filmov
tv
THIS Could Seriously HURT Aviation!
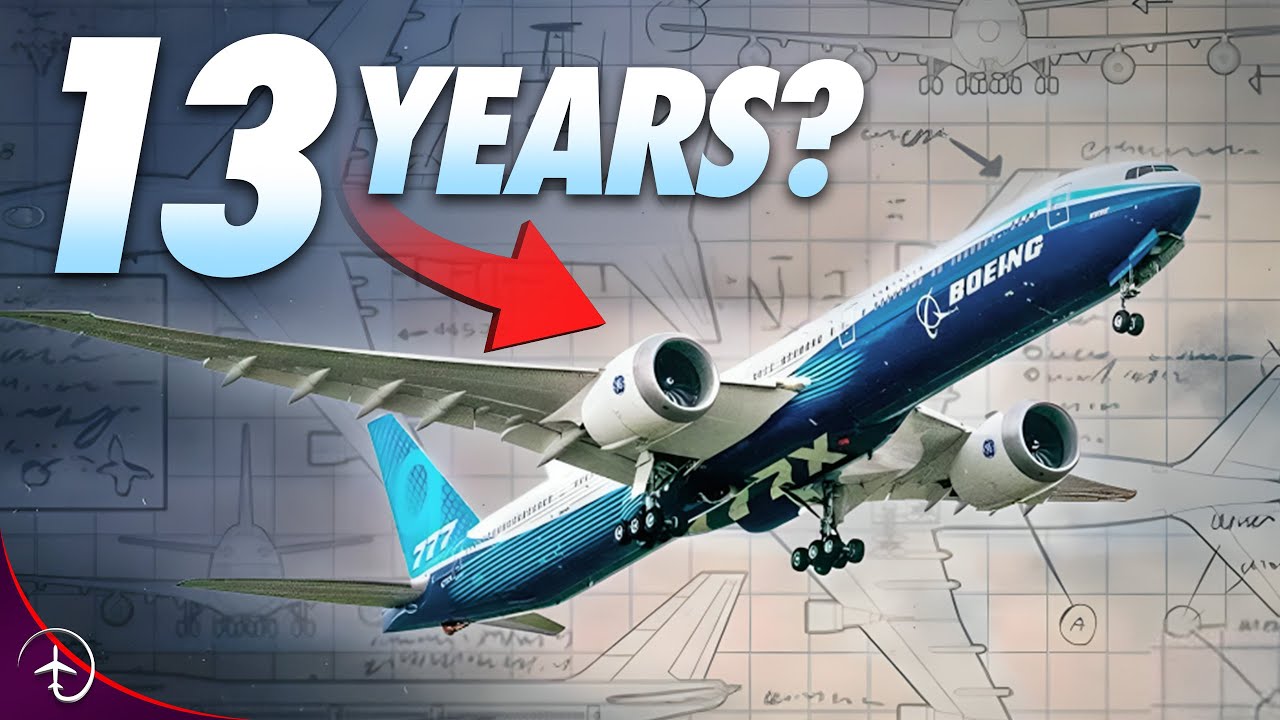
Показать описание
-----------------------------------------------------
Why is aircraft development getting so slow? How did we go from developing an all-new jetliner from scratch in three to four years in the 50s and 60s, to needing more than a decade to change a wing and the engines of an existing airliner in the 2010s and 2020s?
-----------------------------------------------------
If you want to support the work I do on the channel, join my Patreon crew and get awesome perks and help me move the channel forward!
Our Connections:
Social:
Download the FREE Mentour Aviation app for all the latest aviation content
Below you will find the links to videos and sources used in this episode.
SOURCES
-----------------------------------------------------
#Mentourpilot #pilot #boeing
Why is aircraft development getting so slow? How did we go from developing an all-new jetliner from scratch in three to four years in the 50s and 60s, to needing more than a decade to change a wing and the engines of an existing airliner in the 2010s and 2020s?
-----------------------------------------------------
If you want to support the work I do on the channel, join my Patreon crew and get awesome perks and help me move the channel forward!
Our Connections:
Social:
Download the FREE Mentour Aviation app for all the latest aviation content
Below you will find the links to videos and sources used in this episode.
SOURCES
-----------------------------------------------------
#Mentourpilot #pilot #boeing
THIS Could Seriously HURT Aviation!
This could Seriously Hurt the Aviation Industry!
What About The Old Planes…🥺 #aviation #sad #trend #shorts #nostalgia
Just HOW Badly DAMAGED is Boeing?!
'12 HUGE AVIATION STORIES!' Boeing, NASA, China, Russia, SpaceX, Danger In The Sky, Plus M...
Telling the Truth - Paid or Sponsored by Airlines?
Lufthansa flight 540 - What was supposed to happen 💔 - #avgeeks #pilot #aviation #flight #planes
Asiana airlines 214 - what was supposed to happen 💔 - #aviation #planes #avgeeks #airline #flight
Aloha Airlines #shorts #shortvideo #short #shortsvideo #shortsfeed #shortsviral #viralvideo #viral
Causes of plane crashes (Part 6) #plane #planecrash #aviation
The Last Words Of Pilots PT.7😔#shorts #aviation #planedisasters #sad
What Happens When an Arresting Cable Breaks on US Aircraft Carriers?
Animation vs Real Life - TAM Airlines Flight 3054 #planecrash
Nobody Was Seriously Hurt #aviation #crash #shorts
Why Airline Pilots Get Paid So Much ✈️💰
When a Pilot Misses Aircraft Carrier Landing
World's SAFEST Airlines
The Worlds Most DANGEROUS Airline: Aerosucre
747 then vs now… 🫡 - #aviation #planes #avgeeks #flight #747 #queenoftheskies
sounds pilot are scared of #aviation #automobile #plane #airlines #a330 #planecrash
Animation vs Real footage | Air France 296Q | #shorts #aviation #planecrash
Rc Airliner doing an awesome wheelie! #motionrc #aviation
How Banning Russian Airlines is Hurting Boeing #shorts
I Tested 1-Star Airlines
Комментарии