filmov
tv
1300 Amp MOT Spotwelder - Fail
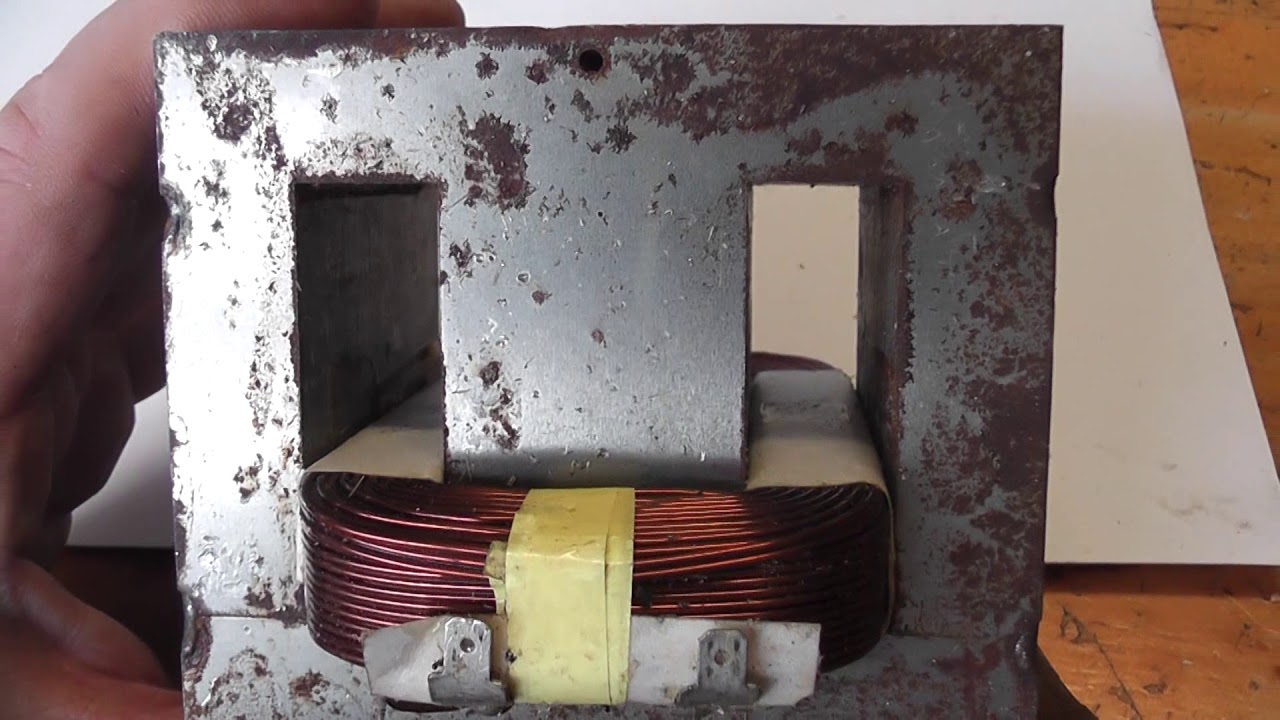
Показать описание
Experimental spotwelder with an old MOT and single turn secondary winding.
Plenty of heat but no metallic fusion.
The quality of the welds is not good. Soldering was marginal.
The current was exceeding my expectations.
0:06 Current readings
0:30 Preparations
1:16 Removing the HV windings
3:19 Fitting the Cu busbat
4:44 Testrun on Copper
5:32 Trying with solder
8:45 Rough weld
Plenty of heat but no metallic fusion.
The quality of the welds is not good. Soldering was marginal.
The current was exceeding my expectations.
0:06 Current readings
0:30 Preparations
1:16 Removing the HV windings
3:19 Fitting the Cu busbat
4:44 Testrun on Copper
5:32 Trying with solder
8:45 Rough weld
1300 Amp MOT Spotwelder - Fail
Testing my MOT Spot Welder 100 amp Spot Welder Control Circuit-Demonstration & Explanation
MOT SPOT-WELDER works now, but it didn't start that way!
Custom/DIY MOT spot welder.
18650 AC MOT spot welder
Making a Spot Welder from a Microwave!
Lipo 4s under/over volt super explosion💥💥
Handheld DIY Spot Welder Using MOT
Building a Spot Welder from a Microwave Transformer!
Quick DIY Spot Welder without microcontroller
HOMEMADE SPOT WELDER 1000 AMP 🦾🔧🔨 DIY Do-It-Yourself #1 Full HD 60fps
Modified MOT: playing with high current. (Part 2 of 4)
Big Home Made Spot welder Part 1 MOT to 140A Arc welder transformer
SPOT WELDER BUILD
How to make simple Welding machine with 3V 🔋, Working 100%
Las listrik rakitan dari trafo microwave 2 biji #trending
fail - home made spot welding machine for batteries
Home made Variable current spot welder
DIY Spot Welder [ not working to good ]
diy microwave spot welder - The Transformer
High current transformer experiment
microwave oven spot welder DIY build for 18650 battery tab welding, Part 1
How to make Spot Welder at home | Urdu, Hindi & English CC | DIY
Spot welder using toroidal transformer salvaged from audio power amplifier
Комментарии