filmov
tv
Take control of your MIG Welding! I’ll drop the 🤯 in the comments⬇️
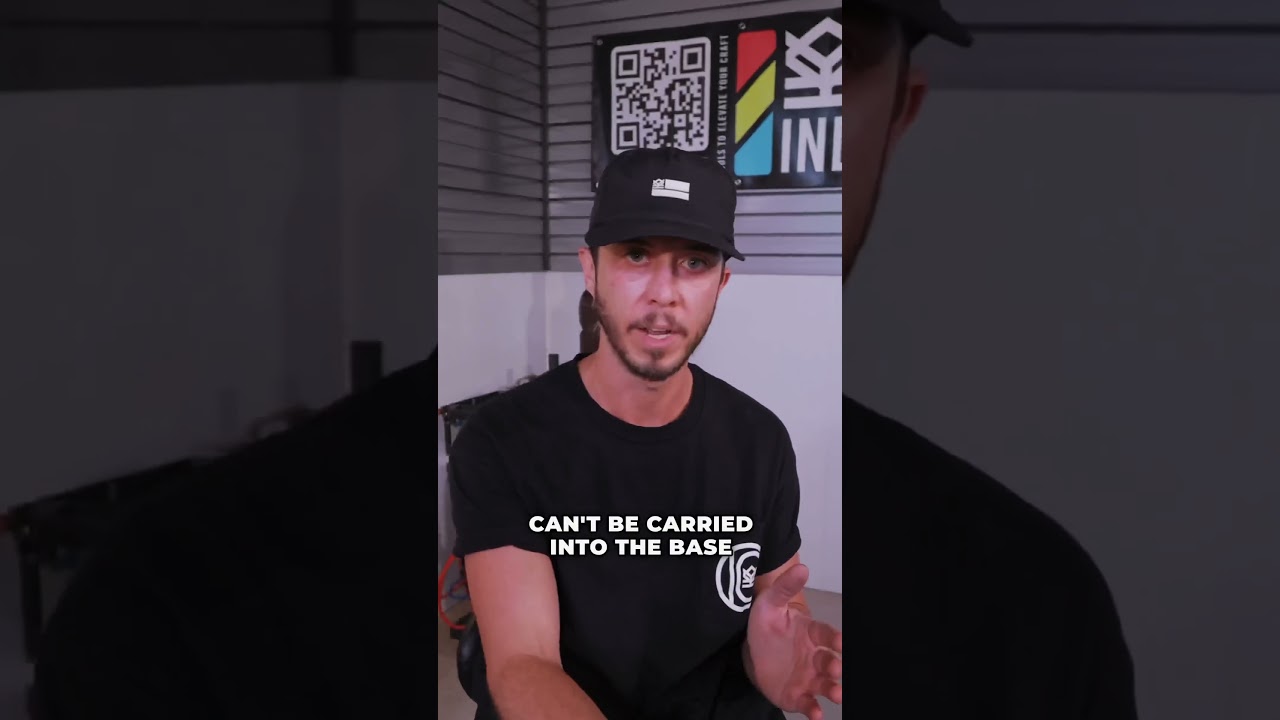
Показать описание
3 MIG Welding Tips From A Welding Instructor
How to Make Consistent MIG Welds
MIG Welder Settings: MIG Welding Basics for Beginners
Basic mig welding technique for beginners
Take control of your supply chain! How MiG boosts your productivity and delivery excellence
Setting Wire Speed On A Mig Welder To Match Voltage, Must See For Beginners Learning Welding
Perfect Mig Welder Settings in 3 Easy Steps
Mig Welding Basics part 3-Setting Voltage and Wire Speed
Mastering Free Fire: Keyboard andMouse Gameplay with Handcam #shorts
MIG Welding Basics For BEGINNERS!! How To Set Up Your Welder + Tips, Tricks & Techniques!!
beginner welding mig # #migwelding #sorts
HOW TO MIG LIKE TIG WELD (Stacking Dimes) W/ OVERKILLRACINGANDCHASSIS w/ *Tips and Techniques*
Simple MIG Welding Technique - Flat, Horizontal, Vertical & Overhead | Welding Tips & Tricks...
How NOT TO Weld: Most Common MIG Welding Mistakes
Simple technique welding Mig-Mag #welding #sorts
MIG Welding Basics For Beginners
(HELP) I Can't See My Mig WELDS (Top 5 Tips)
Go Gasless! See How Simple MiG Welding Can Be
Fix This MIG Welding Problem
Guaranteed Better Mig Welds Or Your Money Back!
MIG Welding Quick Tip - How to Fix Excessive Spatter - MIG Welding from Eastwood
Push vs. Pull Methods in MIG Welding
5 MIG Welding Mistakes I Made as a Beginner
MIG Welding Techniques Explained!
Комментарии