filmov
tv
Oceangate Titan Submersible Manufacturing and Engineering Issues Part 1
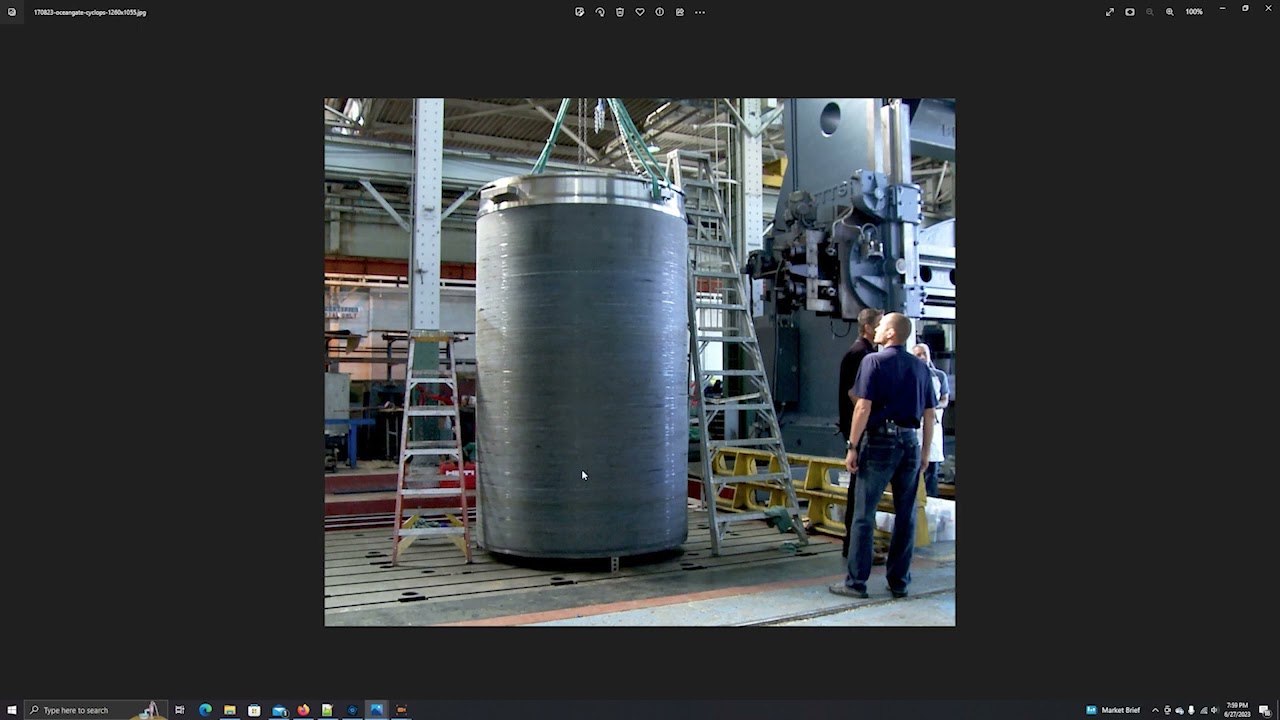
Показать описание
Oceangate video on filiment winding
Watch The Manufacturing Process That DOOMED OceanGates Titan To Fail. But It NEVER Had To Happen.
Oceangate Titan Submersible Manufacturing and Engineering Issues Part 1
The making of Titan: Oceangate's submersible capable of taking people to the Titanic
Titan Submarine Debris Clues, Implosion Simulation
Titan Sub | carbon fiber - Detailed Tour
The Questionable Engineering of Oceangate
Titan Sub Implosion Causes OceanGate Titanic Expedition
Why OceanGate Titan Imploded - A Carbon Fiber Composites Perspective
James Cameron on 'fundamental flaw' in design of Titan submersible
Exposing OceanGate Submarines Many Fatal Designs
Ocean Gate: The Search For The Truth (Full Documentary)
Exclusive Footage inside Titan Submarine expedition
David Pogue revisits experience with Titan sub crew and OceanGate’s CEO Stockton Rush #shorts
Engineering Failures Behind Titan’s Implosion!
Oceangate Titan Submersible Manufacturing and Engineering Issues Part 2
How They Close OceanGate Titan submersible BOLTS AND NUTS!
Titan Submersible Hearings
Oceangate 2024: The world's first multi-physics simulation of the Oceangate TITAN
NTSB Titan Sub Report: Carbon Fiber Hull Defects, More
Missing Sub: Former Titan passenger 'couldn't get comfortable with design'
“The Whole Thing Was A Botched Job” OceanGate Whistleblower Had ‘No Confidence’ In Manufacturing...
How Titan was Built, Lost and Found: An Analysis
Why the Titan sub failed
OceanGate Titan Sub Debris Video Shows How It Imploded
Комментарии