filmov
tv
Milling 13/16' Holes in Angle Iron for a Fast Turn-Around
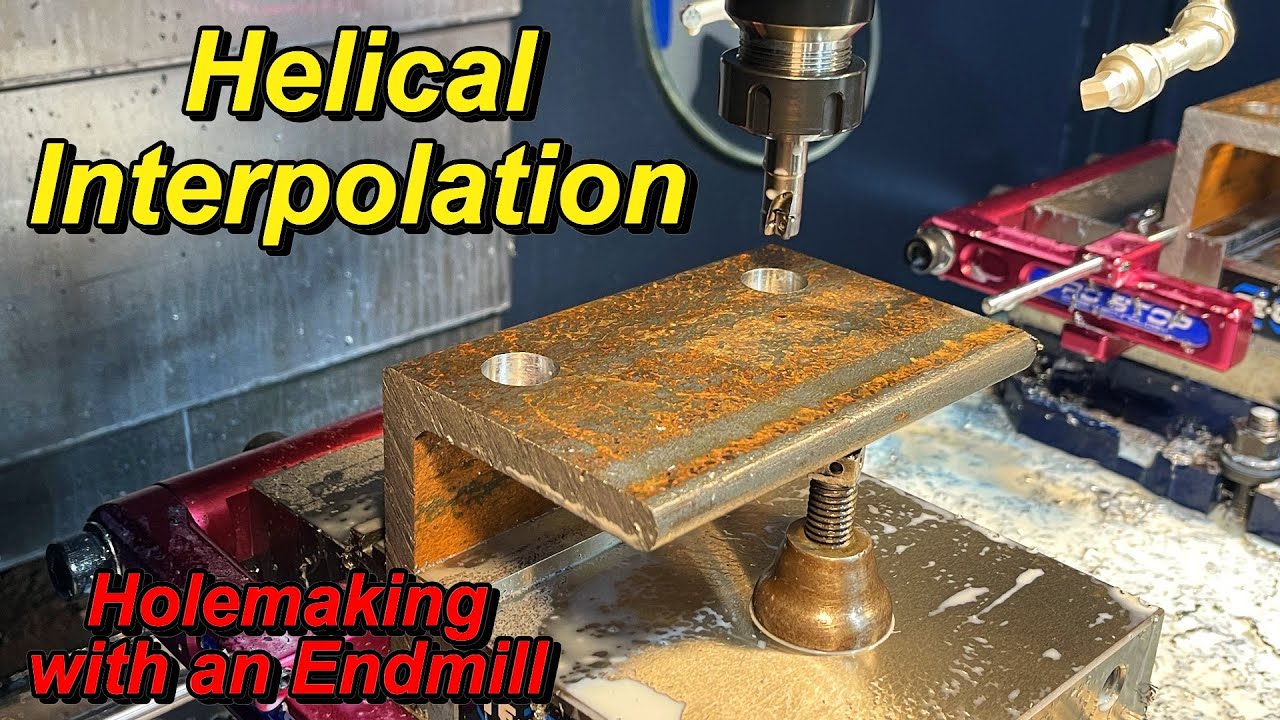
Показать описание
The welding shop had a stack of 4x4x1/2 angle iron pieces cut 6" long that required some 13/16" holes machines in them and they needed them back right away. This was a great opportunity to use the @MilltronicsUSAInc TRM3016 cnc mill with my @TungaloyCorporation 1/2" Tung Force Rec end mill and use a helical interpolation tool path to mill the holes to size. This was a good technique to quickly get the holes machined in these parts and utilizing two work offsets as well. #cncmachining #milltronics #tungaloy
Visit my second Youtube channel where you can follow our travels, camping, RVing, cooking, and bbq! @AbomAdventures
Visit my second Youtube channel where you can follow our travels, camping, RVing, cooking, and bbq! @AbomAdventures
Milling 13/16' Holes in Angle Iron for a Fast Turn-Around
Milling Project Video 8: Drilling Holes
Making a VERSATILE Mini Pallet || INHERITANCE MACHINING
tos w100a HBM milling angle plates to dimension
Making Collet Blocks || INHERITANCE MACHINING
Milling Angled Mounts
Thread milling 1/2-13
DIY Vice Stop for milling machine
Making Machinist V Blocks on a Mini Milling Machine
Holier than Thou: Precision Holes by Drilling, Boring, and Reaming
The Tool I Should Have Built Years Ago!
How To Sharpen A Drill Bit - stainless steel drill bit sharpening
Adjustable angle plate, improving and scraping - Part 1
Manual Mill Tutorial
A tool to set accurate angles on a milling machine head
GibbsCAM 2016 | Thread Milling
How to Identify Thread Pitch and Size | Tech Tips | Swagelok [2020]
New Cross Slide Handwheel Part 2 - Schaublinisation Of The Mini Lathe
How to Power Tap
How to sharpen a drill, three easy ways!
Fanuc Custom Macro B - Sphere Cavity finish milling
PLATE KA REDUCER KAISE BANAYE
CNC Machining - How to Design Parts for CNC Machining
A Better Tool Post Nut || INHERITANCE MACHINING
Комментарии