filmov
tv
Toyota CEO REVEALS Why Tesla Giga Casting Machines
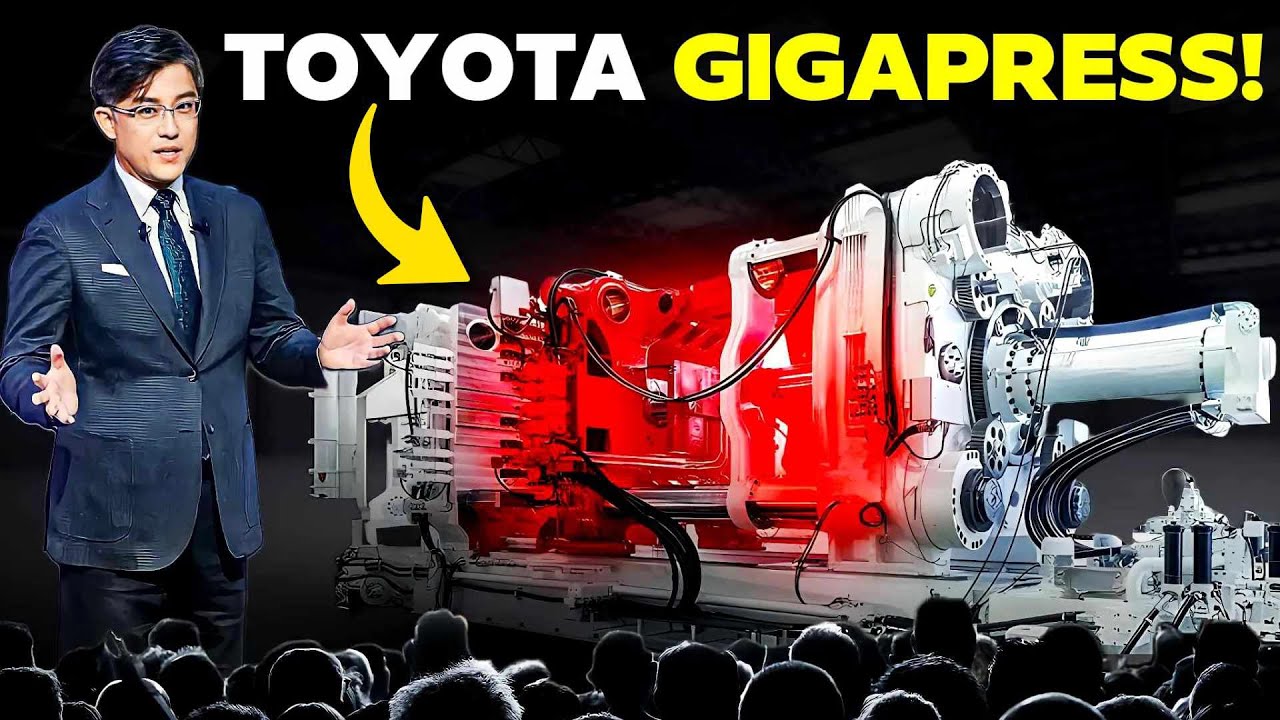
Показать описание
Toyota CEO REVEALS Why Tesla Giga Casting Machines
Toyota Motor announced this week that it will use a Tesla-pioneered technology called "gigacasting" as part of a plan to increase the efficiency and decrease the cost of future electric vehicles (EVs).
Toyota is not the only company imitating Tesla's innovation. But what’s the reason for this new trend?
A new fashion trend has recently begun to gain traction. The giga-casting trend was started by Tesla and is also known as "mega-castings" by some OEMs. These massive cast structural elements can combine a variety of parts into a single, extremely large casting. This may affect not only how cars are made and how aluminum is used generally, but it may also change how much castings, sheets, and extrusions are used in light vehicles. To put it another way, it might promote new growth for castings while possibly inhibiting the growth of sheets and extrusions.
Tesla has incorporated the gigapress aluminum die-casting machine in its US, Chinese, and German factories. The home-sized machines can create aluminum components that are much larger than anything previously used in the production of vehicles.
The word "giga" in the name is a reference to Tesla's practice of referring to its factories as "gigafactories". They are now referred to as "megapresses" by other automakers, a term that can also be used to describe smaller but still enormous machines.
When the press is in use, it feeds an 80 kg or more shot of molten aluminum into a mold where it is shaped into a part, released, and then quickly cooled.
Tesla has created an aluminum alloy that also enables it to forego the standard heat-treating procedure used to boost the strength of the cast component.
Numerous studies, particularly those from Ducker-Carlisle, have demonstrated that the amount of aluminum used in light vehicles has been rising steadily over the years, surpassing 500 lbs (227 kg) per light vehicle in North America and 396 lbs (180 kg) per vehicle in Europe. Castings have traditionally been the most common product form, but sheet and extrusion applications have seen the fastest growth rates in recent years and will continue to do so in the future. The primary motivation for using aluminum has always been lightness.
The trend of aluminum's growth has only been sustained by the quickening electrification of vehicles, which has also altered the product mix. While hybrid vehicles typically have smaller engines and battery electric vehicles (BEVs) don't use internal combustion engines (ICEs), castings have historically been the most common product form and have primarily been used in the powertrain of ICE vehicles (primarily using secondary A380 or 319 alloys). The growth of aluminum has now moved to the car body and chassis, as well as the battery trays and electric drive components for electric vehicles. Today, the majority of these components are made from sheet and extruded materials, with only a small portion from castings, which are frequently structural and are therefore made using more advanced techniques and cleaner aluminum alloys (either primarily from clean scrap or secondary).
this time, numerous other automakers have made the decision to take the same route and have invested in giga-presses, including Volvo and its EV brand Polestar. Volvo plans to create a number of vehicle models that can utilize the same mega-casting for their body-in-white (BIW) components. Even mounting points for parts like suspension arms and electric motors will be integrated into the castings.
Mercedes-Benz, Volkswagen, Toyota, General Motors, Hyundai, and the Chinese electric vehicle start-ups Nio and Xpeng are other notable automakers that are openly known to be following this trend (or plan to)5.
--------------------------------------
Check this out:
Toyota CEO Just Had Enough Of BEVs!
Toyota CEO Just ANNOUNCED A New Electric Motor That Will SHOCK The EV World!
Toyota's C-HR 2023 Shocked Everyone With It's Features
Here's Why Toyota's RAV4 2023 Will Shock Everyone
--------------------------------------
#toyota #toyotabz4x #toyotagigapress #toyota4runner #toyotarav4 #toyotatacoma #toyotabattery #2024tacoma
⚠️ Copyright Disclaimers
• Section 107 of the U.S. Copyright Act states: "Notwithstanding the provisions of sections 106 and 106A, the fair use of a copyrighted work, including such use by reproduction in copies or phonorecords or by any other means specified by that section, for purposes such as criticism, comment, news reporting, teaching (including multiple copies for classroom use), scholarship, or research, is not an infringement of copyright."
• We use images and content in accordance with the YouTube Fair Use copyright guidelines
Toyota Motor announced this week that it will use a Tesla-pioneered technology called "gigacasting" as part of a plan to increase the efficiency and decrease the cost of future electric vehicles (EVs).
Toyota is not the only company imitating Tesla's innovation. But what’s the reason for this new trend?
A new fashion trend has recently begun to gain traction. The giga-casting trend was started by Tesla and is also known as "mega-castings" by some OEMs. These massive cast structural elements can combine a variety of parts into a single, extremely large casting. This may affect not only how cars are made and how aluminum is used generally, but it may also change how much castings, sheets, and extrusions are used in light vehicles. To put it another way, it might promote new growth for castings while possibly inhibiting the growth of sheets and extrusions.
Tesla has incorporated the gigapress aluminum die-casting machine in its US, Chinese, and German factories. The home-sized machines can create aluminum components that are much larger than anything previously used in the production of vehicles.
The word "giga" in the name is a reference to Tesla's practice of referring to its factories as "gigafactories". They are now referred to as "megapresses" by other automakers, a term that can also be used to describe smaller but still enormous machines.
When the press is in use, it feeds an 80 kg or more shot of molten aluminum into a mold where it is shaped into a part, released, and then quickly cooled.
Tesla has created an aluminum alloy that also enables it to forego the standard heat-treating procedure used to boost the strength of the cast component.
Numerous studies, particularly those from Ducker-Carlisle, have demonstrated that the amount of aluminum used in light vehicles has been rising steadily over the years, surpassing 500 lbs (227 kg) per light vehicle in North America and 396 lbs (180 kg) per vehicle in Europe. Castings have traditionally been the most common product form, but sheet and extrusion applications have seen the fastest growth rates in recent years and will continue to do so in the future. The primary motivation for using aluminum has always been lightness.
The trend of aluminum's growth has only been sustained by the quickening electrification of vehicles, which has also altered the product mix. While hybrid vehicles typically have smaller engines and battery electric vehicles (BEVs) don't use internal combustion engines (ICEs), castings have historically been the most common product form and have primarily been used in the powertrain of ICE vehicles (primarily using secondary A380 or 319 alloys). The growth of aluminum has now moved to the car body and chassis, as well as the battery trays and electric drive components for electric vehicles. Today, the majority of these components are made from sheet and extruded materials, with only a small portion from castings, which are frequently structural and are therefore made using more advanced techniques and cleaner aluminum alloys (either primarily from clean scrap or secondary).
this time, numerous other automakers have made the decision to take the same route and have invested in giga-presses, including Volvo and its EV brand Polestar. Volvo plans to create a number of vehicle models that can utilize the same mega-casting for their body-in-white (BIW) components. Even mounting points for parts like suspension arms and electric motors will be integrated into the castings.
Mercedes-Benz, Volkswagen, Toyota, General Motors, Hyundai, and the Chinese electric vehicle start-ups Nio and Xpeng are other notable automakers that are openly known to be following this trend (or plan to)5.
--------------------------------------
Check this out:
Toyota CEO Just Had Enough Of BEVs!
Toyota CEO Just ANNOUNCED A New Electric Motor That Will SHOCK The EV World!
Toyota's C-HR 2023 Shocked Everyone With It's Features
Here's Why Toyota's RAV4 2023 Will Shock Everyone
--------------------------------------
#toyota #toyotabz4x #toyotagigapress #toyota4runner #toyotarav4 #toyotatacoma #toyotabattery #2024tacoma
⚠️ Copyright Disclaimers
• Section 107 of the U.S. Copyright Act states: "Notwithstanding the provisions of sections 106 and 106A, the fair use of a copyrighted work, including such use by reproduction in copies or phonorecords or by any other means specified by that section, for purposes such as criticism, comment, news reporting, teaching (including multiple copies for classroom use), scholarship, or research, is not an infringement of copyright."
• We use images and content in accordance with the YouTube Fair Use copyright guidelines
Комментарии