filmov
tv
Aluminum MIG vs TIG Welding
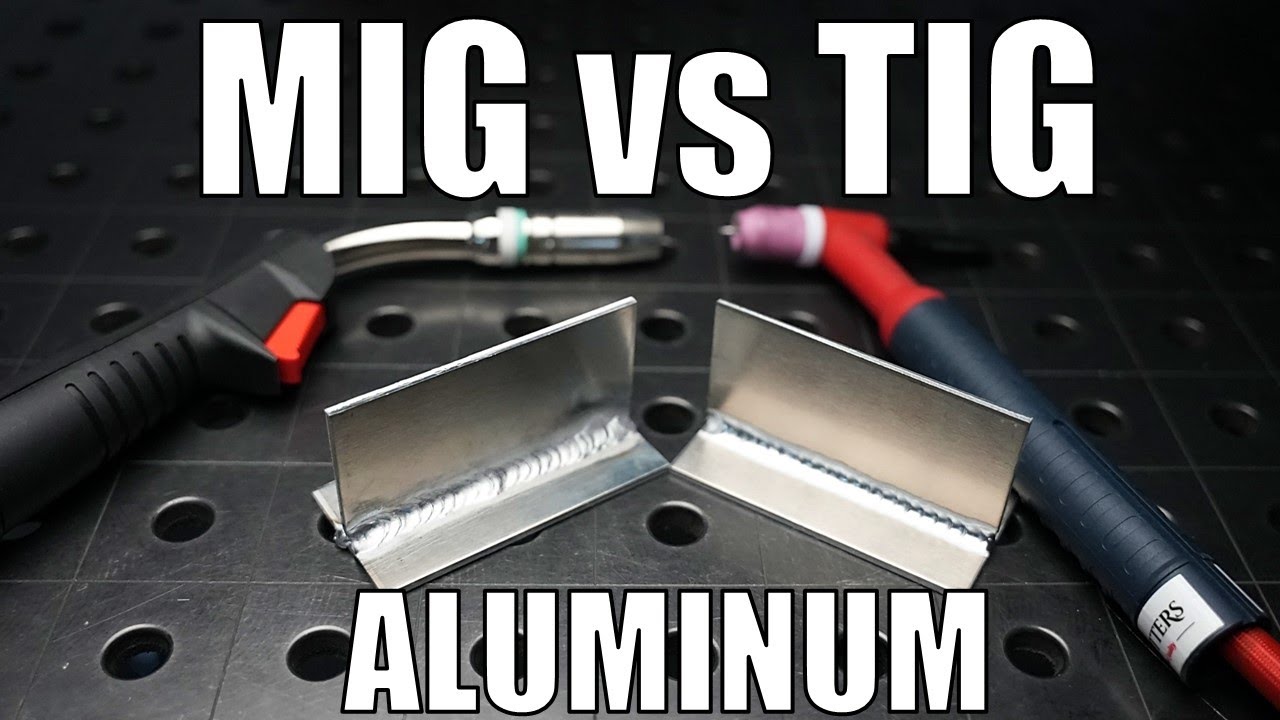
Показать описание
Let's explore the 2 most common processes for welding aluminum
👨🏭 Learn to Weld In My $39 Online Courses 👨🏭
🧰 Tools Used In This Video 🧰
-For MIG & TIG - Revolution 2500
-For MIG - ProPulse 220
-For TIG - Invertig 221
📖 Chapters 📖
0:00 Welcome
0:23 MIG Welding Aluminum
6:17 Welding Machine
6:40 TIG Welding Aluminum
9:36 Summary
🙏Thanks for Watching!🙏
Gas Metal Arc Welding (GMAW) and Gas Tungsten Arc Welding (GTAW) are both great processes for welding aluminum. Watch this to find out which welding process is better for your project.
👨🏭 Learn to Weld In My $39 Online Courses 👨🏭
🧰 Tools Used In This Video 🧰
-For MIG & TIG - Revolution 2500
-For MIG - ProPulse 220
-For TIG - Invertig 221
📖 Chapters 📖
0:00 Welcome
0:23 MIG Welding Aluminum
6:17 Welding Machine
6:40 TIG Welding Aluminum
9:36 Summary
🙏Thanks for Watching!🙏
Gas Metal Arc Welding (GMAW) and Gas Tungsten Arc Welding (GTAW) are both great processes for welding aluminum. Watch this to find out which welding process is better for your project.
Aluminum MIG vs TIG Welding
Alumiweld vs Aluminum Weld: Was My TIG Welder a Waste of Money?
MIG VS TIG Welding With Aluminum
MIG vs. TIG vs. STICK Welding
Welding Aluminum TIG vs MIG Spool Gun.(OEM,ODM)
Weld Aluminum with ANY MIG Welder
TIG Welding Aluminum W/ Harbor Freight Titanium 200
Welding Aluminum TIG vs MIG Spool Gun
Electric Welding Machine #Technology#Engineering# #automobile#automotivetools #tools#powertools
get the BEST ARC CONTROL tig welding aluminum (here's how) how to tig weld aluminum
How To MIG Weld Aluminum - Pointers and Troubleshooting with Eastwood
Aluminum Welding Rods
I think the Amazon Welder is better😳
best harbor freight TIG welder #welding #work #metal
PrimeWeld MIG180 SPOOL GUN Aluminum
TIG vs MIG Welding for Hobbyists: Which Type of Welding is Best?
OptX™ Laser Comparison to TIG and MIG
Should I buy an expensive tig welding machine? (WATCH THIS FIRST!)
$70 vs $2,300 Welder? Let's Settle This! Weld Strength, Duty Cycle, Current Output, Build Quali...
$200 TIG Welder VS $2,000 TIG Welder
Guide to MultiProcess Welders: Harbor Freight vs Vevor vs ArcCaptain vs Lincoln!
Stick vs Flux Cored Welding for Hobbyists: Which type of welding is better for you?
Lift TIG Welding - YesWelder FIRSTESS™ MP200 5-in-1 Welder & Cutter
aluminium welding tigtechniques.How to 'Weld' Aluminum forBeginners
Комментарии