filmov
tv
Exposing OceanGate Submarines Many Fatal Designs
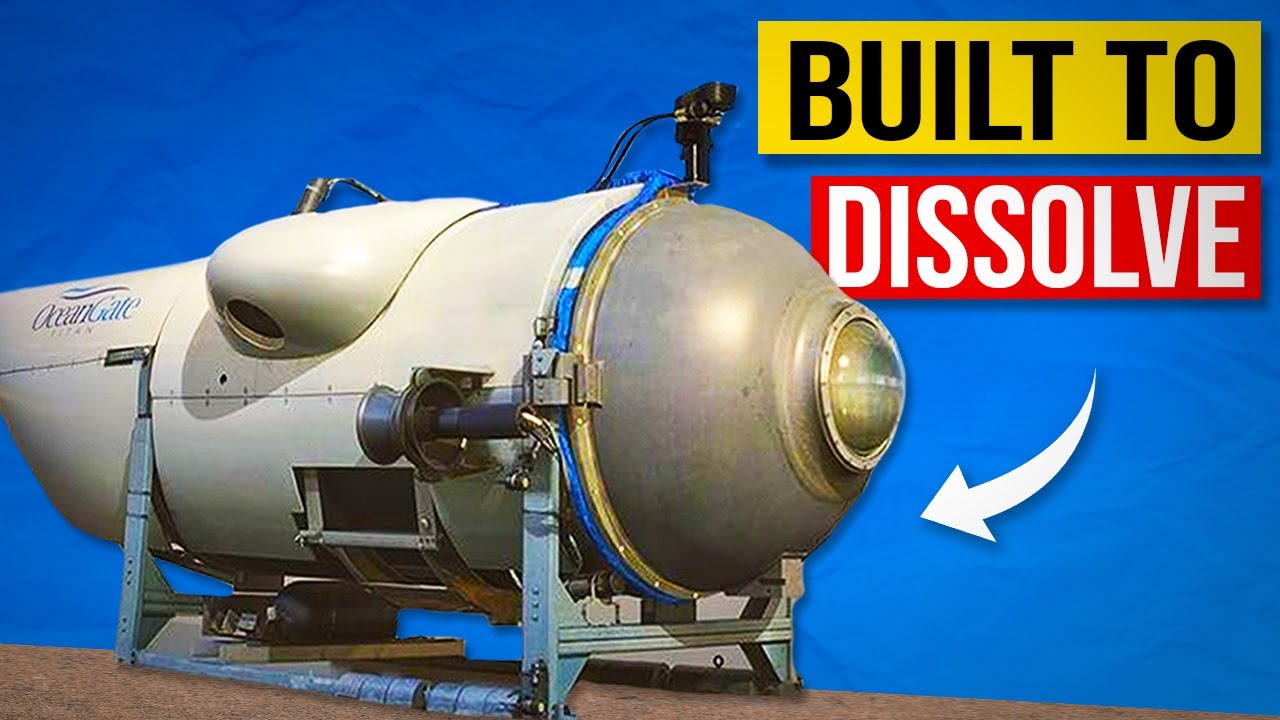
Показать описание
The recent coverage of the Titan submersible has spoken a lot about the possible ways the vessel could have failed, but how did it actually work?
This video explores many of the systems onboard, from the controls and communications systems, to the propulsion and safety. Will deep sea exploration continue to be a tourist location? Or will this change the direction of the sector? Either way, I hope you learn something from this video!
Due to it being very late in the UK as I upload, I will sort the references more neatly tomorrow!
Sources:
#OceanGate #Titan #Explained
This video explores many of the systems onboard, from the controls and communications systems, to the propulsion and safety. Will deep sea exploration continue to be a tourist location? Or will this change the direction of the sector? Either way, I hope you learn something from this video!
Due to it being very late in the UK as I upload, I will sort the references more neatly tomorrow!
Sources:
#OceanGate #Titan #Explained
Exposing OceanGate Submarines Many Fatal Designs
Fatal Flaws: The OceanGate Story | Full Documentary (2024)
Exposing OceanGate Submarines Many Fatal Designs | Khoj The World
The Red Flags Missed in the Tragic OceanGate Case, Ex-Employee Exposes CEO
MrBeast was invited on the Oceangate Submarine that drowned 😱
The Questionable Engineering of Oceangate
Woman whose son and husband died on OceanGate submersible speaks out #shorts
Watch What Happened To The BODİES At İMPLOSİON Of TİTAN Submersible (Titanic Expedition)
The Dark Truth About OceanGate (Documentary)
US Navy Just Reveals Titan's TERRIFYING Last Moments | Oceangate Submarine Documentary
Exposing OceanGate Submarines Many Fatal Designs subscribe my youtube chennal Mukesh all geming
#Titan Submersible Was Set Up To Fail
Former Oceangate employees detail issues with Titan submersible
The Fatal Design Flaws of The Titanic Submarine
What Deep Sea Implosions Do To A Body
The Untold Truth: Oceangate Submarine Disaster Exposed!
Former Director Exposes OceanGate's Profit-Driven Culture in Fatal Submersible Implosion
Inside The Oceangate's Titan Submarine Just Before It Went Missing #shorts #viral
Exposing the Fatal Flaws of the Oceangate Submarine
The Titan Tragedy: What Went Wrong with OceanGate's Mission?
Ocean Gate: The Search For The Truth (Full Documentary)
The Fatal Flaw of The Submersible #youtubeshorts #jamescameron #submarine #oceangate #titan
$250,000 To Use This Toilet? - Titan Submarine
What REALLY happened to OceanGate's Titan
Комментарии