filmov
tv
Mig Welding Thin Square Tubing
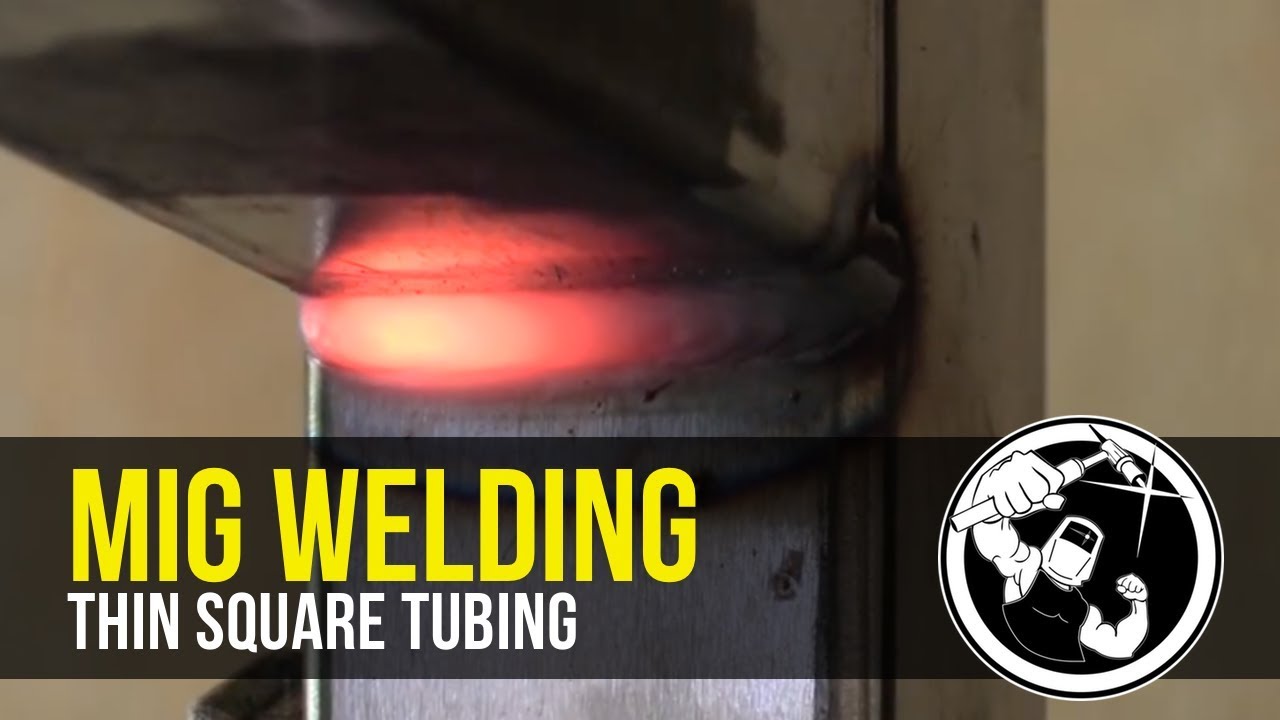
Показать описание
Subscribe to my channel for more weekly videos.
Follow Welding Tips & Tricks on social media to see what I’m up to:
Join the discussion with thousands of welders at the Welding Tips & Tricks forum
In this video I used the Lincoln Powermig 210mp along with .025" er70s-6 wire.
The recommended settings for 16 ga were 17 volts and 240ipm but I went a bit hotter with 18 volts and 305 ipm.
Follow Welding Tips & Tricks on social media to see what I’m up to:
Join the discussion with thousands of welders at the Welding Tips & Tricks forum
In this video I used the Lincoln Powermig 210mp along with .025" er70s-6 wire.
The recommended settings for 16 ga were 17 volts and 240ipm but I went a bit hotter with 18 volts and 305 ipm.
MIG Weld Thin Square Tubing: 5 Tips to Crush It!
Mig Welding Thin Square Tubing
Learn to (Mig Weld) in A DAY pt. 3 (MIG Welding Thin Square Tubing)
Mig Welding 45° Square Tubing
#tack #weld on thin square tube with large gap and common mistakes in #mig #gmaw #welding #welder
not everyone knows how to weld thin square tube #sorts #welding
Stick welding square tubing : 3 thin metal welding tricks
Tack Tack Tack Welding and Sq. Tubing Tips & Tricks
The Secret to Perfect thin Square tube to pipe welding.,,
Mig Welding GMAW Steel Box Tube. Straight line splice weld. Penetration cut & reveal
the secret technique of welding thin square tubes that few people know | stick welding square tube
Mig welding square tube #sorts #welding #construction
Stick Weld Thin Square Tubing
Weld Sequencing- Keep Your Projects From Warping
Gasless Fluxcore Welding thin square tubing for beginners
two tricks of welding thin square tubes that few people know about
🔥 Stick Welding Square Tube
how welders patch large holes in thin metal | stick welding square tubing #howtowelding #welding
MIG Welding Thin Metal to Thick Metal: Here's How
Welding Square Tubing to 4' Pipe | Essential Layout Tricks | No Grinding | Welding a Double Gat...
how to cut square pipe, how to weld thin
secret trick stick welding , why no welders talk about this
Stick Welding Thin Tubing *How Not to Burn Through
Stick welding thin square tubing ( T-joint)
Комментарии