filmov
tv
3D Printed Cycloidal Drive V2 - Much Better!
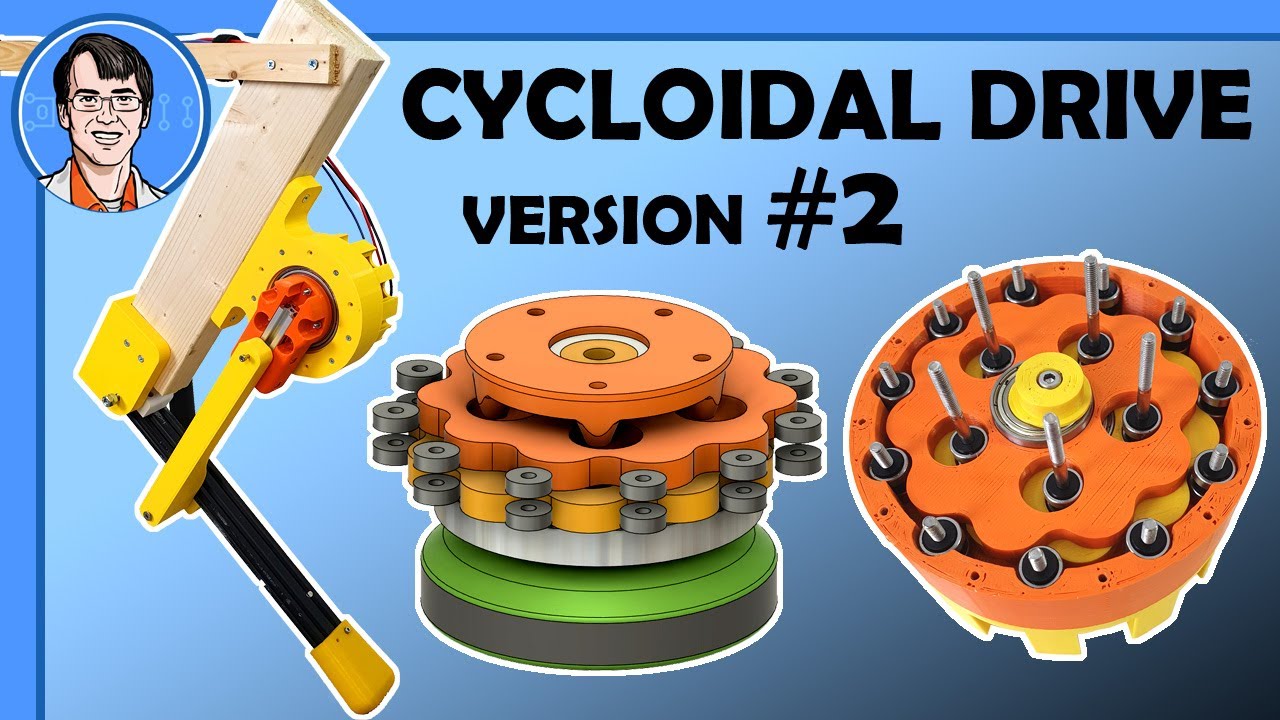
Показать описание
In my previous video I built a 3D Printed Cycloidal Drive which was relatively successful, although the cam snapped off under load and it vibrated a lot. This time I've balanced the drive by using two cycloidal discs 180' out of phase with each other. I've also made the cam shaft much thicker and robust by screwing an M4 bolt through the middle of it. This time it's much tougher, although we still need to do a lot of testing.
You can support me on Patreon or buy my Merchandise:
***************************
***************************
Affiliate links - I will get some money of you use them to sign up or buy something:
***************************
***************************
Other socials:
***************************
***************************
Huge thanks to my Patrons, without whom my standard of living would drastically decline. Like, inside out-Farm Foods bag decline. Plus a very special shoutout to Lulzbot, Inc who keep me in LulzBot 3D printers and support me via Patreon.
HARDWARE/SOFTWARE
Below you can also find a lot of the typical tools, equipment and supplies used in my projects:
XROBOTS
Former toy designer, current YouTube maker and general robotics, electrical and mechanical engineer, I’m a fan of doing it yourself and innovation by trial and error. My channel is where I share some of my useful and not-so-useful inventions, designs and maker advice. Iron Man is my go-to cosplay, and 3D printing can solve most issues - broken bolts, missing parts, world hunger, you name it.
XRobots is the community around my content where you can get in touch, share tips and advice, and more build FAQs, schematics and designs are also available.
Комментарии