filmov
tv
No Shoulder Shadows: Under-Cabinet Lighting
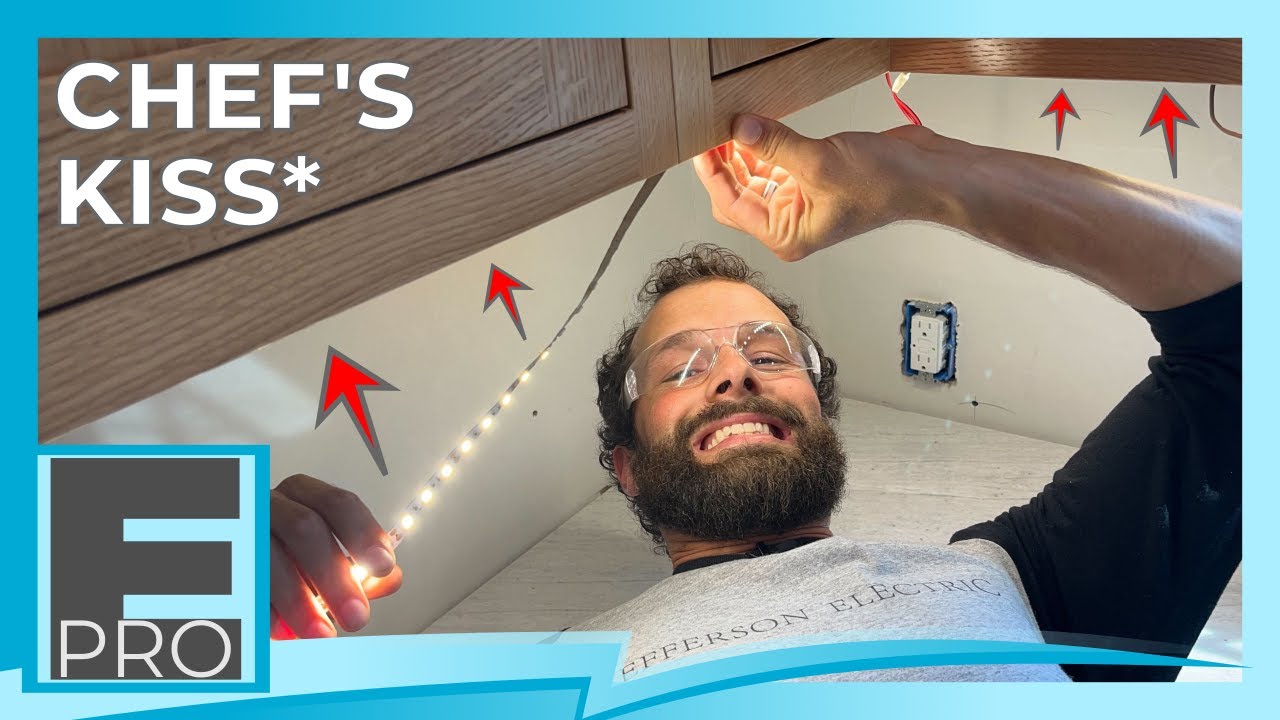
Показать описание
Electric Pro Academy - Real skills to make real money.
Synopsis:
Joel breaks down a master electrician’s thought process and mounting of _______
Besides secondary power sources, under-cabinet lighting is probably the most “en vogue” electrical project these days. With minimal power-draw requirements, lots of product options, and plenty of visual appeal, we highly recommend it to customers and EPros alike! In this video we’ll include our favorite LED strip light brand, the unique parts and materials needed, and the best ways to avoid headache…by showing you a few headaches of our own!
Laced within the technical instruction are recommendations and points of professionalism employed daily by Jefferson Electric masters, journeymen, & apprentices.
If the instruction in this video is unclear or skew to what you are searching for, feel free to comment below for additional assistance.
Thank you for watching; we value your feedback and monitor this channel daily.
EPRO-2-Call:
Products We’d Recommend:
*EPRO endorses pro-level tools & materials, and receives a small commission for purchases through our links from Amazon & other affiliate programs. We’d be happy to recommend more cost-effective products for DIYers and low-frequency users if you engage with us in the comment section!
National Electrical Code (NEC) referenced in our videos:
Outline:
0:00 - Introduction
0:38 - Tools & Materials
1:56 - Power
4:25 - Installing Self-Adhesive Strip Lights
15:04 - Business Tip: Totes
16:22 - Headache #1: Solder Point or Cut Point?
17:20 - Headache #2: No Light!
17:32 - Troubleshooting Driver-Transformer
20:50 - Replacing Pinched Wire
21:52 - Bonus: Air Switched Garbage Disposal
22:38 - Cliff Was Right…Again.
Connect With Us:
Electric Pro Academy is a multimedia team dedicated to training and instructing DIYers and professional electricians for the growth and dignity of the craft nationwide.
Jefferson Electric installs and services residential, commercial, solar, and Tesla systems in Indianapolis, IN.
Synopsis:
Joel breaks down a master electrician’s thought process and mounting of _______
Besides secondary power sources, under-cabinet lighting is probably the most “en vogue” electrical project these days. With minimal power-draw requirements, lots of product options, and plenty of visual appeal, we highly recommend it to customers and EPros alike! In this video we’ll include our favorite LED strip light brand, the unique parts and materials needed, and the best ways to avoid headache…by showing you a few headaches of our own!
Laced within the technical instruction are recommendations and points of professionalism employed daily by Jefferson Electric masters, journeymen, & apprentices.
If the instruction in this video is unclear or skew to what you are searching for, feel free to comment below for additional assistance.
Thank you for watching; we value your feedback and monitor this channel daily.
EPRO-2-Call:
Products We’d Recommend:
*EPRO endorses pro-level tools & materials, and receives a small commission for purchases through our links from Amazon & other affiliate programs. We’d be happy to recommend more cost-effective products for DIYers and low-frequency users if you engage with us in the comment section!
National Electrical Code (NEC) referenced in our videos:
Outline:
0:00 - Introduction
0:38 - Tools & Materials
1:56 - Power
4:25 - Installing Self-Adhesive Strip Lights
15:04 - Business Tip: Totes
16:22 - Headache #1: Solder Point or Cut Point?
17:20 - Headache #2: No Light!
17:32 - Troubleshooting Driver-Transformer
20:50 - Replacing Pinched Wire
21:52 - Bonus: Air Switched Garbage Disposal
22:38 - Cliff Was Right…Again.
Connect With Us:
Electric Pro Academy is a multimedia team dedicated to training and instructing DIYers and professional electricians for the growth and dignity of the craft nationwide.
Jefferson Electric installs and services residential, commercial, solar, and Tesla systems in Indianapolis, IN.
Комментарии