filmov
tv
What is DCS? (Distributed Control System)
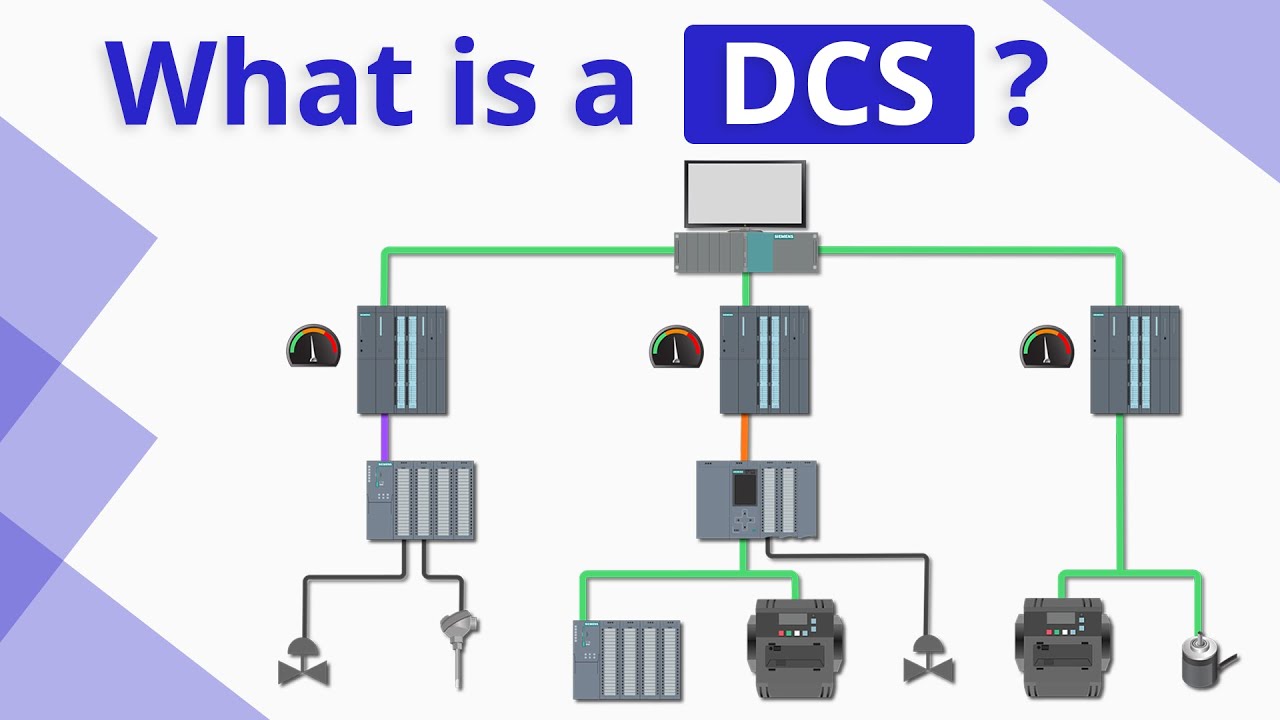
Показать описание
▶ Check out the full blog post over at
=============================
Over the years, the term DCS has evolved from the original description for the acronym as a Distributed Control System to the use of the term Decentralized Control System and they seem to be somewhat interchangeable nowadays.
Briefly, as a point of the historical review, when PLC’s were invented, they were really good at handling single processes and were primarily used for repetitive, discrete control.
The advent of the DCS was for controlling many autonomous controllers that handled many continuous operations, mainly using analog control.
PLCs, traditionally, were used for single batch or high-speed control, have a relatively simple, low-cost design, and are the core of the system.
Processing time for tasks are typically very fast, operators usually interact and control the system using some sort of graphical display such as SCADA.
A DCS is used for continuous, complex controls, have an integrated control center much like a SCADA, which is the core of the system versus the processors in a PLC system.
The DCS has a number of predefined functions. Processing times are somewhat slower. Operators interact with the control system via an integrated graphical display.
DCS’s also have a claim that when safety is a top priority, the DCS is the most reliable system.
Redundancy may be deployed in either the PLC or DCS applications. You could employ redundant components to negate the possibility of process shutdowns.
Now that we’ve touched on some of the differences in the systems, let’s focus on the DCS and some of its components.
A typical plant starts with a centralized operator control center typically called Operator Stations.
This is where the operator can observe the operations of the plant, view process warnings and alarms, monitor production, and more.
The next level of components may contain servers, archiving computers, and engineering stations.
Communications with the Operator Station level is typically Industrial Ethernet.
Servers are used for the collection of data at the processor level.
Archiving computers are used for storing historical data that may be used for trends or compliance.
Engineering stations are used for creating the projects on which the processes run.
At the next level, you have the master controllers that supervise the individual processors as well as I/O modules.
The next level is the field device level.
Communications between this level and the processor level can be nearly any type that may be compatible with the components.
Components at this level would be devices such as transmitters, switches, valves, motors, remote or distributed I/O, etc.
In short, both PLCs and a DCS have their place in the market today.
PLCs would work best in a small production environment where component failure if no redundant system is deployed, is a small risk for the application, the budget is restricted, or the tasks and I/O count are minimal.
A DCS would be better used in an environment where there are large I/O counts with many continuous processes, a processor failure in one section of the plant is not a problem for production, or risk assessment has determined that an integrated package would be the best option.
=============================
Missed our most recent videos? Watch them here:
=============================
To stay up to date with our last videos and more lessons, make sure to subscribe to this YouTube channel:
=============================
=============================
#RealPars #DCS #DistributedControlSystem
Комментарии