filmov
tv
Conical Slicing: A different angle of 3D printing
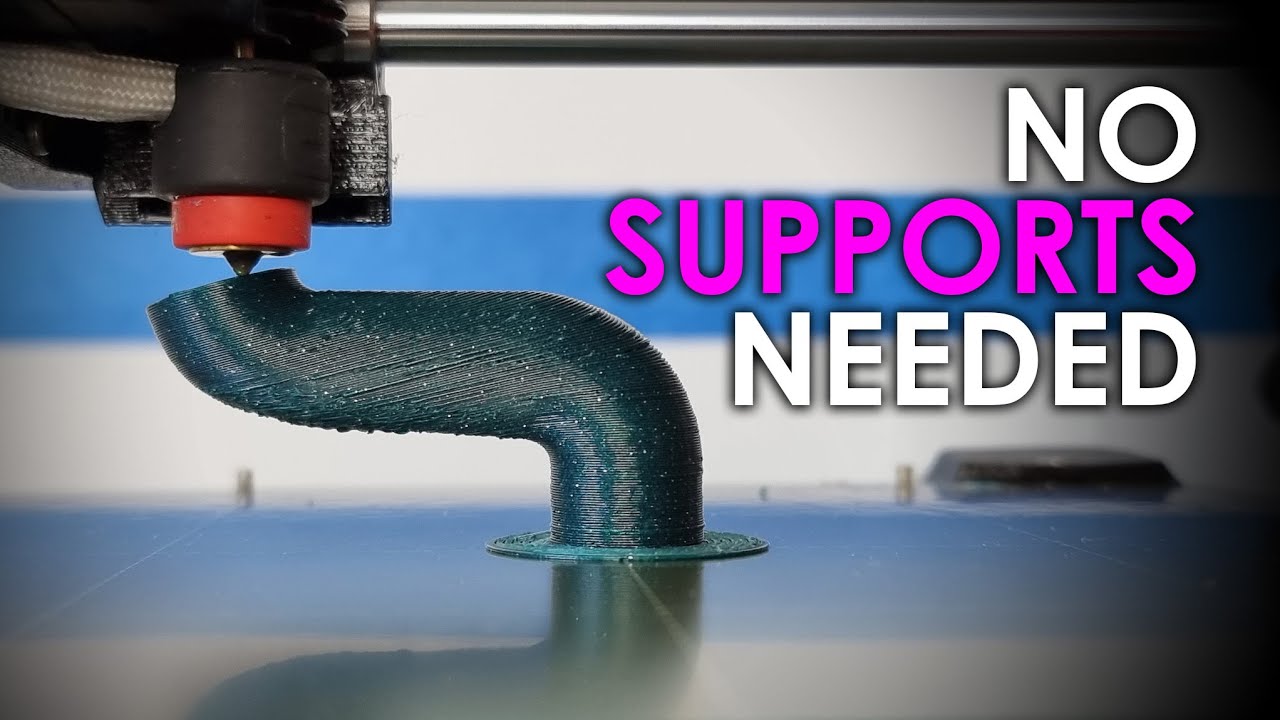
Показать описание
Current 3D printing slicers are dumb and only generate G-Codes on a 2-dimensional plane. We are leaving a ton of potential on the table because 3D printers are easily capable of complex 3-dimensional moves, yet we don’t have any software to take advantage of it. This video shows the Conical Slicing approach to create Non-Planar G-Code that allows printing supportless overhangs!
💚 Support me 💚
Join as a YouTube member!
📚 Further information:
⚙ My gear:
🎥 CAMERAS & LENSES
🎙AUDIO
🔴 LIVE STREAMING
Chapters
00:00 Introduction
02:10 Non-planar
04:15 Nozzle Clearance
05:54 Conical Slicing
08:52 Challenges
12:42 Sponsor Section
#3Dprinting #conicalSlicing #NonPlanar
DISCLAIMER: Part of this video was sponsored by Squarespace.
FTC Disclaimer: A percentage of sales is made through Affiliate links
💚 Support me 💚
Join as a YouTube member!
📚 Further information:
⚙ My gear:
🎥 CAMERAS & LENSES
🎙AUDIO
🔴 LIVE STREAMING
Chapters
00:00 Introduction
02:10 Non-planar
04:15 Nozzle Clearance
05:54 Conical Slicing
08:52 Challenges
12:42 Sponsor Section
#3Dprinting #conicalSlicing #NonPlanar
DISCLAIMER: Part of this video was sponsored by Squarespace.
FTC Disclaimer: A percentage of sales is made through Affiliate links
Conical Slicing: A different angle of 3D printing
Arc Overhangs make Supports Obsolete!
10 Secret 3D Printing Tricks Only Experts Know...
5 must-know 3D printing tips & tricks. (stronger and better looking prints)
Why slicing a cone gives an ellipse (beautiful proof)
Impressive 4-Axis Non-Planar 3D Printing
Non coplanar slicing over 3d curve
3d printing toolpaths with AiSync non planar slicing software
Ellipse geometry: external point, tangent lines, points of contact, normals, chord of contact | 1
Stop 3d printing so slow!!! 🤯 (how to print faster)
Non-Planar 3D printing
90° No Support Print with Conical Slicing?! CNC Kitchen's Early Chrimbo Gift for us All!!
Stop Using Brims, Do This Instead
printed WITHOUT support #shorts
5-axis Slicing vs. 3-axis Slicing
SOLVING 3D PRINTING CHALLENGES WITH ADAPTIVE SURFACE SLICING
Simple 5-axis slicing with GUI in Grasshopper
NON-PLANAR 3D Printing by BENDING G-Code
HYDRAULIC PRESS VS STRONGEST HUMAN BONES 🤯 WHO WILL WIN 💥 #shorts #usa #shortfeed
Mixing Planar & Non-Planar Slicing Methods for 3D Printing Overhangs without Support Structure
Mistakenly Grabbing Molten Glass (For safety/hazard education, don’t try!) #shorts
You can build this 5-axis Prusa conversion: The Open5X! #ERRF2022
What’s new in NX2206 Additive Manufacturing New cone slicing method for parts with varying slope
Creality Ender 3 V2 - Simple Tips for Super Clean 3D Prints
Комментарии