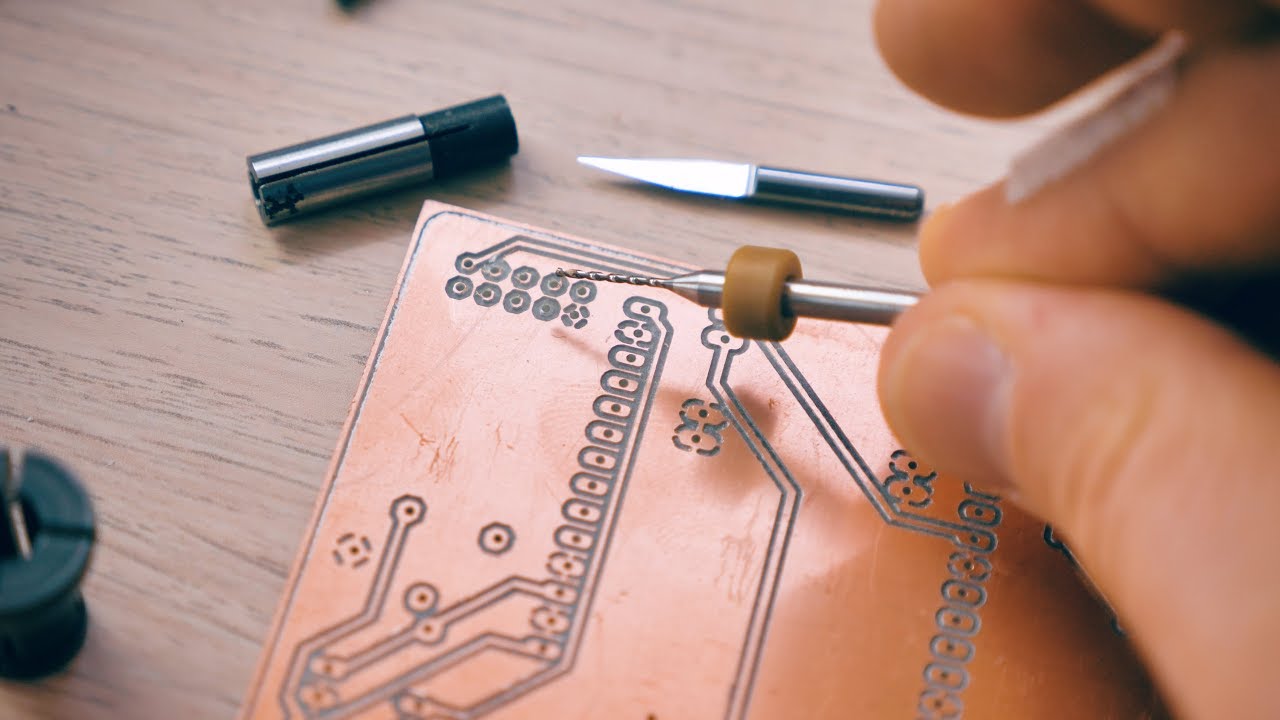
Показать описание
I've always wanted to make my own PCBs - and with a CNC machine, a few tool bits and a few pieces of software it's actually a super fast and straightforward process! In this video, I show how I used Eagle and FlatCam to create an isolation-routed circuit board on the Sienci Mill One, complete with a milled-out contour and all holes drilled.
Components used
Tools used
Software used
Eagle files
Product links are affiliate links - I may earn a commission on qualifying purchases (at no extra cost to you)
Components used
Tools used
Software used
Eagle files
Product links are affiliate links - I may earn a commission on qualifying purchases (at no extra cost to you)
PCB Creation for Beginners - Start to finish tutorial in 10 minutes
You can now PRINT PCBs! Creating a homemade PCB with the Voltera V-One PCB Printer!
Make custom PCBs with the Sienci CNC and FlatCAM!
DIY PCBs At Home (Single Sided Presensitized)
'A Machine PERFECT for Making PCBs at Home' Is what they said!
The fastest way to make crisp PCBs at home!
This credit card sized PCB can SAVE YOUR LIFE! (Shrinkify your projects with a 4 Layer PCB)
DIY PCB Fabrication (Dry Film Inkjet Method)
Making PCBs with PCBway
PCBWay - The Way to Make PCB Professionally and Economically
Design and Build a PCB - SMD LED Learn electronics engineering
How To Make A Custom PCB From Design To Assembly
Make professional PCBs at home
How to make HIGH quality PCBs at home
How to Design Mechanical Keyboard PCBs with Kicad
How Do PCBs Work?
Easily Design Your Own PCBs! The SAMD21 HCC Module
How to Make A PCB Making CNC in Your Budget
How to make custom PCBs at home
my most expensive pc building mistake... #shorts
Quick start for Pad2Pad custom PCBs
Making PCBs with fiber laser
Printing PCBs At Home!
How to make custom PCBs at home - Part 1.
Комментарии