filmov
tv
diy microwave spot welder - The Transformer
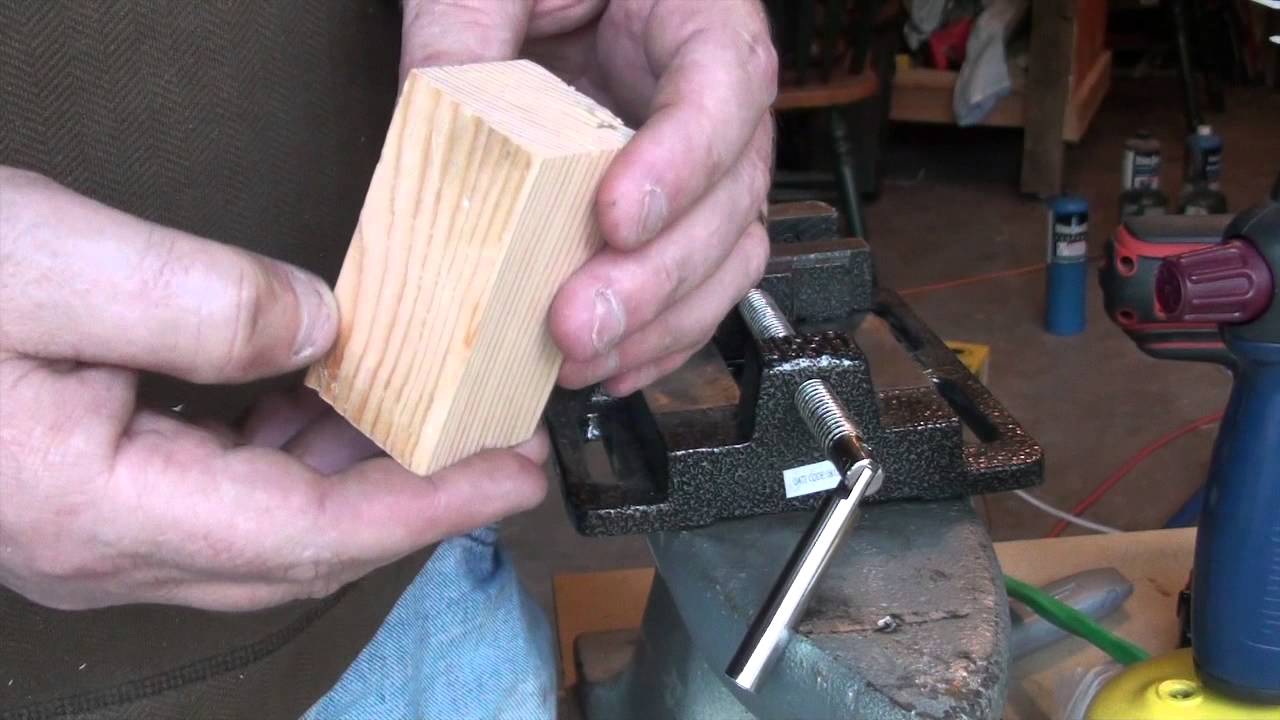
Показать описание
In this is video, i'm going to show you how
I extracted the big transformer from the microwave oven
and repurpose it for use as a spot welder.
I'll show you how I disasembled the transformer and rewired it to give a low
voltage and high current, then put it back to together.
I extracted the big transformer from the microwave oven
and repurpose it for use as a spot welder.
I'll show you how I disasembled the transformer and rewired it to give a low
voltage and high current, then put it back to together.
DIY 18650 battery Spot Welder! | Microwave Transformer
DIY Spot welder build - Cheapest out there! Part 1/2
18650 Battery Tab Spot Welding Machine using Microwave Transformer #shorts #short
How To Make Spot Welding Machine For 18650 Lithium-ion Battery From A Old Microwave Oven Transformer
DIY Spot Welder From Microwave Transformer | HOW TO
Spot Welding Machine | Weld Like a Pro at Home | DIY Microwave Oven Transformer!
DIY Spot Welding Machine For 18650 Lithium ion Cells.
DIY Spot Welder ( Part I )
Spot Welder - The 3 Best Value for Money Spot Welders 2025
DIY battery Spot Welder on the Cheap
Diy Spot Welder in action!
DIY Battery Spot Welder - Update & Demonstration
DIY Battery Spot Welder / Spot Welder Controller / Microwave Transformer 1
How to make Spot welding machine DIY with Microwave
How To Make Spot Welding Machine
DIY Spot Welder from a Microwave Transformer Easy & Powerful!
CHEAP DIY Spot Welder | Compared to $200 Sequre SQ-SW1
Building a spot welder from an old microwave.
INCREDIBLE Spot Welder DIY built with microwave
DIY or BUY a Battery Spotwelder?!
Mosfet Spot Welder Part 1/ DIY 18650 FB Group
Diy Spot Welder Microwave Oven Transformer(MOT)
A little flux makes spot welding 18650 lithium batteries fast & safe #flux #18650battery #solder...
Battery spot welder
Комментарии