filmov
tv
Machine Learning and Physics-based Solutions for Drilling Automation
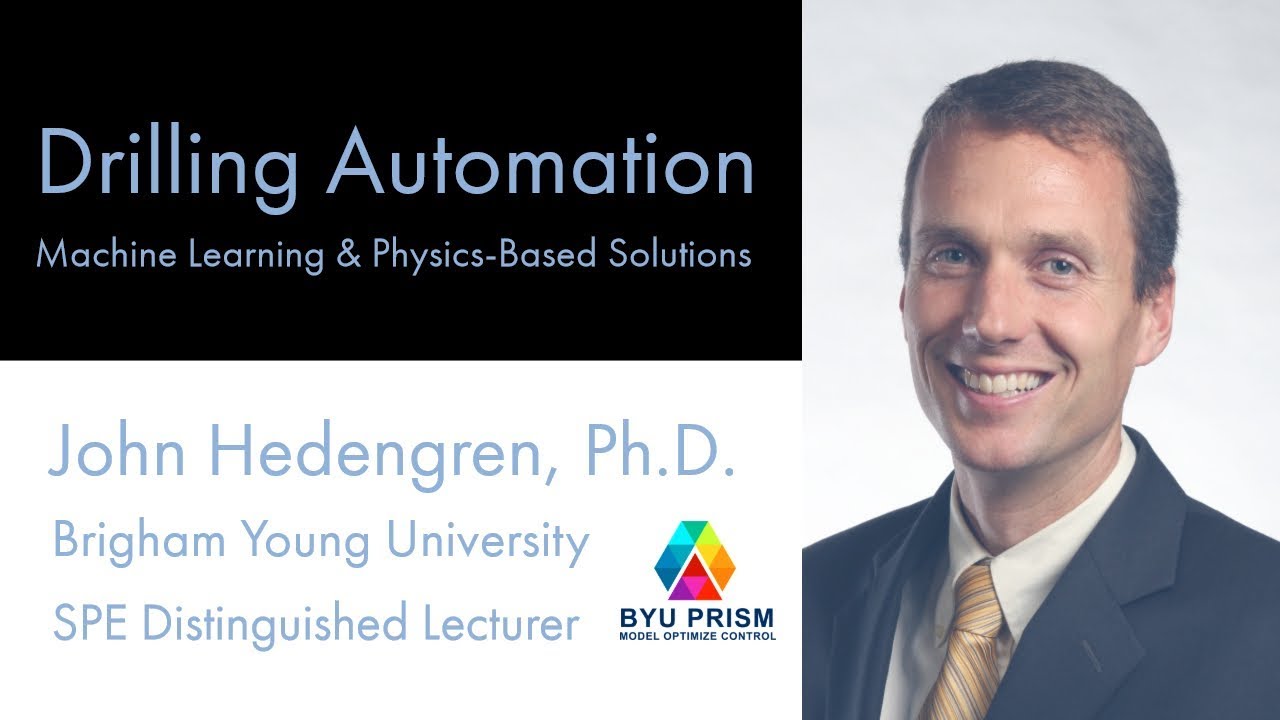
Показать описание
The drilling industry faces challenging market conditions that motivate the use of automation to reduce costs and decrease well manufacturing variability. The objective of this presentation is to motivate automation initiatives that utilize machine learning and physics-based models for predictive monitoring and control. This presentation explores current progress, challenges, and opportunities to control critical drilling conditions such as downhole pressure in Managed Pressure Drilling (MPD). The 3 essential elements of automation are explored with a perspective on recent advancements in automation due to downhole measurement availability through wired drillpipe. However, only a small fraction of drilling systems currently utilize wired drillpipe. In automated rig systems, there is additional potential to unlock the predictive capabilities of physics-based models to "see" into the near future to optimize and coordinate control actions. A convergence of several key technologies creates an opportunity to use sophisticated mathematical models within automation. A significant challenge is the size of the physics-based models that have too many adjustable parameters or are too slow in simulation to extract actionable information. This presentation shows how fit-for-purpose models can be used directly in the automation solutions. These fit-for-purpose models have unlocked new ways to think about automation in drilling. For example, rate optimization and pressure control have traditionally been separate applications in MPD. Simulation studies suggest significant potential improvement when combining the two applications.
John Hedengren is an Associate Professor in the Department of Chemical Engineering at Brigham Young University. He received a PhD degree in Chemical Engineering from the University of Texas at Austin. Previously, he developed the APMonitor Optimization Suite and worked with ExxonMobil on Advanced Process Control. His primary research focuses on accelerating automation technology in drilling. Other research interests include fiber optic monitoring, Intelli-fields, reservoir optimization, and unmanned aerial systems. In addition to drilling automation, he is a leader of the Center for Unmanned Aircraft Systems (C-UAS), applying UAV automation and optimization technology to energy infrastructure.
Pastusek, P., Payette, G., Shor, R., Cayeux, E., Aarsnes, U.J., Hedengren, J.D., Menand, S., Macpherson, J., Gandikota, R., Behounek, M., Harmer, R., Detournay, E., Illerhaus, R., Liu, Y., Creating Open Source Models, Test Cases, and Data for Oilfield Drilling Challenges, SPE/IADC Drilling Conference, The Hague, Netherlands, March 2019, SPE-194082-MS.
#SPEDL #ModelPredictiveControl #MachineLearning #DeepLearning
John Hedengren is an Associate Professor in the Department of Chemical Engineering at Brigham Young University. He received a PhD degree in Chemical Engineering from the University of Texas at Austin. Previously, he developed the APMonitor Optimization Suite and worked with ExxonMobil on Advanced Process Control. His primary research focuses on accelerating automation technology in drilling. Other research interests include fiber optic monitoring, Intelli-fields, reservoir optimization, and unmanned aerial systems. In addition to drilling automation, he is a leader of the Center for Unmanned Aircraft Systems (C-UAS), applying UAV automation and optimization technology to energy infrastructure.
Pastusek, P., Payette, G., Shor, R., Cayeux, E., Aarsnes, U.J., Hedengren, J.D., Menand, S., Macpherson, J., Gandikota, R., Behounek, M., Harmer, R., Detournay, E., Illerhaus, R., Liu, Y., Creating Open Source Models, Test Cases, and Data for Oilfield Drilling Challenges, SPE/IADC Drilling Conference, The Hague, Netherlands, March 2019, SPE-194082-MS.
#SPEDL #ModelPredictiveControl #MachineLearning #DeepLearning
Комментарии