filmov
tv
How I built the Simplest CNC Machine with minimum parts possible | DIY Laser Engraver
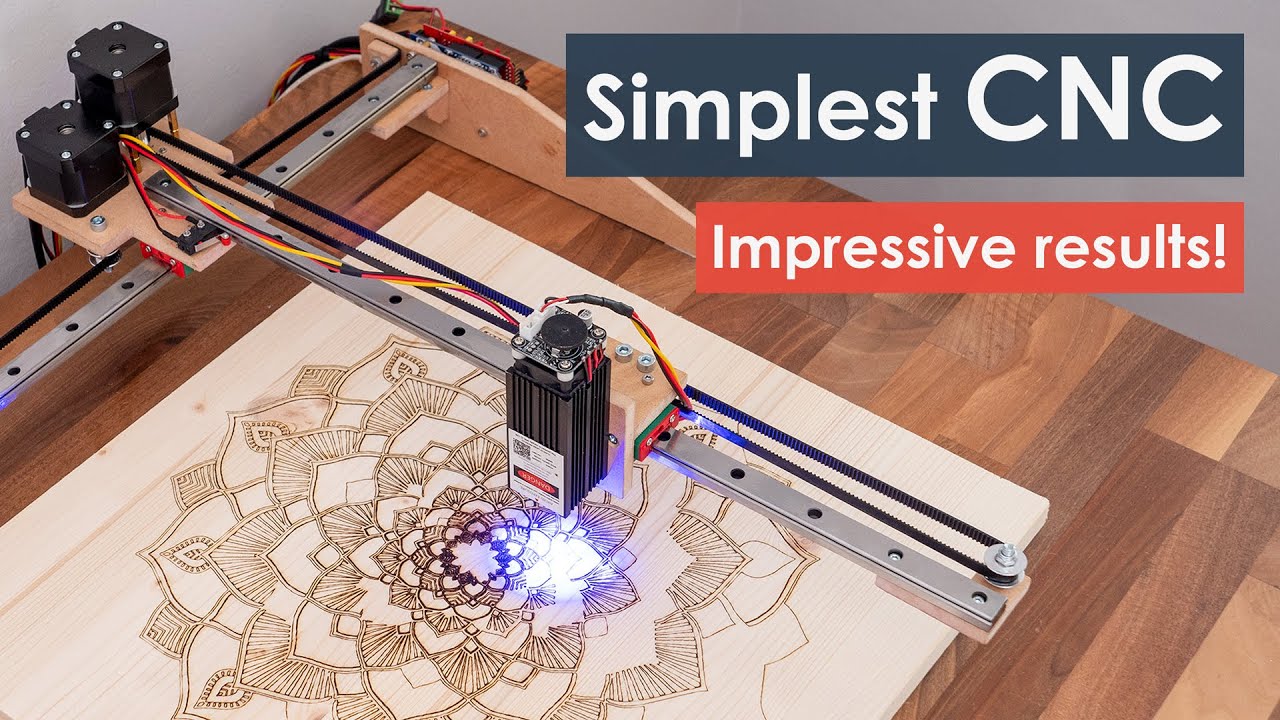
Показать описание
Parts list (check website article for full list, affiliate links):
AliExpress:
In this video I will show you how I built the simplest CNC machine with minimum parts possible and without using a 3D printer. That’s right. I’ve been using 3D printers for most of my recent projects because, of course, they are great for prototyping as we can easily make any shape we want with them. However, not everyone has a 3D printer, so therefore I wanted to show you that we can also make stuff even without the help of 3D printers or other CNC machines.
Like my page on Facebook:
How I built the Simplest CNC Machine with minimum parts possible | DIY Laser Engraver
How I built a simple RPG game to track my life and skills
Simple Off Grid Log Cabin Build: Easy Wall Construction (Butt And Pass)
How I built the Simplest Laser Engraver, DIY Laser Engraver
Complete build a simple house
Build a Simple Electric Motor | Science Project
How to build a simple 15 foot plywood boat in 2 days with Lou - Catskill Mountain Youtube Maker Camp
ad How I built a Easy DIY Privacy Screen using the @Wagner-Spraytech FLEXiO 3500 Paint Sprayer!
How I built easy DIY bespoke storage to match our kitchen
Simple off grid Cabin that anyone can build & afford
The EASIEST & FASTEST Way To DIY Build A Campervan (perfect for beginners)
How to build easy & stackable sawhorses
The Simplest DIY Go-Kart Build
1419 The Easiest Engine You Will Ever Build - The Fluidyne
How to Build a Super Simple RC Airplane for Beginners
Easy-Build SURVIVAL SHELTER | Bushcraft Day Project | Debris Emergency Fort in the Woods
How to Build a Chicken Coop the simple way
#1 Tip For EASY SHELVING + QUICK BUILT-INS (Save Money $$ With This Trick)
How To Build a Simple Cheap Work Bench
How to Build a Simple, Sturdy Greenhouse from 2x4's | Modern Builds | EP. 58
How to BUILD CABINETS Fast and Easy - Frameless Plywood Cabinets
How To Build SIMPLE DIY STORAGE SHELVES
HOW TO Build an EASY DIY A-Frame Chicken Coop | Part #1 (Pallet Project)
How to Build Garage Shelving - Easy, Cheap and Fast!
Комментарии