filmov
tv
5 FEA Mistakes Most Structural Engineers Make
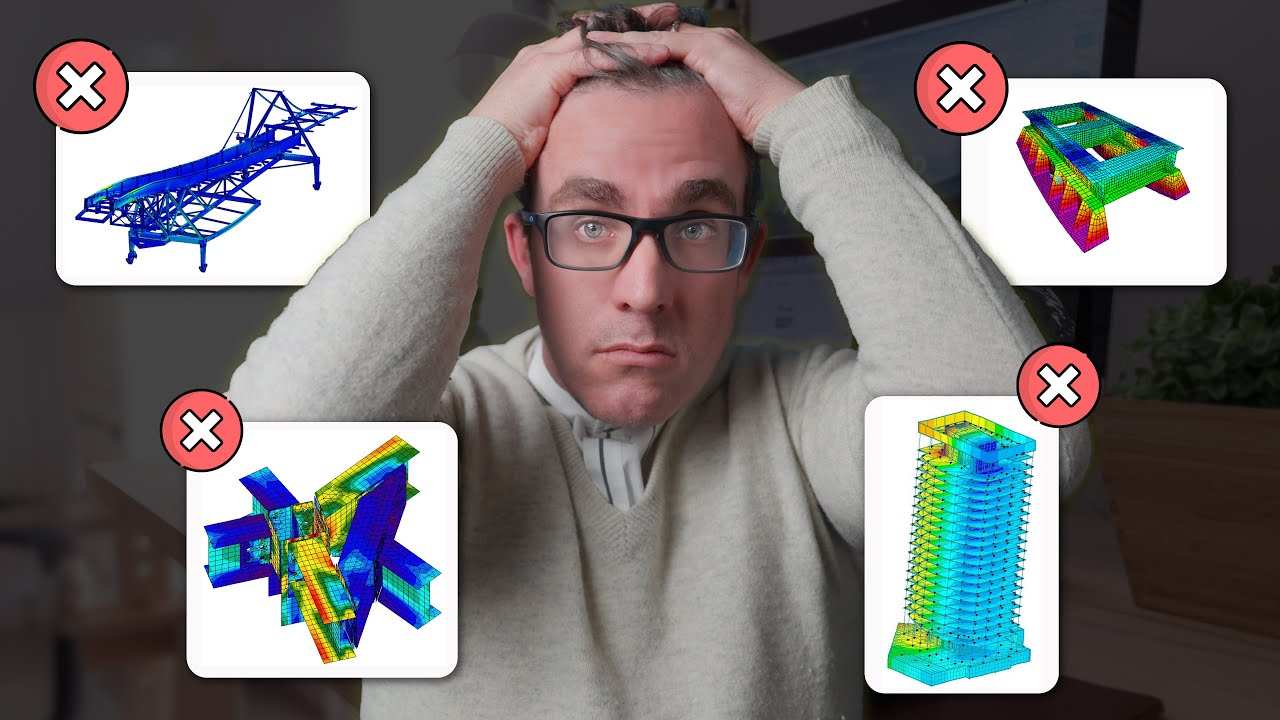
Показать описание
Finite Element Analysis (FEA) is an essential tool for structural engineers, offering unparalleled precision and efficiency in designing safe and cost-effective structures. However, even experienced engineers can fall into common traps that compromise the accuracy and reliability of their analysis. In this video, we uncover the 5 FEA mistakes most structural engineers make —and more importantly, how to avoid them.
What to watch next
🖱️ Software/Apps I recommend:
📚Recommended Engineering Books:
🎥SEO tool
🔴Disclaimer: Some of the links below are affiliate links as an Amazon Associate and other affiliate programs; I'll earn a small commission from qualifying purchases at no additional cost.
What to watch next
🖱️ Software/Apps I recommend:
📚Recommended Engineering Books:
🎥SEO tool
🔴Disclaimer: Some of the links below are affiliate links as an Amazon Associate and other affiliate programs; I'll earn a small commission from qualifying purchases at no additional cost.
5 FEA Mistakes Most Structural Engineers Make
Real Civil Engineer vs. Architecture Fails #shorts
How To Avoid Disaster When Doing Structural Finite Element Analysis.
Minecraft's Deadliest Structure!
Structural engineers, save time now!
My 5 'Clean' Code Principles (Start These Now)
Precast reinforced concrete foundations construction techniques and procedures
AI & Outsourcing: 5 Ways to Streamline Your Marketing with Jen Lehner | Ep. 50
SketchUp Tutorial for Beginners - Learn SketchUp in 10 MINUTES | (SketchUp Free 2022)
The single biggest reason why start-ups succeed | Bill Gross | TED
You’re using ChatGPT wrong
31 nooby C++ habits you need to ditch
Understanding Fatigue Failure and S-N Curves
Do Structural Engineers get Paid Well (in AUS, US, UK)
10 Design Patterns Explained in 10 Minutes
What is the most important influence on child development | Tom Weisner | TEDxUCLA
8 Email Etiquette Tips - How to Write Better Emails at Work
ANSYS 2020 Workbench Tutorial | Introduction to Static Structural | 2020 R2
Why hasn't Apple invented this yet?!
The Psychology Behind Good Advertising
Contributing to Open Source Can Change Your Life - Here’s How to Do It
What Are The Different Atomic Models? Dalton, Rutherford, Bohr and Heisenberg Models Explained
10 CSS Pro Tips - Code this, NOT that!
Structural Shapes Ranked and Reviewed - Which one Wins?
Комментарии