filmov
tv
Just A 'SIMPLE' Repair
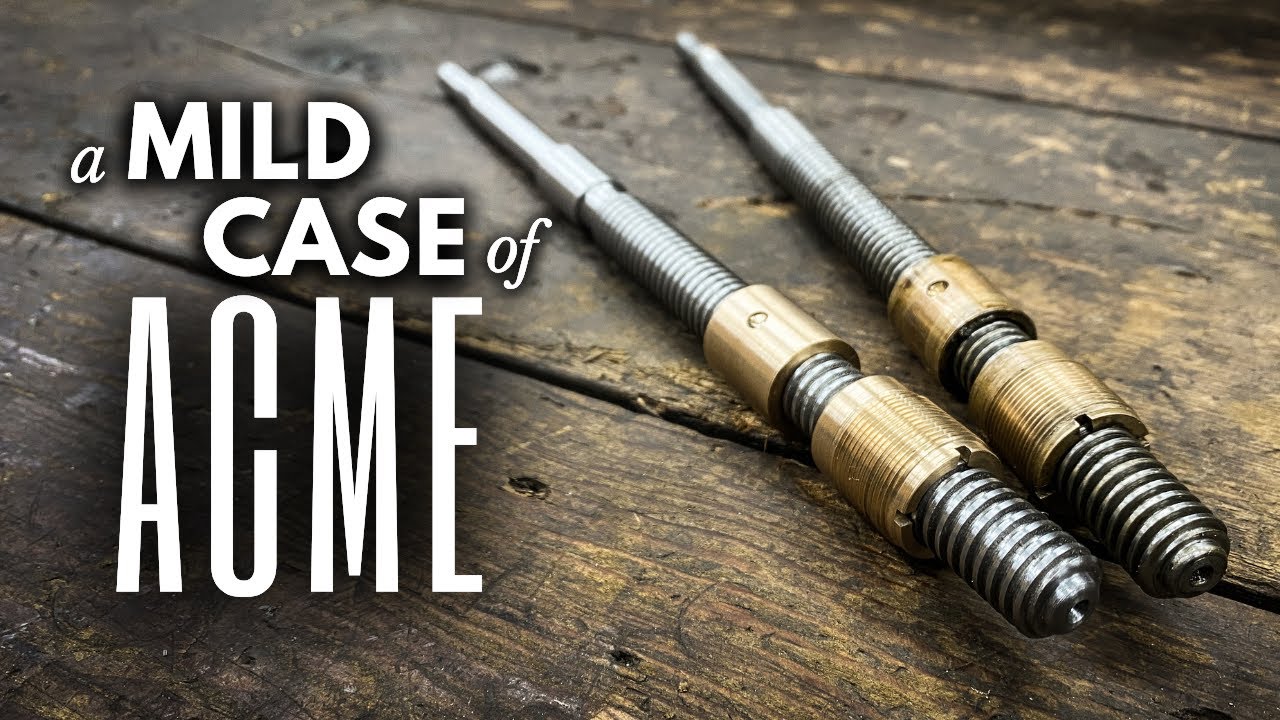
Показать описание
This video is sponsored by Shapr3D.
Ignoring the larger issues with the "new" lathe in favor of a simple project. Remaking the lead screw and nuts for the compound slide. Little did I know simple... does not mean easy...
#inheritancemachining #machineshop #hobbymachinist
Thank you again to the Micrometer level Patreon members listed at the end of the video!
TIMESTAMPS
0:00 Spoiler Alert
1:20 Le Probleme
3:30 Civility
5:29 A Worthy Investment
7:39A before B (but also C and D)
11:07 Trigonom-ish
13:08 Two Firsts
16:48 A Milling Problem But a Center Ain't One
18:27 Brrrr
20:00 Killing Time...
21:31 Climax
24:18 MOAR THREADS
26:39 Bringing It All Together
FAQ
Editing: Final Cut Pro X
Intro Song: Way Back Way Back When (Instrumental Version) - Gamma Skies
© 2023 Inheritance Machining, LLC. All Rights Reserved.
Just A 'SIMPLE' Repair
The Pump Repairman Taught Me This Simple Trick! Plumbing Repair Made Simple
repair ANY earphones DIY
This repair made my neighbor jealous!🔥 #emotional #waygo #FixItRight #FeelGoodFix #shorts
Shattered Tablet Fix #lifehacks
Easiest Repair Ever..? #Shorts
I fixed your slime
10 stitches you need to know - how to start a stitch #sewing #handstitch #sewingforbeginners
How to repair Kitcehn lighter. Not Clicking? No Spark? Only rs10
Fixing a fractured finger (3D Animation)
EASY Life Hack to Fix Your Charger #Shorts
How To Fix Your Knock Knees From Home… Grab a Pillow! #knockknees #kneepain #walking
Quick & Easy Sonicare ToothBrush Disassembly Hack #DIY #LifeHacks #Sonicare #repair #broken
How To Make 2 Ingredients Slime At Home, Satisfied Crush Edition
Diy fix for DEEP scratches
GENIUS Mop Fix in 1 Minute! Plastic Bottle Hack That Actually Works!
Viral Mascara Hack?! Is it worth it 😱 #makeup #mascara #makeuphacks
Repair Your Damaged Skin Barrier in JUST 5 Days! 🔥#skincare #glowup2025 #acnefree
Fix hole in wall in 60 seconds
Amazing Shoe Repair Process in Just Seconds
Thresher Pulley Thread Repair | Save Money with This Simple Fix! Complete Tutorial for Beginners
How To Change Your Yoyo From 'Responsive' to 'Unresponsive'
Simple car repair series - cleaning the crankshaft forced ventilation valve#tips #cars#car#carskills
Nail Tips💅 The Builder gel on nail tips #melodysusie #buildergel #gel #gelnails #nailtutorial...
Комментарии