filmov
tv
Full logistics Guide pt.3 | BLUEPRINTS and Simulating Layouts in Satisfactory 1.0 | Tips and Tricks
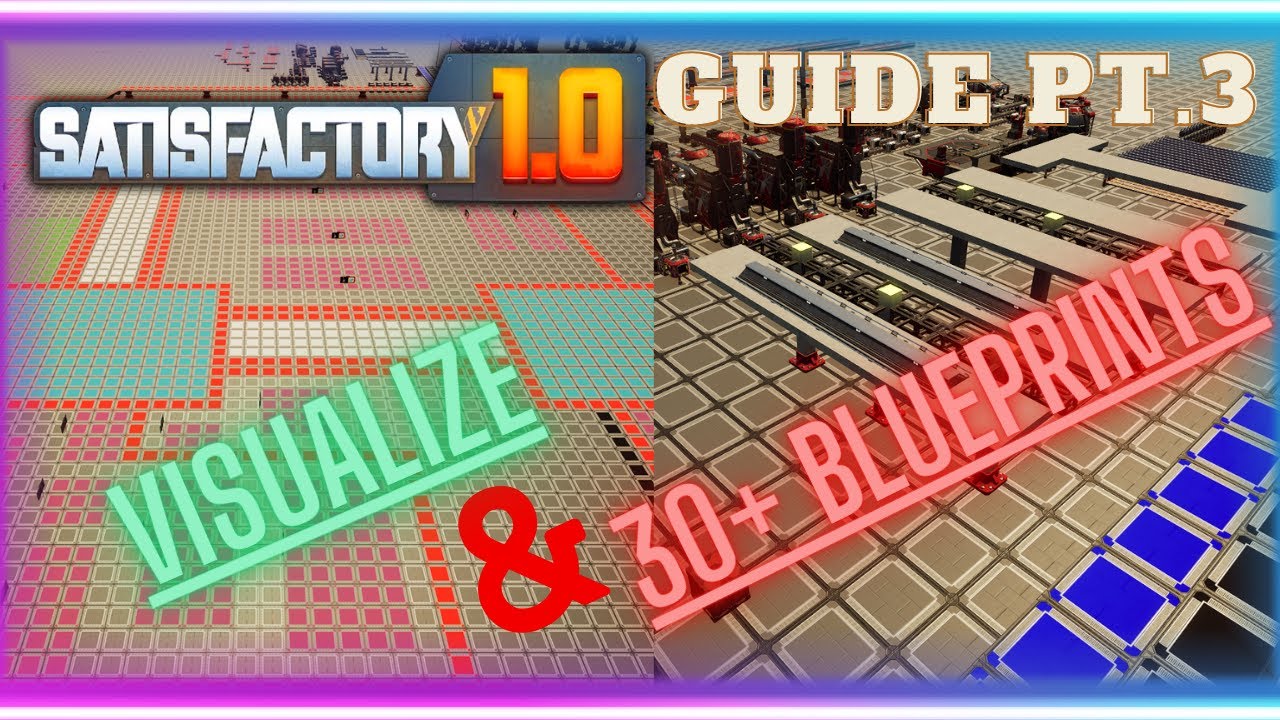
Показать описание
In this video, Jack Blade will continue teaching the method for Logistics Planning, setup and building in Satisfactory 1.0.
Today the focus is starting the process and doing a lot of the pre-planning that happens before you ever put down your first conveyor belt or blueprint
Video Links to Planners:
_________________________________________________
CHAPTERS:
0:00 - Intro
1:37 - What is simulation and visualization
3:18 - Real life examples (storytime with Jack)
8:40 - How does simulating logistics pass
9:41 - correcting mistakes from video 2
10:55 - Visualizing the layout
11:54 - How much space does each machine take
16:32 - Alternative Machine Setups
23:52 - Determining how much space capacity is needed
20:03 - Testing space layouts start here
27:13 - Blueprints time!
29:13 - Interlude
30:41 - Presenting 30+ blueprints
33:41 - Wrap up and outro
_________________________________________________
About Jack Blade:
I am an avid gamer who loves all kinds of games but there is a special place in my heart for factory, logistics and management games. I want to share that love with the world and other fans of the genres!
Satisfactory itself holds a dear place in my heart and honestly I would say it can be held up next to Minecraft on the level of pure creativity you can unleash in this game. The factory and automation as well as the logistics elements of the game just takes it to the next level. On top of that the world is beautiful and the sound design is top tier!
___________________________________________
____________________________________________
Terminology (Dictionary)
- Logistic Systems:
Constructed mechanics that facilitate transfer and organization between different Factories, Production Lines, Faucets, Storage and Sinks
-Factory:
A collection of Faucets, Sinks, Storage and Production lines interconnected with Logistics Systems that produces one or more specific end products
- (Mechanical) Translation:
Communications between different logistics systems
- Megafactory: Single massive central factory for insane amounts of production output
- Modular Factory: Multiple smaller factories with single or just a few final outputs
- Production Line: A single parts production setup within a Factory
- Logistics Layers: Different methods of resource transfer that needs mechanical translation to interact
- Logistics Hierarchy: A method of planning, sorting and thinking about logistics system construction
- Sushi Belts: Single belts with multiple different resources on
- Overflow Protection: Systems using Sinks or Translation to other Production Lines and Factories to avoid production lines stopping because of lack of Storage
- Faucet: A system that inputs resources into the game, mining nodes, spawning mobs and generating power are examples
- Sink: A system that deletes, eats up or compresses resources to reduce space usage or entirely remove them from the game, AWESOME Sinks, power usage and advanced low quantity End Product production are examples
- Storage: Mechanical features in the game that stores or buffers resources in the game. Some examples are machines internal buffers, containers, vehicles and belts
- Buildable: Any single part you place down using the multitool/build gun
- End Product: The intended part or parts produced by a Factory
- Load Balancing: Predetermining flow rates for multiple belts
- Belt Priority: Predetermining priority order of belts
- Splitter: Buildable that splits one belt into 2 or 3, has advanced variants, smart and programmable splitters
- Merger: Buildable that can merge 2 or 3 belts onto 1
- Logic: Connected buildables, logistics and game mechanics that create an automated function
- Manifold: A line of splitters or mergers that feed machines or merge outputs
- Logistics Bus: A line of relevant Logistics Layers to move resources, are sorted into hierarchies
- Buffer: Container that stores extra resources before or after other buildables, logistics systems or production lines
- Logistics Floor: A floor separate from where production machines are placed, where logistics systems are built
- Wireframing: Minimal effort outline building for purposes of aligning and visualizing the finished build
- Machine Group: a set of machines, multiple machine groups make up one production line
Today the focus is starting the process and doing a lot of the pre-planning that happens before you ever put down your first conveyor belt or blueprint
Video Links to Planners:
_________________________________________________
CHAPTERS:
0:00 - Intro
1:37 - What is simulation and visualization
3:18 - Real life examples (storytime with Jack)
8:40 - How does simulating logistics pass
9:41 - correcting mistakes from video 2
10:55 - Visualizing the layout
11:54 - How much space does each machine take
16:32 - Alternative Machine Setups
23:52 - Determining how much space capacity is needed
20:03 - Testing space layouts start here
27:13 - Blueprints time!
29:13 - Interlude
30:41 - Presenting 30+ blueprints
33:41 - Wrap up and outro
_________________________________________________
About Jack Blade:
I am an avid gamer who loves all kinds of games but there is a special place in my heart for factory, logistics and management games. I want to share that love with the world and other fans of the genres!
Satisfactory itself holds a dear place in my heart and honestly I would say it can be held up next to Minecraft on the level of pure creativity you can unleash in this game. The factory and automation as well as the logistics elements of the game just takes it to the next level. On top of that the world is beautiful and the sound design is top tier!
___________________________________________
____________________________________________
Terminology (Dictionary)
- Logistic Systems:
Constructed mechanics that facilitate transfer and organization between different Factories, Production Lines, Faucets, Storage and Sinks
-Factory:
A collection of Faucets, Sinks, Storage and Production lines interconnected with Logistics Systems that produces one or more specific end products
- (Mechanical) Translation:
Communications between different logistics systems
- Megafactory: Single massive central factory for insane amounts of production output
- Modular Factory: Multiple smaller factories with single or just a few final outputs
- Production Line: A single parts production setup within a Factory
- Logistics Layers: Different methods of resource transfer that needs mechanical translation to interact
- Logistics Hierarchy: A method of planning, sorting and thinking about logistics system construction
- Sushi Belts: Single belts with multiple different resources on
- Overflow Protection: Systems using Sinks or Translation to other Production Lines and Factories to avoid production lines stopping because of lack of Storage
- Faucet: A system that inputs resources into the game, mining nodes, spawning mobs and generating power are examples
- Sink: A system that deletes, eats up or compresses resources to reduce space usage or entirely remove them from the game, AWESOME Sinks, power usage and advanced low quantity End Product production are examples
- Storage: Mechanical features in the game that stores or buffers resources in the game. Some examples are machines internal buffers, containers, vehicles and belts
- Buildable: Any single part you place down using the multitool/build gun
- End Product: The intended part or parts produced by a Factory
- Load Balancing: Predetermining flow rates for multiple belts
- Belt Priority: Predetermining priority order of belts
- Splitter: Buildable that splits one belt into 2 or 3, has advanced variants, smart and programmable splitters
- Merger: Buildable that can merge 2 or 3 belts onto 1
- Logic: Connected buildables, logistics and game mechanics that create an automated function
- Manifold: A line of splitters or mergers that feed machines or merge outputs
- Logistics Bus: A line of relevant Logistics Layers to move resources, are sorted into hierarchies
- Buffer: Container that stores extra resources before or after other buildables, logistics systems or production lines
- Logistics Floor: A floor separate from where production machines are placed, where logistics systems are built
- Wireframing: Minimal effort outline building for purposes of aligning and visualizing the finished build
- Machine Group: a set of machines, multiple machine groups make up one production line
Комментарии