filmov
tv
Inside Tesla’s Model 3 Factory
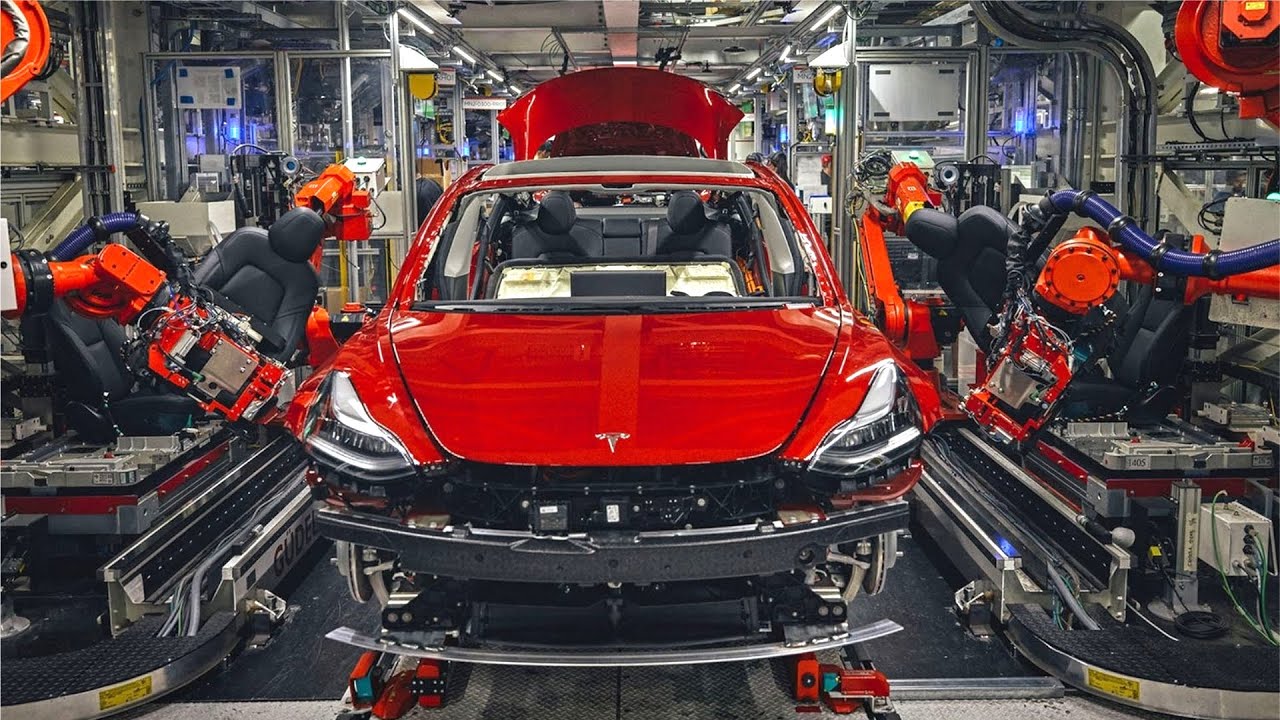
Показать описание
Inside Tesla’s Model 3 Factory
Stamping Tesla Model 3 uses a high-end Schuler servo stamping press to turn giant rolls of steel into Model 3 body parts. There are only 35 such presses in auto manufacturing worldwide, and Tesla says it is the first in the U.S. The equipment has allowed Tesla to crank out unique parts, like the Model 3 front fender, which engineers say has greater depth in a single piece of stamped steel than any other fender in production.
Assembly Putting together the pieces of the car’s body is an area that all automakers automate to varying degrees. However even state-of-the-art factories tend to rely on people to transport parts and load them onto the machines. Car parts are packed together for storage and shipping, and picking them back up is difficult without human fingers.
Seat Factory Car manufacturers hate seats. They're tedious to make and require different skills and materials than the rest of the car. It’s easier to outsource, and no major manufacturer does it all themselves. But relying on suppliers got Tesla into trouble with the Model X, when its engineers designed an extremely difficult-to-make “monopost” seat and an impossible-to-hit timeline. Problems with suppliers set production back by months, and Musk decided he wasn’t going to put up with it again.
Quality Control Tesla says it has 47 robots deployed in scanning stations throughout the body line. They measure 1,900 points in every Model 3 to match them to design specs—with a precision of 0.15 millimeters. Torque measurements are also automatically recorded for every bolt that’s fastened.
Stamping Tesla Model 3 uses a high-end Schuler servo stamping press to turn giant rolls of steel into Model 3 body parts. There are only 35 such presses in auto manufacturing worldwide, and Tesla says it is the first in the U.S. The equipment has allowed Tesla to crank out unique parts, like the Model 3 front fender, which engineers say has greater depth in a single piece of stamped steel than any other fender in production.
Assembly Putting together the pieces of the car’s body is an area that all automakers automate to varying degrees. However even state-of-the-art factories tend to rely on people to transport parts and load them onto the machines. Car parts are packed together for storage and shipping, and picking them back up is difficult without human fingers.
Seat Factory Car manufacturers hate seats. They're tedious to make and require different skills and materials than the rest of the car. It’s easier to outsource, and no major manufacturer does it all themselves. But relying on suppliers got Tesla into trouble with the Model X, when its engineers designed an extremely difficult-to-make “monopost” seat and an impossible-to-hit timeline. Problems with suppliers set production back by months, and Musk decided he wasn’t going to put up with it again.
Quality Control Tesla says it has 47 robots deployed in scanning stations throughout the body line. They measure 1,900 points in every Model 3 to match them to design specs—with a precision of 0.15 millimeters. Torque measurements are also automatically recorded for every bolt that’s fastened.
Комментарии