filmov
tv
EEVblog 1409 - The DANGERS of Inductor Back EMF
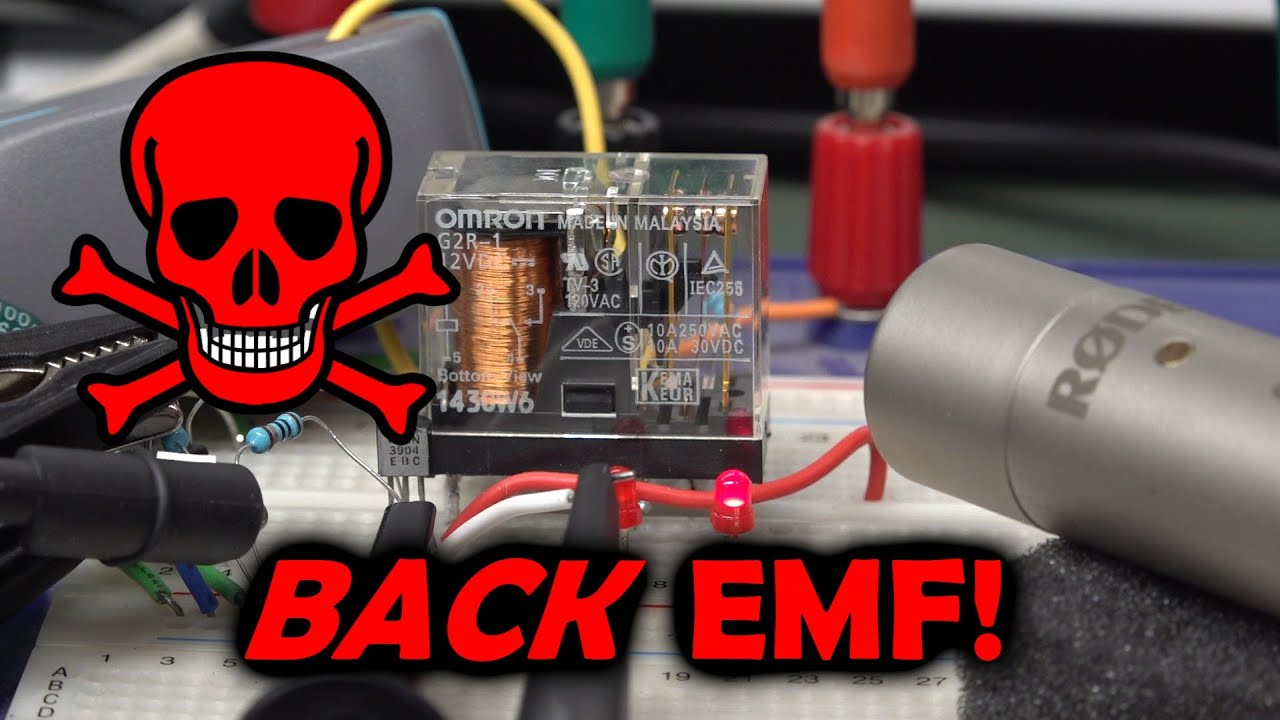
Показать описание
A practical demonstration of Lenz's law and back EMF in an inductive relay coil and how to solve it using a Freewheeling/Flywheel/Flyback/Snubber/Clamp diode. Also the downsides of clamping diodes, and switch arcing supression.
Also a look at an AMAZING potential phenomenon you probably haven't seen before!
Actually, two rather cool things you probably haven't seen before.
Along with transistor ratings, transistor storage current, and Collector-Emitter breakdown voltage, there is a lot to unpack in this video.
This is a follow-on from the DC Transients Fundamentals video:
00:00 - Recap of Relays, Inductors, Faraday & Lenz's Laws
02:30 - Relay Back EMF Explained
07:09 - The Flywheel analogy of Inductors
08:30 - Relay circuit demonstration
12:35 - 700V Back EMF!
14:43 - BJT Transistor Storage Time
17:03 - Back EMF Diode clamp demonstrated
19:06 - An AMAZING demonstration!
24:43 - Trap for young players
25:23 - DOWNSIDES of Back EMF Diodes
28:38 - BONUS cool effect of Back EMF diode DEMONSTRATED
Buy anything through that link and Dave gets a commission at no cost to you.
Donate With Bitcoin & Other Crypto Currencies!
#ElectronicsCreators #Tutorial #Inductors
Also a look at an AMAZING potential phenomenon you probably haven't seen before!
Actually, two rather cool things you probably haven't seen before.
Along with transistor ratings, transistor storage current, and Collector-Emitter breakdown voltage, there is a lot to unpack in this video.
This is a follow-on from the DC Transients Fundamentals video:
00:00 - Recap of Relays, Inductors, Faraday & Lenz's Laws
02:30 - Relay Back EMF Explained
07:09 - The Flywheel analogy of Inductors
08:30 - Relay circuit demonstration
12:35 - 700V Back EMF!
14:43 - BJT Transistor Storage Time
17:03 - Back EMF Diode clamp demonstrated
19:06 - An AMAZING demonstration!
24:43 - Trap for young players
25:23 - DOWNSIDES of Back EMF Diodes
28:38 - BONUS cool effect of Back EMF diode DEMONSTRATED
Buy anything through that link and Dave gets a commission at no cost to you.
Donate With Bitcoin & Other Crypto Currencies!
#ElectronicsCreators #Tutorial #Inductors
Комментарии