filmov
tv
20 Best Mini Lathe Upgrades And Improvements
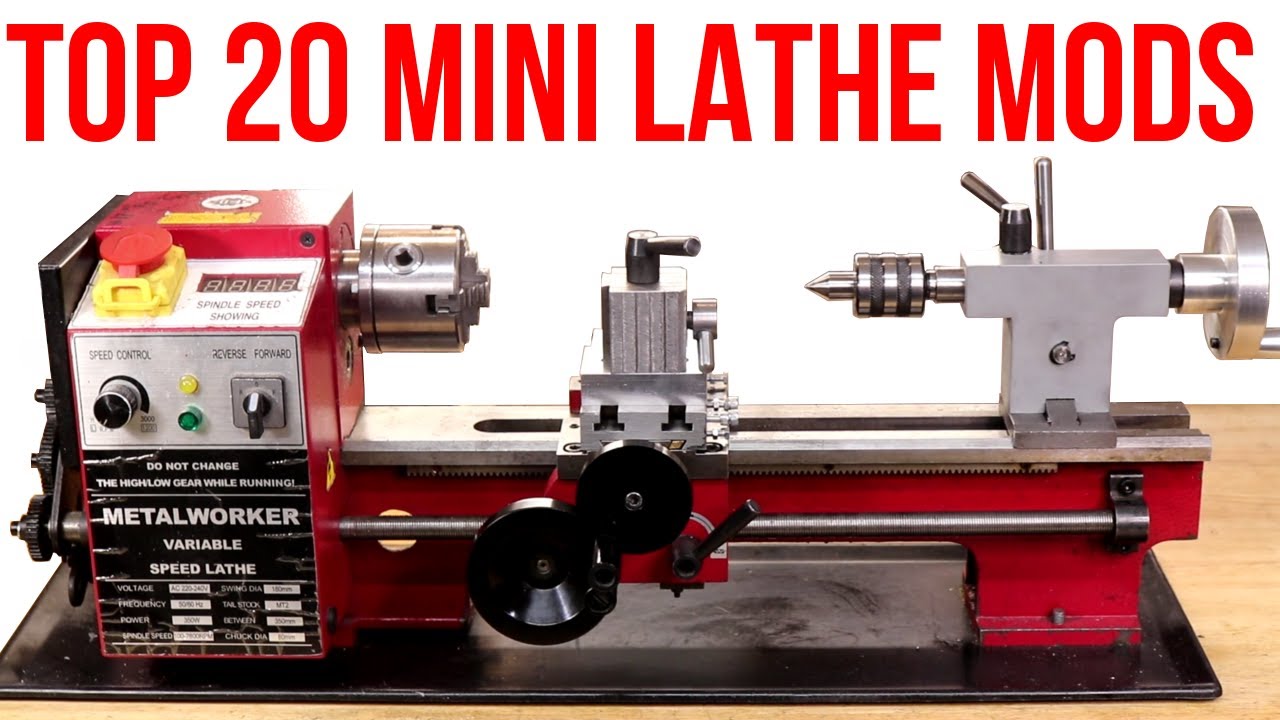
Показать описание
G'day everyone,
I have owned my import mini lathe (sieg c3) for over 2 and a half years at this point. I think it is a very capable little machine, and considering the price that I paid, the parts that it can produce are very decent. It can even turn steel with over a 1mm depth of cut.
However to get to this point I have had to make several modifications and upgrades, in order to fix issues from the factory, and expand the capabilities of the lathe.
In this video I will be showing you all the upgrades I have done to the lathe over the past 2 1/2 years. Some of the mods I have shown here on the channel before, and they are linked as follows.
Timestamps
0:00 - Intro
0:35 - Bolt The Lathe Down
1:10 - Quick Change Tool Post
2:27 - Replace The Handwheel
3:56 - Carriage Lock
5;01 - Slide Locks
5:49 - Replace The Carriage Retainer Strips
6:52- Solid Tool Post
7;36 - Replace The Chuck
8:29 - Upgrade The Spindle Motor
9:32 - Tapered Roller Bearings
10:36 - Brass Gib Strips
11:26 - Lever Lock Tailstock
12:15 - Tailstock Base Plate Scraping
12:50 - Apron Gear Cover
13;57 - Oiler Ports
14:41 - Top Slide Leadscrew Fix
16;13 - Spring Under Tailstock
16:26 - Level The Tailstock
16;52 - Rebuild The Cross Slide
17:24 - lapping The Slides
18:02 - Conclusion
#machining #minilathe #workshop
I have owned my import mini lathe (sieg c3) for over 2 and a half years at this point. I think it is a very capable little machine, and considering the price that I paid, the parts that it can produce are very decent. It can even turn steel with over a 1mm depth of cut.
However to get to this point I have had to make several modifications and upgrades, in order to fix issues from the factory, and expand the capabilities of the lathe.
In this video I will be showing you all the upgrades I have done to the lathe over the past 2 1/2 years. Some of the mods I have shown here on the channel before, and they are linked as follows.
Timestamps
0:00 - Intro
0:35 - Bolt The Lathe Down
1:10 - Quick Change Tool Post
2:27 - Replace The Handwheel
3:56 - Carriage Lock
5;01 - Slide Locks
5:49 - Replace The Carriage Retainer Strips
6:52- Solid Tool Post
7;36 - Replace The Chuck
8:29 - Upgrade The Spindle Motor
9:32 - Tapered Roller Bearings
10:36 - Brass Gib Strips
11:26 - Lever Lock Tailstock
12:15 - Tailstock Base Plate Scraping
12:50 - Apron Gear Cover
13;57 - Oiler Ports
14:41 - Top Slide Leadscrew Fix
16;13 - Spring Under Tailstock
16:26 - Level The Tailstock
16;52 - Rebuild The Cross Slide
17:24 - lapping The Slides
18:02 - Conclusion
#machining #minilathe #workshop
Комментарии