filmov
tv
Can you use a CHEAP CNC ROUTER for GUITAR BUILDING?
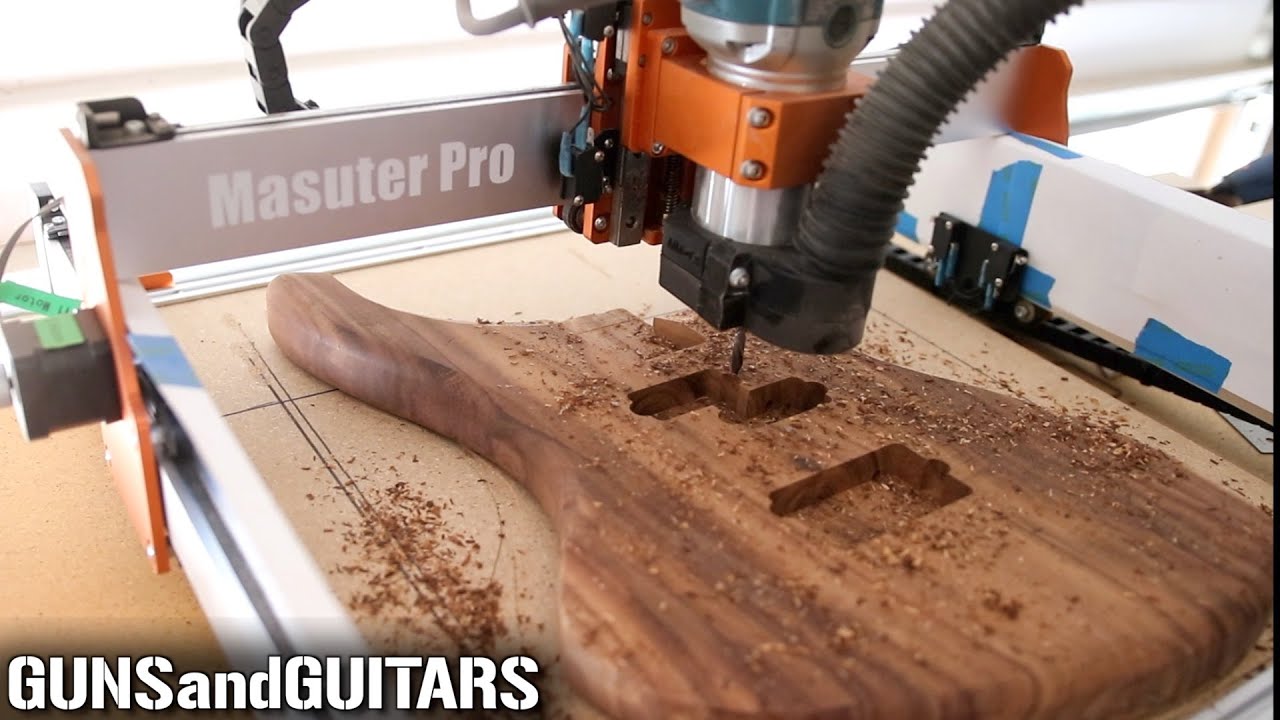
Показать описание
I've always wanted to see if I can use a cheap small CNC router to do some custom guitar work. The CNC router I chose for this test is the FoxAlien Master Pro, which has rugged all aluminum construction, a 15.7"'x15.75" work area (with extension kit coming soon), accepts a Makita router, and comes in at less than $650. For more information, or to make a purchase, check out the links below:
*Prices mentioned in this video are subject to change without notice, please check the links for current pricing.
Full disclosure: I am an Amazon Associate and FoxAlien affiliate, and the links in this description are affiliate links, which means that if you make a purchase, it doesn't cost you any more money, but I will earn a commission. I would like to thank FoxAlien for sending me this machine for testing and evaluation purposes.
Instagram @gunsandguitarsofficial
Current Patrons (as of this video)
$5 Patrons:
Yosemite Sam
Mynameisnotjeff
David J Kitelinger
Derek Weathersbee
John Clark
Tanner Redman
David Morgan
David Vaughan
LesLamcke
Fabian Muresan
Alejandro Vega
Captain Rudy 4021
Chris Hopkins
Tony Butterworth
j
Ben Berscak
Jeff Savoie
Mike Bennett
PEEPEE POOPOO
Colin Jenison
Will Fowler
Aidan Peet
Matthew Renegar
Tommy Transplant
Aaron
Daniel Newman
Brian Wigton
Dave Speller
Elijah R Sell
Andrew Epperson
Jeffery A Fallon
Andrew Jeffries
Philip Honeycutt
Travis Blakely
Daniel Russell
Declan Fischer
Paul Messina
Joseph Lacroix
samuel ungeheier
Carlos A. Lizarraga R.
Chriz
Conor O’Doherty
James Populo
Ian Davies
Alex Trocker
Laramie Reg
Troy Thompson
JeffG
Sean Quigg
Dave Van Englehoven
Jamie Cucalon
Maro
Osel Rodrigues
David Anderson
Gerald Ringgold
Brian Brown
Donald West
ChaoticDanny
Ron Clevenger
Matthew Burch
Victor A Estes
Ken Widmer
$10+ Patrons:
Adam West
Brandon Leafblad
Christopher Heath
john best
Nicholas
Peter Champlin
The Grapeman Reform
Marcus Warren
James Lamb
Koss Billingham
Drew Lawton
Jim Shepard
Mark Cockrell
William Herrera
Chris Thomason
John Morris
Patrick Emry
David Capp
Tim Chapin
Timothy Potter
Austin Hewlett
James Robers
Seth Johnson
James Shepard
Touch of Oops
Justin Setters
Jack Stow
Daniel Rota
Michael Fierro
Jeffery Maslan
Johnathan Simmonds
Wolfgang Widmer
James Campbell
Corey Muxlow
Casey Smalley
Tim Stephens
E
Matthew Caffell
Clint Walker
Drew
Al Philp
Robert Lewis
Jaden Bass
Rob Haag
Gregory Clark
JoshuaTroller
Josh Perez
Samuel Ungeheier
Billy Sullivan
Brandonlee
Background music made by Jordan Rowan of iMakeMusic
*Prices mentioned in this video are subject to change without notice, please check the links for current pricing.
Full disclosure: I am an Amazon Associate and FoxAlien affiliate, and the links in this description are affiliate links, which means that if you make a purchase, it doesn't cost you any more money, but I will earn a commission. I would like to thank FoxAlien for sending me this machine for testing and evaluation purposes.
Instagram @gunsandguitarsofficial
Current Patrons (as of this video)
$5 Patrons:
Yosemite Sam
Mynameisnotjeff
David J Kitelinger
Derek Weathersbee
John Clark
Tanner Redman
David Morgan
David Vaughan
LesLamcke
Fabian Muresan
Alejandro Vega
Captain Rudy 4021
Chris Hopkins
Tony Butterworth
j
Ben Berscak
Jeff Savoie
Mike Bennett
PEEPEE POOPOO
Colin Jenison
Will Fowler
Aidan Peet
Matthew Renegar
Tommy Transplant
Aaron
Daniel Newman
Brian Wigton
Dave Speller
Elijah R Sell
Andrew Epperson
Jeffery A Fallon
Andrew Jeffries
Philip Honeycutt
Travis Blakely
Daniel Russell
Declan Fischer
Paul Messina
Joseph Lacroix
samuel ungeheier
Carlos A. Lizarraga R.
Chriz
Conor O’Doherty
James Populo
Ian Davies
Alex Trocker
Laramie Reg
Troy Thompson
JeffG
Sean Quigg
Dave Van Englehoven
Jamie Cucalon
Maro
Osel Rodrigues
David Anderson
Gerald Ringgold
Brian Brown
Donald West
ChaoticDanny
Ron Clevenger
Matthew Burch
Victor A Estes
Ken Widmer
$10+ Patrons:
Adam West
Brandon Leafblad
Christopher Heath
john best
Nicholas
Peter Champlin
The Grapeman Reform
Marcus Warren
James Lamb
Koss Billingham
Drew Lawton
Jim Shepard
Mark Cockrell
William Herrera
Chris Thomason
John Morris
Patrick Emry
David Capp
Tim Chapin
Timothy Potter
Austin Hewlett
James Robers
Seth Johnson
James Shepard
Touch of Oops
Justin Setters
Jack Stow
Daniel Rota
Michael Fierro
Jeffery Maslan
Johnathan Simmonds
Wolfgang Widmer
James Campbell
Corey Muxlow
Casey Smalley
Tim Stephens
E
Matthew Caffell
Clint Walker
Drew
Al Philp
Robert Lewis
Jaden Bass
Rob Haag
Gregory Clark
JoshuaTroller
Josh Perez
Samuel Ungeheier
Billy Sullivan
Brandonlee
Background music made by Jordan Rowan of iMakeMusic
Комментарии