filmov
tv
What IS Concentric Twisting? | Motorsport Wiring [#TECHTALK]
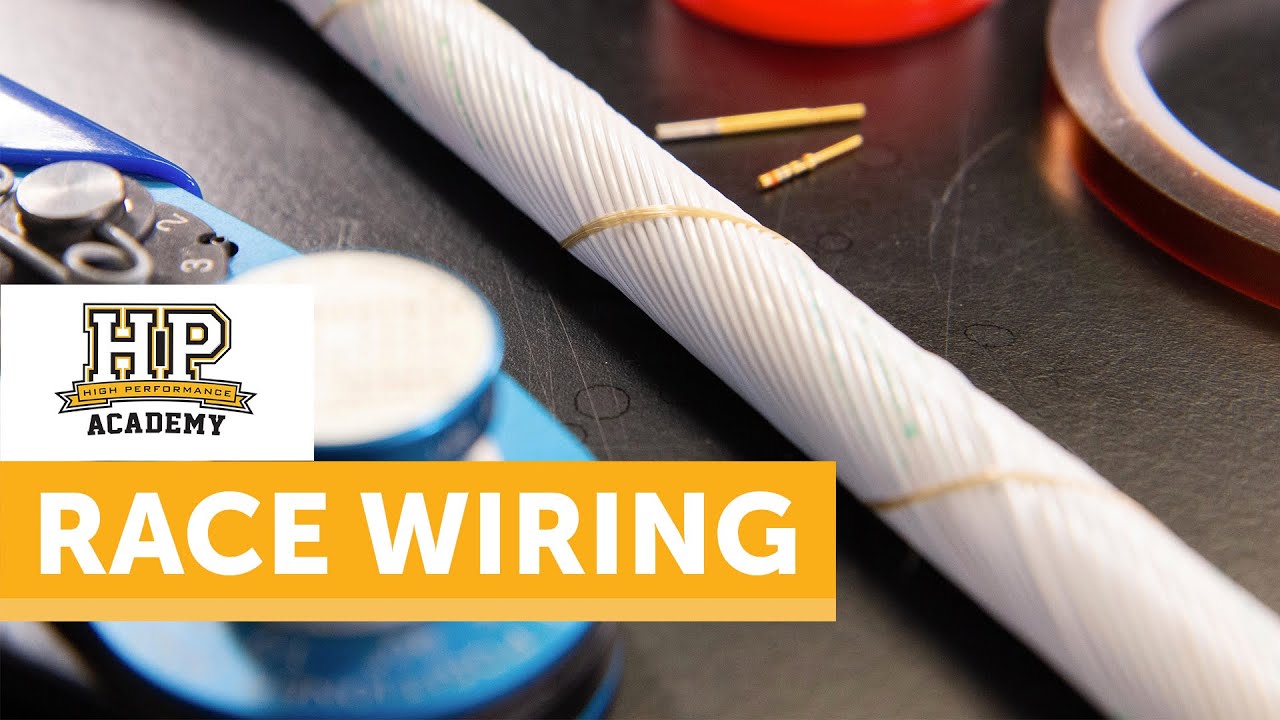
Показать описание
Ever wondered what goes into laying up a concentrically twisted harness and why it is a go-to technique for wiring harnesses used in professional motorsports like Formula 1, MotoGP and many more?
Get $50 off your next HPA course purchase with this coupon: 3NADNF
Concentric twisting has a number of advantages when it comes to reliability and durability, but they do come at a cost which Andre explains in this [TECH TALK] on the use of concentric twisting in a wiring harness.
As well as the detail behind this method, wiring stripping and connector crimping are also covered to give you all the knowledge you need to decide if this is a technique you would like to employ in your own wiring projects, and if not, understand why it is used by others.
TIME STAMPS:
0:00 - Intro
0:50 - Breaking down a Concentrically Twisted Harnesses
2:15 - The Advantages
3:55 - The Disadvantages
4:58 - Stepping up the layers
6:16 - Connectors used
7:58 - Crimp Tooling
8:49 - Which Positioner do I use?
9:24 - Stripping the wire and the correct tool for the job
11:43 - Stripping & Crimping demonstration
13:10 - Inserting the crimp into the connector
14:26 - What if I insert the crimp in the wrong place?
15:04 - Loops on the back of the connectors?
16:46 - Performing Strain relief loops
17:16 - Another tip for your harness
19:35 - The setup
21:35 - Building the Harness
24:04 - Completed Layer
24:39 - Summary
25:00 - Do you want to learn more about concentric twisting?
25:21 - Outro
Courses Mentioned:
#highperformanceacademy #learntotune #concentrictwisting #dontletthesmokeout #wiring101 #twistedworld
Комментарии