filmov
tv
Easy Improvements For Your Lathe And Mill!
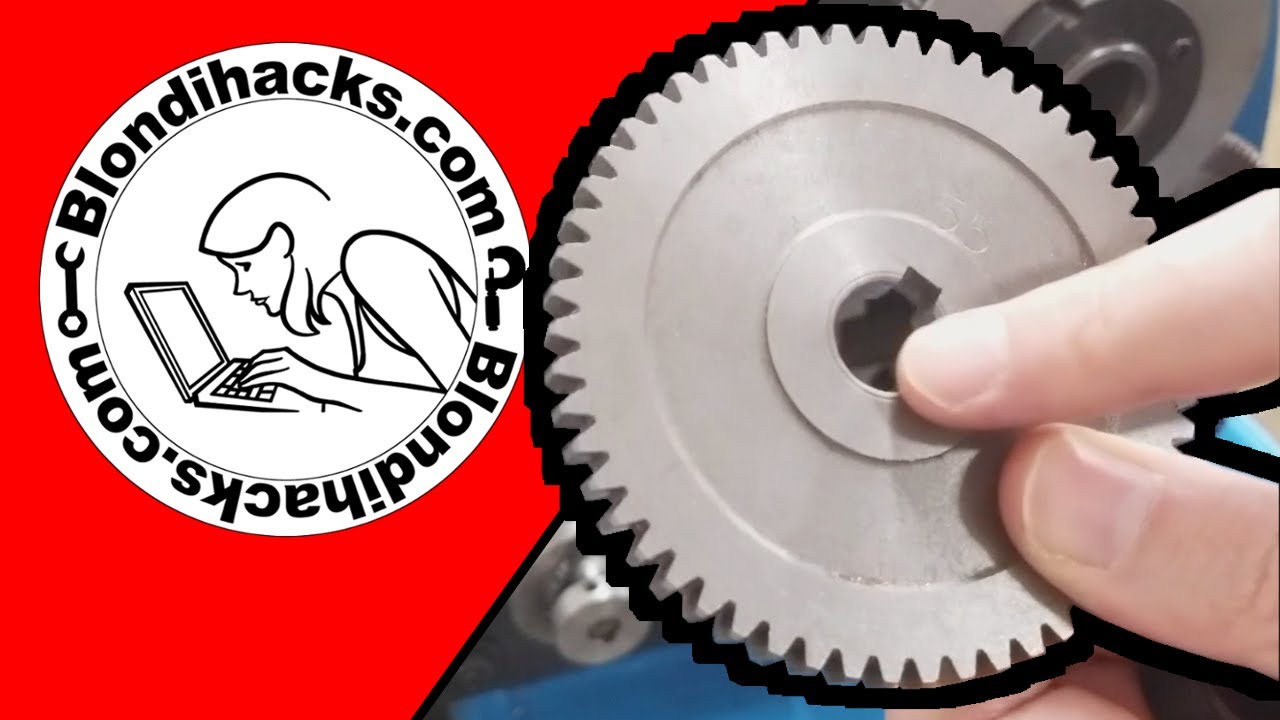
Показать описание
This episode on Blondihacks, I'm sharing a few of the things I've done to improve life with my hobby machine tools! Exclusive videos, drawings, models & plans available on Patreon!
Here are links for many of the tools that you see me using:
(I earn small commissions on these links)
Want more content like this? Try these places:
As an Amazon Associate, I earn from qualifying purchases.
Here are links for many of the tools that you see me using:
(I earn small commissions on these links)
Want more content like this? Try these places:
As an Amazon Associate, I earn from qualifying purchases.
Easy Improvements For Your Lathe And Mill!
More Easy Improvements For Your Lathe and Mill
20 Best Mini Lathe Upgrades And Improvements
The 6 Best Lathe Projects For Beginners
10 More Mini Lathe Mods And Upgrades - 2022
Essential Mini Lathe Tools And Accessories
Essential MINI Lathe Upgrades
Simple Project Will Save Time on the Lathe
High Definition Plasma Makes Fabrication Easy!
Mini lathe add-ons and upgrades
Simple Portable Lathe | Japanese Woodworking
10 Years of Mini Lathe Ownership: Pros, Cons, Modifications and Improvements
Best UPGRADES on a Mini Lathe
7 MORE Mods and Improvements for a Metal Lathe!
7 Mods and Improvements for a Metal Lathe
Making Lathe MILLING Tool Attachment at home
mini lathe upgrades
Some UPGRADES for the Lathe || INHERITANCE MACHINING
Get the Most Out of Your Lathe With The Perfect Hollower™
New lathe tools #tapanddie #powertap #lathe #newtools #machinist
Best Metal Lathe Under 1000: Top Products In Your Budget
Portable Lathe Drill
Quick Change Lathe Chucks
How To Align Your Lathe
Комментарии