filmov
tv
EEVblog #682 - Ness D16X Alarm Panel Repair
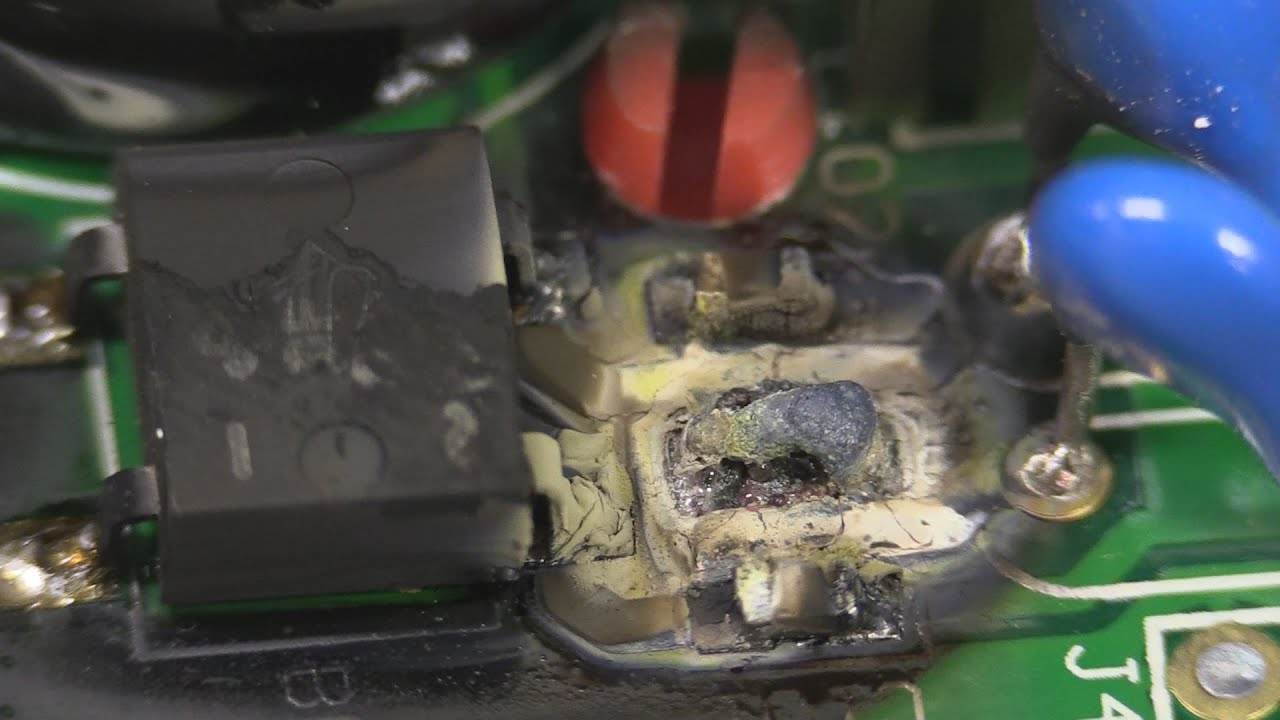
Показать описание
Part teardown, part repair, Dave looks at an Australian designed and manufactured Ness D16X alarm panel that has failed.
What's that smell?
Can it be fixed?
How do you repair solder mask on a PCB?, or add solder mask to your own home etched PCB's?
And another look at PCB spark gaps.
Datasheets:
Fujitsu H8/538
Holtek DTMF Receiver
Maxcap Capacitors:
Epcos MOVs
Support the EEVblog through Patreon!
EEVblog Amazon Store (Dave gets a cut):
Donations:
Projects:
Electronics Info Wiki:
What's that smell?
Can it be fixed?
How do you repair solder mask on a PCB?, or add solder mask to your own home etched PCB's?
And another look at PCB spark gaps.
Datasheets:
Fujitsu H8/538
Holtek DTMF Receiver
Maxcap Capacitors:
Epcos MOVs
Support the EEVblog through Patreon!
EEVblog Amazon Store (Dave gets a cut):
Donations:
Projects:
Electronics Info Wiki:
EEVblog #682 - Ness D16X Alarm Panel Repair
EEVblog #684 - Ness SMT Manufacturing & Assembly Factory Tour
EEVblog #763 - Dumpster Plasma TV Bad Cap Repair
EEVblog #688 - How To Rework Solder SMD Chips - BTTF Time Circuits Repair!
EEVblog #681 - More Solar Roadways BULLSHIT!
EEVblog #1219 - Don't Trust Switches - Toy Repair
eevBLAB #3 - Engineers Can't Spell
EEVblog #673 - Mailbag
EEVblog #680 - Mailbag
eevBLAB #1 - The EEVblog Is Hiring
EEVblog #918 - REPAIR: Sony Pyxis GPS
EEVblog #693 - AVO Transistor Analyser Teardown
EEVblog #683 - Rigol DS1000Z & DS2000 Oscilloscope Jitter Problems
EEVblog #717 - How To Hack Vacuum Fluorescent Displays
EEVblog #1195 - Sony 4K 60' LCD TV Audio Repair
EEVblog1460 - REPAIRING a LED Studio Light with a DUMPSTER LAPTOP!
EEVblog #1258 - MORE Dumpster Wandel And Goltermann!
EEVblog #1036 - PSU Fire PCB Repair
EEVblog #719 - Sony Low Noise Audiophile SDXC Memory Card
EEVblog #825 - Your Printer Is Spying On You!
EEVblog #694 - Mailbag
When a simple repair becomes longer than expected
EEVblog #539 - RFID Tag Card Repair
EEVblog #690 - TDS220 Oscilloscope Autopsy
Комментарии