filmov
tv
A Lesson in Humility
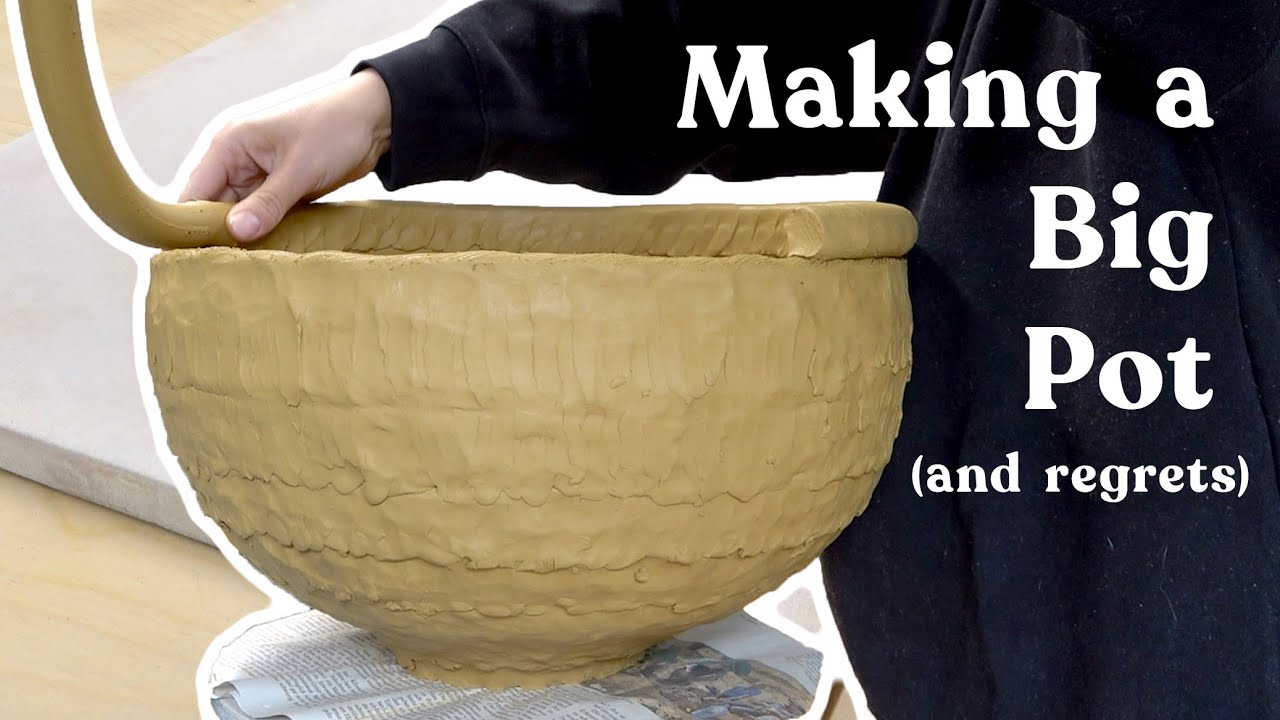
Показать описание
When you try to make a big pot, but the universe has other plans.
//ONLINE CLASSES
//SHOP
//TOOLS & CLAY
Stuff I use and recommend:
//SAY HI!
//ONLINE CLASSES
//SHOP
//TOOLS & CLAY
Stuff I use and recommend:
//SAY HI!
Be humble -- and other lessons from the philosophy of water | Raymond Tang
A Lesson in Humility
How to be Humble
How To Give A Lesson In Humility To An Arrogant Player 🔥
A Lesson in Humility (Part 1 of 2) — 07/29/2020
Suki Waterhouse & Belle and Sebastian - Every Day's A Lesson In Humility (Official Audio)
The Prideful Ant | A Story about Pride and Humility
A Lesson In Humility - Bishop TD Jakes
Jesus and the Pharisees A Lesson in Humility
Sadio Mané's Humble lifestyle: A Lesson in True Greatness 🌟 #Inspiration #Humility #Football...
A Lesson in Humility || Crisp Video
A Lesson in Humility
MUST SEE!!! A Lesson In Humility (BE HUMBLE!)
When Humility Looks Like Arrogance | Lesson 7 of Drawing Near | Study with John Bevere
Symbolical A Lesson in Humility Promo 2014
A Lesson in Humility
A Lesson in Humility: The Same Stage, Different Levels
Jesus Teaches About Humility | Stories of the Bible
Humility in Power: A Former Undersecretary's Lesson on Leadership
PHILIPPIANS 2 | 'WHAT DOES HUMILITY LOOK LIKE?'
Degs - A Lesson In Humility
God's lesson on Humility
OBJECT LESSON About Pride and Humility
The Dog Vs Squirrel: A Lesson In Humility And Wisdom - An Animated Story
Комментарии