filmov
tv
Managed Pressure Drilling Automation: Challenges and Opportunities
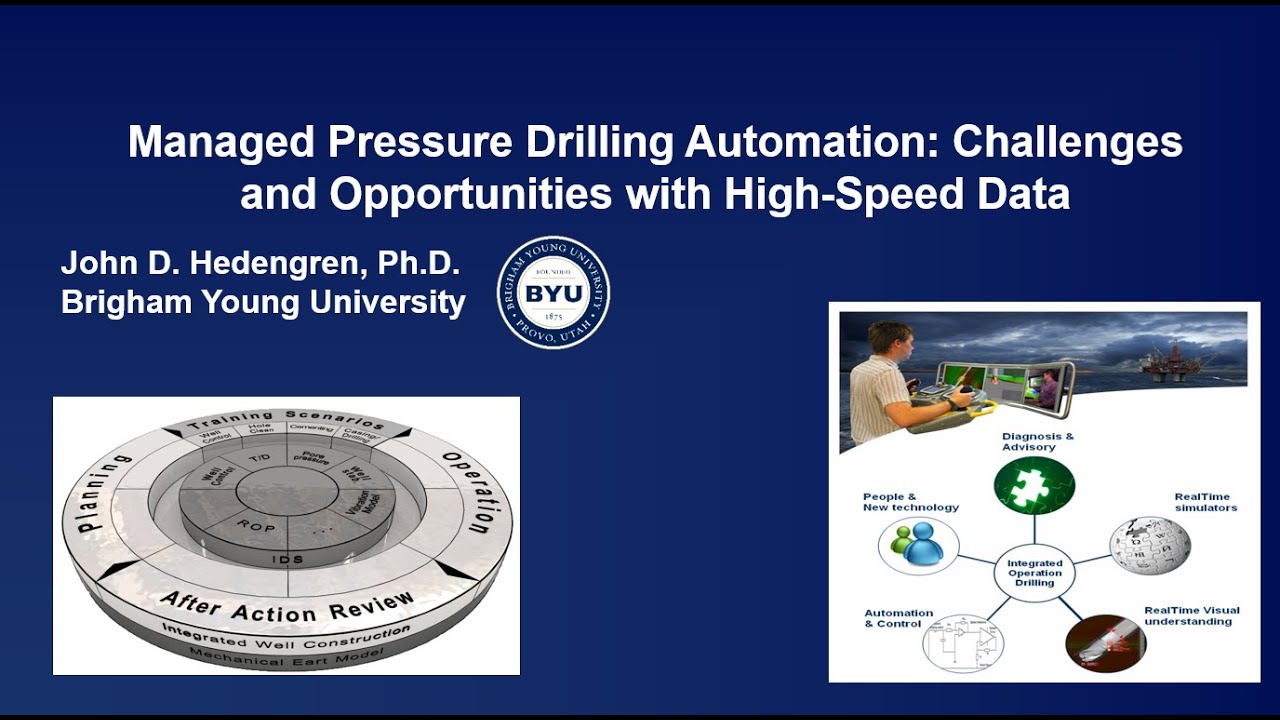
Показать описание
The drilling industry is facing challenging market conditions that motivate the use of automation to reduce costs and decrease well manufacturing variability. The objective of this presentation is to motivate automation initiatives that utilize high-speed data to directly measure downhole conditions or physics-based models for predictive monitoring and control. This presentation explores opportunities and challenges in well manufacturing by combining high-speed data and physics-based models to both estimate and control critical drilling conditions. Methods such as ensemble control automatically switch between high speed data, physics-based models, and lower-order models in a similar manner to redundant mechanical or electrical backup systems that increase uptime and reliability. The automation adjusts choke valve opening in the case of unexpected gas influx and to maintain pressure during drilling and connection procedures. Principles of smart manufacturing are being applied to achieve consistent and reliable performance. Two developments include reliable high speed data communication offered by wired drill pipe telemetry and advances in physics-based modeling of borehole hydraulics and drillstring dynamics. The approach to smart well manufacturing has the potential to reduce drilling costs and improve consistency, especially in Managed Pressure Drilling (MPD) where tight pressure control and maximized rate of penetration are key performance indicators. Automation case studies demonstrate the value of high speed data and predictive models in land and offshore drilling. In additional to a survey of the latest automation developments, several new ways of thinking about drilling control are discussed. For example, rate optimization and pressure control have traditionally been separate applications. Simulation studies suggest significant potential improvement when combining the two applications. New methods for automation and future directions are proposed for further development.
John Hedengren is an Assistant Professor in the Department of Chemical Engineering at Brigham Young University. He received a PhD degree in Chemical Engineering from the University of Texas at Austin. Previously, he developed the APMonitor Optimization Suite and worked with ExxonMobil on Advanced Process Control for 5 years. His primary research focuses on accelerating automation technology in drilling. Other research interests include fiber optic monitoring, Intelli-fields, reservoir optimization, and unmanned aerial systems. In addition to drilling automation, he is a leader of the Center for Unmanned Aircraft Systems (C-UAS), applying UAV computer vision and optimization technology to energy and infrastructure monitoring.
John Hedengren is an Assistant Professor in the Department of Chemical Engineering at Brigham Young University. He received a PhD degree in Chemical Engineering from the University of Texas at Austin. Previously, he developed the APMonitor Optimization Suite and worked with ExxonMobil on Advanced Process Control for 5 years. His primary research focuses on accelerating automation technology in drilling. Other research interests include fiber optic monitoring, Intelli-fields, reservoir optimization, and unmanned aerial systems. In addition to drilling automation, he is a leader of the Center for Unmanned Aircraft Systems (C-UAS), applying UAV computer vision and optimization technology to energy and infrastructure monitoring.