filmov
tv
The Why and How to Remove Static Electricity & Electrostatic Discharge (ESD) Part 1!
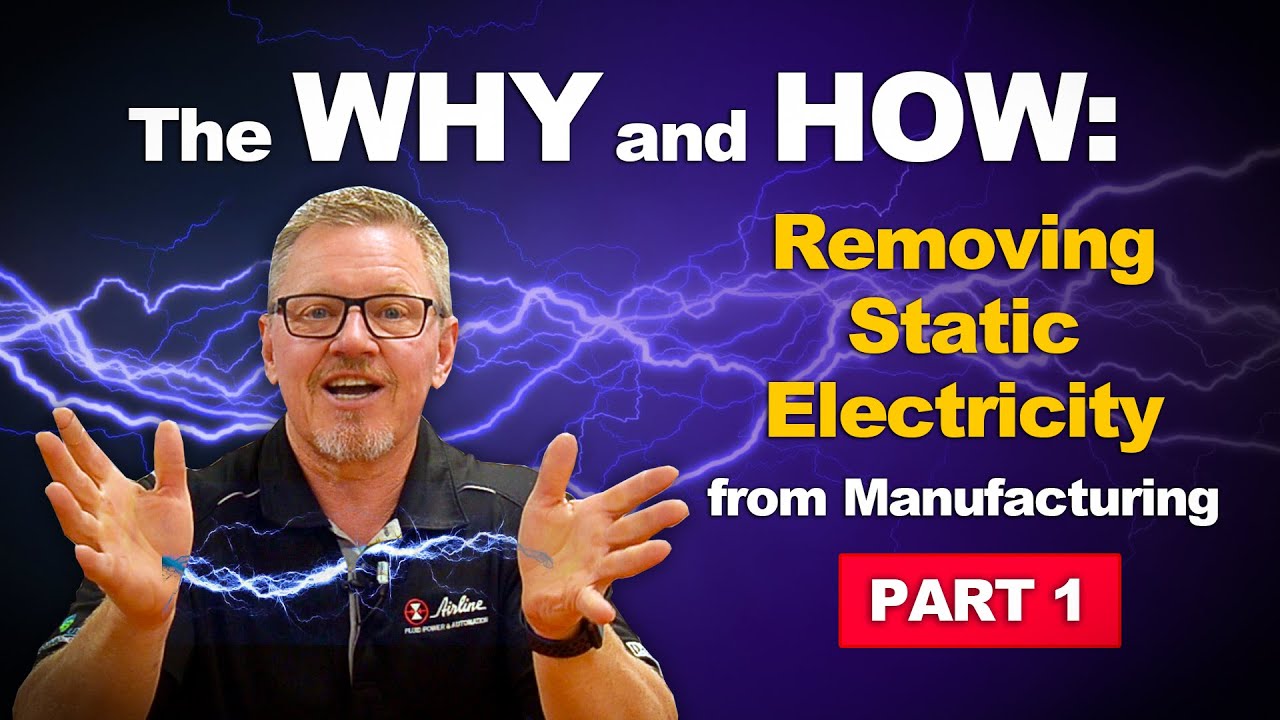
Показать описание
Electrostatic Discharge (ESD), is a static electricity issue that can make any manufacturer’s hair stand on end. Luckily, ESD can be eliminated by understanding its cause, recognizing its symptoms, and implementing best practices and anti-static technologies. Learn more by watching this two-part series, where we’ll explain the WHY and HOW behind ESD: Why it occurs, why it is a problem, and how to solve the problem.
Electrostatic Discharge (ESD) is what we recognize as the “zap” or spark we experience with static electricity. This spark may seem small, but a single spark can generate up to 3,000 volts of electricity! The results of this electrical charge can range from creating minor nuisances in your machine line to costly (and potentially deadly) repercussions, including latent damage to products, product contamination and even explosions. Unfortunately, issues with ESD become worse in the fall and winter, because static charge is more likely to build up when the air is dry.
As products and mechanisms move through the manufacturing line, this movement creates friction, which is the cause of static electricity and ESD. These electrically charged items can wreak havoc in the manufacturing line, as they can attract or repel other objects through the system. In some instances, the product will become adhesive to surfaces, sometimes becoming stuck at various points throughout the process. In other instances, the product may move away from objects down the line. As you can imagine, this can cause serious problems on the production floor when products are going through various stages from assembly to packaging.
Not only can it hold up your manufacturing process, but it can also damage, or even destroy your products. ESD is often unpredictable in its speed and amount of discharge, but it’s not uncommon for a spark to create enough volts to melt the device’s current-carrying elements. For example, one zap of ESD can change the circuit from a semi-conductor to an always-conductor, which usually results in a spark and a bad smell when powered on. Manufacturers of semi-conductors and other electronic devices can see lower yields and loss of revenue due to ESD. Quality issues can also arise, as malfunctions from ESD sometimes don’t surface until days or weeks later, after testing has already been completed.
Another issue static brings is the attraction of unwanted particles, like dust, dirt, pollen and bacteria. Ionized products attract electrons that carry unwanted particles, covering the product in dust and dirt. This creates quality issues for the final product and depending on the application, potential health hazards for the end-user.
Static has also become more of an issue with increased production pressures. As manufacturers increase their production rate and reduce material costs by switching to synthetic materials, they create the perfect environment for static electricity. Although most materials can generate a positive or negative charge, synthetic materials are more likely to retain charges because they have low conductivity, so their charge is less likely to dissipate. Surprisingly, air actually has the potential to be highly positive in charge, meaning they have a tendency to give away electrons. Other positively-charged materials include glass, Lexan, nylon, wool, lead, aluminum and paper. Negatively charged materials include hard rubber, polyester, silicone, vinyl, metals like gold, silver, nickel, platinum and copper, polyester, plastic wrap, polyethylene, which is the material of scotch tape, silicon, Teflon, certain types of foam, and more. All of these materials have a tendency to readily attract electrons.
Stay tuned to part two, where we’ll learn how to remove static discharge from your manufacturing line. Hit that subscribe button and bell icon so you don’t miss it!
AND follow us on social media!
ABOUT US:
Electrostatic Discharge (ESD) is what we recognize as the “zap” or spark we experience with static electricity. This spark may seem small, but a single spark can generate up to 3,000 volts of electricity! The results of this electrical charge can range from creating minor nuisances in your machine line to costly (and potentially deadly) repercussions, including latent damage to products, product contamination and even explosions. Unfortunately, issues with ESD become worse in the fall and winter, because static charge is more likely to build up when the air is dry.
As products and mechanisms move through the manufacturing line, this movement creates friction, which is the cause of static electricity and ESD. These electrically charged items can wreak havoc in the manufacturing line, as they can attract or repel other objects through the system. In some instances, the product will become adhesive to surfaces, sometimes becoming stuck at various points throughout the process. In other instances, the product may move away from objects down the line. As you can imagine, this can cause serious problems on the production floor when products are going through various stages from assembly to packaging.
Not only can it hold up your manufacturing process, but it can also damage, or even destroy your products. ESD is often unpredictable in its speed and amount of discharge, but it’s not uncommon for a spark to create enough volts to melt the device’s current-carrying elements. For example, one zap of ESD can change the circuit from a semi-conductor to an always-conductor, which usually results in a spark and a bad smell when powered on. Manufacturers of semi-conductors and other electronic devices can see lower yields and loss of revenue due to ESD. Quality issues can also arise, as malfunctions from ESD sometimes don’t surface until days or weeks later, after testing has already been completed.
Another issue static brings is the attraction of unwanted particles, like dust, dirt, pollen and bacteria. Ionized products attract electrons that carry unwanted particles, covering the product in dust and dirt. This creates quality issues for the final product and depending on the application, potential health hazards for the end-user.
Static has also become more of an issue with increased production pressures. As manufacturers increase their production rate and reduce material costs by switching to synthetic materials, they create the perfect environment for static electricity. Although most materials can generate a positive or negative charge, synthetic materials are more likely to retain charges because they have low conductivity, so their charge is less likely to dissipate. Surprisingly, air actually has the potential to be highly positive in charge, meaning they have a tendency to give away electrons. Other positively-charged materials include glass, Lexan, nylon, wool, lead, aluminum and paper. Negatively charged materials include hard rubber, polyester, silicone, vinyl, metals like gold, silver, nickel, platinum and copper, polyester, plastic wrap, polyethylene, which is the material of scotch tape, silicon, Teflon, certain types of foam, and more. All of these materials have a tendency to readily attract electrons.
Stay tuned to part two, where we’ll learn how to remove static discharge from your manufacturing line. Hit that subscribe button and bell icon so you don’t miss it!
AND follow us on social media!
ABOUT US:
Комментарии